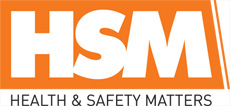
![]() |
Mark Sennett
Managing Editor |
![]() |
Kelly Rose
Editor |
Home> | Health & Wellbeing | >General Health & Wellbeing | >Raising the alarm on noise exposure |
Home> | Managing Health & Safety | >Noise Monitoring | >Raising the alarm on noise exposure |
Raising the alarm on noise exposure
04 July 2022
Tim Turney shares how employers can effectively protect their workers from excessive noise exposure.
OVER 170,000 people in the UK suffer from noise-induced hearing loss (NIHL), tinnitus or other acoustic trauma conditions as a direct result of excessive exposure at work.
Prolonged exposure to excessive noise levels can cause life-changing damage because the harm to the sensory cells and other structures within the ears is irreversible.1
If suitable measures are not set out to prevent NIHL, employers run the risk of reduced productivity, rising costs due to sick days and increased costs for training and recruitment on top of catastrophic penalties and compensation claims.
NIHL damage is, however, as preventable as it is permanent. Workers can wear hearing protection such as earplugs and earmuffs, but the greatest way to reduce hearing loss is by identifying and avoiding excessive noise in the first place
Regulations set out by the HSE
The Control of Noise at Work Regulations (2005) covers all industry sectors in Great Britain and aims to ensure workers are safeguarded from excessive noise.
There are legal limits on noise exposure in the workplace through exposure action and limit values:
-
The lower exposure action values are—
-
a daily or weekly personal noise exposure of 80 dB (A-weighted); and
-
a peak sound pressure of 135 dB (C-weighted).
-
-
The upper exposure action values are—
-
a daily or weekly personal noise exposure of 85 dB (A-weighted); and
-
a peak sound pressure of 137 dB (C-weighted).
-
-
The exposure limit values are—
-
a daily or weekly personal noise exposure of 87 dB (A-weighted); and
-
a peak sound pressure of 140 dB (C-weighted).
-
The 2005 Noise Regulations require employers to reduce noise exposure to as low as is reasonably practicable.
Providing hearing protection should only be a first-aid measure and noise exposure should be reduced as low as possible through control measures, such as engineering methods or reducing exposure time.
Implementing safety measures
If a risk assessment establishes that noise levels pose a risk to workers, personal hearing protection should be supplied immediately while other more permanent solutions are implemented. However, personal hearing protection should only be considered the primary solution when all other options have been exhausted as control of noise at the source is the ultimate priority. Other measures can reduce exposure by reducing the time a worker is exposed to loud noise, such as physically separating staff from the noisiest areas or rotating shifts to spread individual exposure.
It is often not possible to reduce noise such that earing protection is not necessary, and workers have a responsibility to wear hearing protection equipment that has been provided to them. The duration that hearing protection is worn is essential. The performance of hearing protectors is often less than the protection stated on the packaging because, without realising the risk, workers may remove them throughout their shift. If hearing protection is removed for even a small fraction of time, the overall protection the equipment offers is severely reduced.2
Selecting personal hearing protection
When selecting hearing protection equipment, employers should consider the relationship between hearing protection and other personal protective equipment (PPE). For example, an employee wearing prescription or safety glasses will not obtain an adequate fit from a standard earmuff, so plugs or semi-inserts may be more suitable. In working environments where hard hats are worn regularly, a hard hat with built-in hearing defenders should be considered.
Employers must also understand the process of reducing sound, known as attenuation. If a protector with too little attenuation is used, then employees will not receive enough protection. However, too much noise reduction can create feelings of isolation, and an employee may need to remove their PPE to communicate. In addition, over-attenuation can cut out safety warnings such as fire alarms or sirens from reversing vehicles, resulting in further risks to workers. As a rule of thumb, businesses can avoid over-protecting workers by ensuring the level of exposure is not reduced to a level below 75dB(A).
Using noise monitoring to gain insight
Noise monitoring equipment can be an essential tool for understanding sound level exposures. Measuring unwanted sounds and noises encompasses a wide range of deciBels. The goal is to measure an individual’s exposure to noise over an eight-hour period, so if the noise level is consistent throughout the day, then a relatively short measurement can be performed. If noise levels vary, however, a more comprehensive approach may be taken such as using multiple noise dosimeters on many people throughout the day, depending on the levels of noise variation as well as the number of employees in the workspace.
Noise monitoring provides accurate insights into the noise levels of a working environment, allowing businesses to identify problem areas and ensure compliance with HSE regulations. With the right equipment, and suitably trained health and safety managers, using a sound level meter or dosimeter can create an effective noise monitoring routine on-site. There are several products in the market that offer these capabilities, so choosing the correct tool for the job, while essential, can also prove difficult. Ideally, those responsible for the task should understand noise in terms of measuring terminology, frequency and amplitude (deciBels).
Trained professionals should also recognise that noise measurements should be repeated if there are changes to the workplace layout, installation of additional machinery or a change in the type of distribution of work undertaken. Of course, individuals may not be knowledgeable about all the aspects covered above and all the detail involved, so external consultation should be sought for areas where competency may be lacking.
Sound level meters
A sound level meter is a hand-held device, enabling measurements to be taken at the ear with the instrument pointing at the noise source. This process must be repeated for both ears for all duties employees perform, making it possible to calculate an accurate record of daily exposure.
When using a sound level meter, measurements must be started at the beginning of a task, representing workers’ actual exposure. If workers are likely to be exposed to high levels of impulsive noise, emitted from heavy pressing operations or sheet metal working, peak noises must be measured for accurate results and compared to peak action levels.
Noise dosimeters
If individual working patterns are irregular, if the worker is highly mobile, or if the work carried out means it is not practical or safe to conduct noise monitoring with a sound level meter, noise dosimeters can be used. Dosimeters are effective for personal noise measurements where it is difficult or unsafe to get close to employees with a sound-level meter because dosimeters are smaller and body-mounted. For example, a dosimeter would be ideal for forklift truck drivers exposed to many different noise levels and irregular working patterns.
Dosimeters can be worn by employees for their entire working shift. Data is logged instantly, and when downloaded onto another device, details the time history of the noise exposure, highlighting where high exposures occur throughout the day. Workers can also make a diary of times and jobs performed, allowing the employer to see the operations that require more effective noise controls. It is important that the data is presented in a format that is easy to understand for a layperson who may not be familiar with all acoustic terminology. Therefore, choosing a dosimeter with accessible software is essential to ensuring accurate insights are gained and, ultimately, taken on board.
Noise dosimeter measurements are subject to tampering, so spot-checking high levels with a sound level meter is beneficial to ensure accuracy. Therefore, when choosing between either monitoring solution, it should be noted that a combination of both solutions can provide the most valid measures.
Noise monitoring equipment protects the future workforce
NIHL is more common than diabetes or cancer.3 It’s vital that employers take responsibility for their workforce and protect their worker’s health. However, skill and knowledge of noise monitoring can take years to build, so the information detailed here can only offer an introductory approach to the effects of noise exposure and equipment to combat this. Training support and external consultancies are suitable for bridging gaps in an employer’s knowledge so that dangerous noise exposure is thoroughly mapped across a workplace.
References
Tim Turney is global marketing manager at Casella. For more information, visit www.casellasolutions.com/us/en.html
- Noise kit upgrade
- Casella 63x digital sound level meters for occupational and environmental noise measurements
- Exposure measuring for HAV or WBV
- Casella launches Intrinsically Safe dBadge2
- Expose the hidden danger
- Next generation of noise dosimeters
- CASELLA INTRINSICALLY SAFE TUFF PERSONAL AIR SAMPLING PUMP AND dBADGE SOUND LEVEL METER ARE A HIT DOWN UNDER WITH AUSTRALIAN DEPARTMENT OF DEFENCE
- Something in the air
- Software package for personal dosimeter
- Casella aids Spanish traffic police
- BSIF: Covid-19 Update
- Dust tight
- SAFEContractor for 5th year
- BSC welcomes proposals to slash legal costs in personal injury claims
- Get some insight
- Asbestos remains number one killer
- Chemical exposure course goes more than skin deep
- Getting workers involved in safety
- Dual drug testing
- On-site health screening