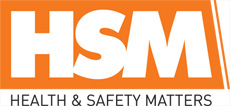
![]() |
Mark Sennett
Managing Editor |
![]() |
Kelly Rose
Editor |
Home> | Breathing Safely | >Breathing Air | >Air quality in the workplace |
Home> | Breathing Safely | >Gas Detection and Monitoring | >Air quality in the workplace |
Home> | Health & Wellbeing | >General Health & Wellbeing | >Air quality in the workplace |
Air quality in the workplace
25 June 2024
COINCIDING WITH Love Your Lungs Week 2024, Tim Turney explains the benefits of maintaining good air quality in the workplace.

Poor air quality affects everyone, some more than others. Those working in industrial settings such as manufacturing plants, construction sites, mines and agriculture sites are among the most likely to be exposed to harmful airborne hazards. The World Health Organization (WHO) estimates that 4.2 million deaths globally can be attributed to surrounding air pollution. Combined with work-related exposure to fumes, dusts, gases and vapours, the risk to workers’ lung health is amplified and precautions must be taken to protect wellbeing.1
12,000 occupational lung disease deaths each year are estimated to be linked to past exposure at work with many thousands more suffering from symptoms. The most common being chronic obstructive pulmonary disease (COPD), a group of lung illnesses that cause breathing difficulties and chest infections. Poor air quality can also increase the likelihood of heart attacks, cancers and can make existing conditions worse.2
Legally, employers have a duty of care to ensure employees aren’t exposed to dangerous levels of substances in the air and reduce exposure to as low as practicable. Workplace Exposure Limits (WELs), occupational exposure restrictions agreed by the Health & Safety Executive (HSE), are defined under the Control of Substances Hazardous to Health Regulations 2002 (COSHH) to dictate the levels at which hazardous substances must be controlled. These concentrations are averaged over a set period of time as workers are often subject to varying concentrations depending on their environments throughout the working day.
The only way to ensure the concentrations of dangerous substances falls well below the WELs is through monitoring. It is not acceptable to get exposure to just below the WEL. Besides controlling the hazards in the workplace to as low as is reasonably practicable, as is dictated by the hierarchy of control, regular air sampling is the most reliable method of ensuring air quality is at acceptable levels to protect staff and comply to regulations, and ensure control measures in place are effective.
Air sampling pumps
Exposure limits are based on personal samples, so the only way to guarantee the safety of employees is to use personal air sampling pumps and implement control measures from the results.
Most personal air sampling pumps are Intrinsically Safe (IS) rated but it is important to check the pump’s rating to ensure it is suitable for each individual case. Guidance can be found in both the user manual as well as a variety of online sources. The pumps must also adhere to the latest international standard for air sampling pumps. Compliance to ISO 13137 ensures accurate flow performance amongst other criteria, ensuring accurate sampling and removing the need for repeated measurement.
As pumps are worn on the body, design characteristics like robustness and comfortability are essential to ensure the monitoring process does not impede working activities. The pump should almost seamlessly form a part of the employee’s uniform otherwise there may be a risk that the pump is removed, causing inaccurate results that will lead to incomplete safety measures being taken.
Before use, pumps must be calibrated with the whole ‘sample train’ that is the head and filter in place to ensure the system is leak free. They should also be checked at the end of the day to make sure flow has not deviated by more than 5%. If it has, there may be a leak or another malfunction which must be remedied before additional measurements are taken.
Sampling procedures are designed to ensure accurate and consistent collection of hazard concentration samples that correctly reflect the substance levels for an individuals exposure, or specified sampling locations and times. Some areas of a facility will have higher concentrations of airborne hazards at different times of the day which must be considered when monitoring, such as an active grinding tool.
Conclusion
Those in industrials settings are often subject to elevated levels of impure and potentially dangerous hazardous air. Employers in this space must control this to avoid financial, legal and reputational implications and most importantly, to protect workers health. Find out the hazards present, sample the quality of the air and implement effective control measures to preserve employees’ health and avoid the penalties for noncompliance.
References
https://www.who.int/teams/environment-climate-change-and-health/air-quality-energy-and-health/health-impacts/exposure-air-pollution
https://www.hse.gov.uk/statistics/causdis/
Tim Turney is global marketing manager at Casella. For more information, visit www.casellasolutions.com
* Love Your Lungs Week takes place between the 21-27 June 2024
- Enhanced sound level meter
- High-level service status
- Improving occupational health
- Dust updates from across the pond: What could this mean?
- Casella's dBadge2 Noise Dosimeter achieves WELMEC approval
- Get connected with App
- Complete solution
- TSI Releases OmniWear Noise, a lightweight, easy-to-use dosimeter.
- Casella will be at Event City in Manchester from the 10th-11th October for Health and Safety North
- Something in the air?
- BSIF: Covid-19 Update
- Dust tight
- SAFEContractor for 5th year
- BSC welcomes proposals to slash legal costs in personal injury claims
- Get some insight
- Asbestos remains number one killer
- Chemical exposure course goes more than skin deep
- If the face fits
- Contains dust over large areas
- Don't get a face full