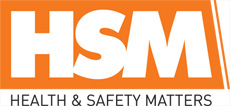
![]() |
Mark Sennett
Managing Editor |
![]() |
Kelly Rose
Editor |
Home> | Managing Health & Safety | >Decontamination Showers | >Protecting workers with safety showers |
Protecting workers with safety showers
04 April 2024
As demand for electric vehicles increases, demand for lithium-ion batteries follows. Due to the nature of the hazards involved in the production, battery gigafactories are considered to be high-risk environments.

Lithium-ion batteries are formed of four main components.
- The capacity of the battery is determined by the cathode - it's the source of the lithium ions.
- The ions are stored in the anode, which enables the electric current to flow through an external circuit when the battery is charged.
- The separator is the physical barrier that keeps the cathode and anode apart.
- The electrolyte acts as a conduit of lithium ions between the cathode and anode.
Before a battery can be installed, the factory must charge and test the unit to identify any faults. It can become faulty when mishandled, overcharged, short-circuited or heated up - leading to issues such as the battery walls expanding or splintering, which can allow some of the internal compounds to leak out.
Electrolytes are made up of organic compounds, such as salts and solvents. When contained inside a battery unit, the electrolyte doesn't pose an immediate risk. If they spill from a battery, because of an accident or if they're handled improperly, they can react with air and water to produce hydrofluoric acid - which poses a significant risk.
Battery gigafactories are extremely complex facilities, with a variety of different conditions. From manufacturing areas featuring extremely high temperatures and little to no humidity for the drying process, to clean rooms with high filtration levels to reduce the presence of dust particles.
Naturally, PPE is absolutely imperative, including head, face, respiratory and hand protection. However, emergency procedures must be in place if there is an accidental leak. This is where safety showers and eye/face washes play such an important part in keeping workers safe. They offer an immediate line of defence against the dangers of hazards, like hydrofluoric acid in the gigafactory environment.
To thoroughly decontaminate in the event of corrosive spills, EN15154 regulations state those affected should flush the skin or eyes for at least fifteen minutes. The water delivered should be tepid (between 15°C and 37°C), and comply with a designated flow rate (depending on its class).
By flushing away chemical contaminants and minimising the effects caused by chemical exposure, safety showers have a vital part to play in the lithium-ion car battery boom.
For more information, visit www.hughes-safety.com
- Emergency safety showers in wastewater treatment
- Alleviate construction site hazards
- Weekly activation of emergency safety shower
- Managing Legionella risk in emergency safety showers
- Drilling down into chemical hazards in the mining industry
- Protect your investment with regular maintenance and servicing
- Refinery specifies decontamination shower
- On-site legionella testing
- Are your safety showers ready for winter?
- Spare parts from Hughes