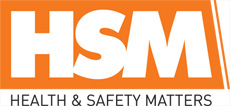
![]() |
Mark Sennett
Managing Editor |
![]() |
Kelly Rose
Editor |
Home> | Premises | >Risk Management | >Serving up security |
Home> | Premises | >Safe Access | >Serving up security |
Home> | Premises | >Spill Prevention/Solutions | >Serving up security |
Serving up security
06 May 2015
Jeremy Cassady, managing director at Securikey, looks at some of the safety and security hazards that are faced by those working in the food and drink processing industry, and explores the physical security solutions available that are specially designed to minimise risk in these challenging environments.
Food and drink manufacturing covers over 30 different sectors, with the largest being the bakery sector, and takes place in factories ranging from small units with few workers to large factories which may be part of multi-site organisations employing thousands.
In the UK, health and safety legislation in the industry is drawn up and enforced by the HSE and local authorities (the local council) under the Health and Safety at Work Act 1974. The European Standardisation Committee (CEN) has also produced a number of European CEN 'C' standards which set out safety requirements for certain types of food machine. Not surprisingly, these are a leading cause of workplace injuries as many have moving parts, sharp edges, hot surfaces and other hazards with the potential to crush, burn, cut, shear, stab or otherwise strike or wound workers if used unsafely or, for instance, if views are obstructed. In order to minimise the electrical and mechanical hazards faced by industrial workers operating this diverse array of machinery, security procedures such as Lockout-Tagout are enforced. This involves shutting off the power to industrial machines or equipment during maintenance or repair, which helps prevent the accidental activation of equipment and resulting injury.
Companies have developed a variety of safety methods and procedures to minimise the risks of physical danger, in areas such as in tight factory spaces and wherever machines and people are in the same place. Safety and security conditions in food manufacturing factories have improved as a result of these effective products and procedures, which is reflected by the declining numbers of injuries reported to the HSE over the years.
Clear vision
Where space is limited and visibility is key, leading suppliers of safety and security products offer an effective and efficient solution in the form of mirrors which comply with UK food standard regulations. British and European legislation demands that all equipment used in the manufacture of food and drinks be easy to clean, corrosion-resistant and have imperceptible seams to avoid the risk of trapped organic substances becoming a breeding ground for bacteria. That is why stainless steel, which meets all these requirements, is the material of choice for leading manufacturers in the food industry.
Stainless steel safety mirrors, such as the Securikey Hygiene F Series, are available in various sizes to meet different needs and have a number of uses in food processing factories. Apart from the obvious uses of allowing a clear view around blind spots and in tight corridors and areas, stainless steel food processing mirrors are also used for viewing vats, hoppers and mixers to prevent backlogs or jams on production lines, thereby helping to prevent injuries.
Access control
An important security factor in a food processing factory is ensuring that only authorised personnel have access to all areas through appropriate access control.
Factories can also be targets for theft and unlawful entry so having a solid access control system in place is of great importance. Mechanical digital door locks, such as the Keylex range from Securikey, offers the perfect solution for a wide range of applications - eradicating the need for keys, cards or tokens that could be lost, stolen or damaged. This range comes in four different variations, from mini to heavy duty, depending on the security level needed, and allows for up to 16,000 different password variations to ensure security is never compromised. If there is a need for physical keys there are a number of sophisticated key safes and vaults that meet the highest British safety standards, proven by recognised product testing houses, to offer advanced key monitoring, management and security.
Keeping safe
Another important factor to consider is safes for securing valuables within a busy factory environment. In food processing factories there might be a need to keep numerous items secure from prying hands, from personal belongings and sensitive documents to potentially harmful chemicals. No matter what the security level need, there are safes on the market that offer different levels of security. Those responsible for the security within a food processing factory are advised to source safes from a reputable supplier, that are certified with EN 1143-1 security standards and are Association of Insurance Surveyors (AIS) approved. In addition to preventing theft, fireproof safes will also keep sensitive materials unharmed in the event of fire and prevent the loss of important documents and items.
Taking the necessary measures to ensure the safety of employees and the security of the workplace in such a tightly regulated industry is the number one priority for those responsible for health and safety. Fortunately, there have been many advances towards improving workplace security in food processing and manufacturing factories. With a wide range of products like safety mirrors designed specifically for the food industry and a wealth of expertise available from leading suppliers, end users can ensure regulations and risk assessment requirements are all met successfully and without complication.