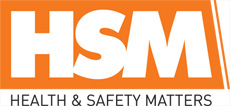
![]() |
Mark Sennett
Managing Editor |
![]() |
Kelly Rose
Editor |
Home> | Managing Health & Safety | >Decontamination Showers | >Going to extremes |
ARTICLE
Going to extremes
14 July 2014
As the global search for oil, gas and other natural resources reaches increasingly inhospitable environments, contractors must source equipment that can withstand and operate reliably in extreme environmental conditions. Taking the example of safety showers Janet Dickinson looks at some of the environmental factors oil, gas and utility plants need to take into consideration when specifying their safety equipment.
The extraction of oil, gas and other natural resources, which previously concentrated on areas such as the North Sea, now encompasses countries ranging from the freezing extremes of Kazakhstan and Alaska to the heat of the Middle East. Breakthroughs in drilling techniques mean it is now possible to operate in temperatures from minus 40 degrees centigrade up to 40 degrees centigrade.
Fortunately for the welfare of workers even in the emerging markets, health and safety requirements surrounding quick, effective decontamination are getting tougher with companies having to meet strict specifications and compliance to the ANSI Z358.1-2009 International standard. Such requirements are encouraging operators and specifiers to look more closely at a product's quality.
Getting it right for the right environment
When specifying the right safety shower for the environment a good starting point is to look at your water supply. If you can't connect directly into a reliable mains water supply then you require a self-contained unit. Gravity fed tank showers, for example, provide a guaranteed supply and instant tepid water. They are not affected by water interruptions or electricity failure making them operationally efficient and cost effective. Units are built entirely of GRP and Stainless Steel which ensures that they are corrosion resistant and easy to maintain.
You then need to look at the environment. In very hot countries, where the water supply feed is exposed to extreme heat, the water would be heated naturally by the sun to a dangerously high temperature. If the water was to remain at this temperature, it could cause or increase injury to the user.
In situations where the contaminant is a burn-inducing chemical, the hot water would intensify the burns and cause the substance to be absorbed further into the skin's pores.
At the other end of the scale, to suddenly douse someone with freezing cold water would not only shock them but could also give them hypothermia. The pores would close immediately, trapping the contaminant therefore hampering attempts to wash it off.
We don't believe that the 15 minute tepid water drench time as recommended by the ANSI.Z358.1 standard is enough when working with potentially harmful substances so our water cooling and heating methods go beyond this.
In hot climates the provision of a chiller unit, coupled to a tank shower, reduces the water to the recommended 20°C. The chiller only activates when the incoming water exceeds this temperature, when the water has been cooled to the correct temperature the unit deactivates. Chiller units can be fitted to any tank shower.
In cold climates, where temperatures reach down to minus 40 degrees, the water supply needs to be heated to 20 degrees. Tank showers which have the capacity and capability to provide tepid water instantly for durations in excess of the recommended 15 minutes allow for more difficult chemical substances to be washed off while ensuring casualties don’t suffer thermal shock. Water is heated by means of a thermostatically controlled immersion heater which keeps the water to a constant 'tepid' temperature as recommended by ANSI Z358.1-2009. This energy efficient system uses a 3kw immersion heater making it economical and delivering immediate first aid. Tankless systems can take vital seconds for the water to become tepid resulting in the initial delivery of water being cold causing the casualty to suffer thermal shock. Also achieving the required flow rate of 76 litres per minute instantaneously can be expensive and require power supplies of up to 110 Kw.
Moving away from dry land to the sea, safety showers on oil and chemical tankers have to meet different design specifications to those on oil and gas fields.
The units need to soak up huge wave momentum, while delivering an uninterrupted flow of water to wash away hazardous spills and materials. The water tank of a safety shower can hold in excess of one tonne of liquid three metres up in the air. When static on land, this tremendous weight is not a problem.
However, out on the high seas, a shower is put under extreme stresses and strains. This will twist a solid stainless steel water tank, as the constant shifting of its load exerts a huge strain on the tank. By using a flexible plastic tank and 316 external reinforced stainless steel framework, the forces involved can be absorbed, as well as withstanding the salty atmosphere. An additional special GRP internal baffle de-compartmentalises the load, thus reducing momentum.
Janet Dickinson is operations manager for safety shower specialists Showers & Eyebaths Services.
MORE FROM THIS COMPANY
OTHER ARTICLES IN THIS SECTION