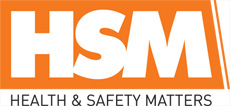
![]() |
Mark Sennett
Managing Editor |
![]() |
Kelly Rose
Editor |
Home> | Managing Health & Safety | >Decontamination Showers | >Hughes promises top quality |
Hughes promises top quality
06 September 2021
SAFETY SHOWERS and eye wash equipment must be reliable, robust, and work first time, every time, to protect lives.

Hughes’ rigorous approach to delivering high-quality products is evident throughout its manufacturing processes. The company is audited to ISO standards, namely 45001:2018, 14001:2015 and 9001:2015.
Nozzle
The Hughes nozzle is the result of meticulous research and development.
Extensive investigation was carried out to gain a clear understanding of how nozzles and roses perform and deliver water. International and European standards on safety shower spray patterns were assessed to ensure that our nozzle would meet recommendations for full decontamination, for example:
-
BS EN 15154 requires that the spray pattern must have a minimum diameter of 50.8cm (20 inches) at 152.4 (60 inches) from the surface on which the user stands. The flushing fluid needs to be substantially dispersed throughout the pattern. Safety shower heads must be capable of delivering 75.7litres/min (16.65 imperial Gallons/min) at a velocity low enough to be non-injurious to the user.
-
ANSI Z358.1-2014 requires the diameter of the spray pattern to be a minimum 400mm (16 inches) at 700mm (27 inches) below the shower head. Emergency shower heads must have a flow rate of 60 litres per minute.
Using this information, the nozzle was designed using the latest Computational Fluid Dynamic (CFD) software to maximise its performance and effectiveness. This design passed extensive testing and the currently features:
-
Internal baffle plate to spin and mix the water providing an even spray pattern distribution
-
Baffle plate creates back pressure and restricts flow at increasing pressures to ensure its non-injurious
-
Higher velocity spray to maximise wash off time with minimal water volume
-
A hole in the centre controls the velocity and flow of water through the nozzle, resulting in an ANSI and EN compliant spray pattern
-
Funnelled outlet mixes the water and removes any cavitation.
Materials of construction
Only the highest quality materials are used in the manufacture of its products. This ensures that showers are reliable, perform to or above expectations and stand the test of time.
Galvanized mild steel
Galvanising is a process where a protective zinc coating is applied to steel piping. This offers two methods of corrosion reduction:
-
It coats the surface like paint, and under most circumstances forms a very adherent oxide layer.
-
It provides a sacrificial anode (zinc) to receive corrosion rather than the steel corroding.
Galvanizing is ideal for safety showers as it can easily withstand repeated and rapid changes between being wet and dry. Due to its unique metallurgical bond, the galvanized coating is also incredibly tough. Galvanized steel is also immune to UV rays, so it won’t degrade in direct sunlight.
Stainless steel
Stainless steel is a low carbon steel which contains chromium at 10% or more by weight. It is the addition of chromium that gives the steel its unique corrosion resisting properties.
Galvanised steel and stainless steel share the same rigidity, strength, flammability, and UV resistance, yet stainless steel has even higher corrosion resistant capabilities.
Powder coated galvanised steel
With all the great properties of galvanised steel, the added powder coating provides an additional protective barrier that helps prevent corrosion. Powder coating is also chip resistant and better for the environment than liquid paint.
It is also easy to clean, ideal for a laboratory setting.
GRP
The company's tank showers and many of its optional fittings are manufactured using glass reinforced plastic (GRP).
GRP is an extremely versatile material and has a lot of great features:
-
Low maintenance
-
Slip resistant
-
Non-corrosive
-
Weather-proof
-
Lightweight
-
Non-conductive
Valves
The stainless steel and brass ball valves used in most of its products are designed to comply with ANSI Z358.1-2014 and EN15154 and certified to DIN EN 13828 and W 570-1. The valve features a bore in the ball to prevent the build-up of biofilm by allowing trapped water to be flushed away. The lever design offers integrated pick-up points for proximity/limit switch activation.
The company has several more specialised valves:
-
Pressure reducing valve - designed to regulate water supply pressure. Higher upstream pressure is reduced to give a lower constant downstream pressure, regardless of the varying force. Pressurisation damage is avoided, and water consumption is reduced.
-
Thermostatic mixing valve – for accurate control and maintenance of the water temperature of safety showers and eye wash equipment. The thermostatic mixing valve delivers a steady temperature despite varying pressure conditions.
-
Scald and freeze protection valves – these valves have gone through rigorous temperature and pressure testing to ensure reliable performance. The paraffin actuators are also the fastest reacting for temperature, delivering a swift response.
Protecting the safety of employees at risk of exposure to hazardous materials in the workplace is Hughes Safety Showers' first and greatest responsibility.
- Anaerobic digestion plants
- Managing tepid water on challenging sites
- Safety showers at wastewater treatment plants
- Protecting workers with safety showers
- Mitigate common dangers in the pulp and paper industry
- Showers boss shares secrets of success
- Safety showers for the fertiliser industry
- Refinery specifies decontamination shower
- Nick Clegg visits Hughes
- Are you serious about safety?