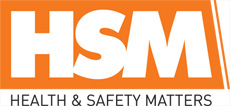
![]() |
Mark Sennett
Managing Editor |
![]() |
Kelly Rose
Editor |
Home> | Managing Health & Safety | >Decontamination Showers | >Brewery role for safety showers |
Brewery role for safety showers
16 May 2019
Safety showers may not be the first things that spring to mind when we think about beer and the brewing process, yet Hughes explains that they are a necessity in breweries due to the strong chemicals required to clean and disinfect equipment.

The value of the global beer industry is predicted to reach a staggering £526,000 million by 2025. In Europe alone the brewing industry is estimated to employ more than 100,000 people, producing over 40 billion litres of beer every year.
Getting beer from grain to glass is not a straightforward process. Even after brewing is complete, harsh chemical cleaners need to be used to ensure the tanks and pipework are sanitised and safe. Due to the potential for a splash or spill of these hazardous cleaners, on-site safety showers are a necessity.
The modern brewing method involves a number of different steps:
Organic deposits such as oils, fats, proteins and starches are left behind following the mashing, boiling and fermenting processes and inorganic scale such as beer stone (often caused by a chemical reaction between caustic cleaners, hard water minerals and proteins) can build up inside fermentation tanks and pipework. The tanks and kegs also become a breeding ground for bacteria and mould to thrive. A strict cleaning regime is necessary to combat any negative effects caused by these deposits and bacteria.
Due to the robust nature of these soils and microbials, strong chemical cleaners are required to clean and disinfect industrial brewing equipment. The hazardous chemicals present in the cleaning solutions have the potential to cause serious injury if they come into contact with the skin or eyes and would require immediate flushing to avoid further injury. Nearby safety showers and eye/face wash equipment must be available in the event of an accidental spillage.
Hazardous chemicals
The types of chemicals used in brewery cleaning belong to three general groups:
- High alkaline detergents for removal of proteinaceous, organic soil (i.e. oils, fats, proteins, starches, and carbohydrates encountered in brewing)
- High acidic cleaners for removal of inorganic soil and scale (e.g. water stains and beer stone)
- Disinfectants to remove microorganisms
Sodium Hydroxide (also known as Caustic Soda) and Potassium Hydroxide are often used to clean beer kegs along with the sludge left at the bottom of the brew kettle after boiling.
These caustic substances cause severe skin burns and long-term damage to eyes if not flushed immediately after contact.
Nitric acid & phosphoric acid, used for descaling in high concentrations can also cause eye damage along with acute acid burns in the event of a spill or splash.
Most breweries also rely on ammonia refrigeration to keep beer and other supplies cold. Ammonia is a particularly dangerous chemical which is corrosive to skin causing acute freeze burns. In the event of an accidental spill it requires a specific decontamination process.
Suitable Safety Showers
- Anhydrous ammonia used in refrigeration, requires safety showers to deliver a large amount of water for at least 15 minutes, at a temperature between 25 and 30°C. Hughes STD-TC-100KS/11K Temperature Controlled Safety Shower maintains the water within this range and can also be used to supply heated water to other emergency safety showers in the local vicinity.
- Hughes range of Indoor Emergency Safety Showers are suitable for a brewery environment. The indoor range includes ceiling, wall and over-door mounted models, designed for environments where space is at a premium. The combination units comprise a plumbed-in safety shower and an eye/face wash for full decontamination. (Model shown - EXP-18GS/45G)
General considerations for safety showers
- To ensure accidental spills are flushed from the skin and eyes quickly to minimise injury, emergency safety showers must be located within 10 seconds of a hazard. However, if a chemical is particularly hazardous, the safety shower and/or eye/face wash equipment should be placed immediately adjacent to the hazard.
- Water delivered by emergency safety showers should be tepid, between 16-38 C (60-100 F). At temperatures above 38 C (100 F) there is the added danger of scalding and increased absorption of harmful chemicals into the skin. Prolonged exposure to water below 16 C (60 F) increases the risk of thermal shock or hypothermia and prevents the casualty using the shower to decontaminate effectively for the full 15 minutes.
- Emergency safety equipment must be visually inspected and activated weekly along with an annual service to guarantee reliable and effective operation and conformance with European and International standards.
- Personnel who may be exposed to hazardous materials should be instructed on the safe and proper use of the emergency safety equipment and be advised of its location.
Both the EN 15154 and the internationally recognised American National Standard, ANSI/ISEA Z358.1-2014 provide uniform minimum requirements for the performance, use, installation, testing, maintenance and training of emergency safety shower and eyewash equipment.
- Showered with accolades
- Nick Clegg visits Hughes
- Contamination in the workplace
- Can your safety showers survive the cold?
- Emergency safety showers for hire
- Enhancing safety at Outokumpu
- Shower activation video
- Hughes expands
- Facing hazards in the fast-paced food industry
- Ladder platform for emergency tank showers