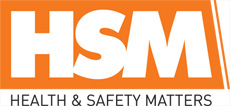
![]() |
Mark Sennett
Managing Editor |
![]() |
Kelly Rose
Editor |
Focus on lens material
28 April 2018
In prescription safety eyewear it is crucial to match the correct lens material to the job in hand, understanding the requirements of the wearer and the hazards they may be exposed to says uvex.

For everyday glasses and users of visual display units (VDUs), CR39 (Columbia Resin 39) lenses are commonly used, replacing the glass lenses of old, which were thicker, heavier and shattered easily.
CR39 advantages
First introduced in 1947, CR39 is made of plastic polymer, which is economical to produce.
It is lightweight
It offers good chemical resistance in laboratories or workshops where caustic, corrosive, or irritant chemicals are used.
It gives higher impact resistance than traditional glass lenses, but less than polycarbonate.
CR39 disadvantages
CR39 does not have the impact strength of new, polycarbonate lenses, and is therefore not suitable for hazardous workplace environments where impact may pose a risk as it may break and shatter.
CR39 only conforms to EN166S, the same standard as toughened glass.
A UV coating must be added to CR39 lenses to protect the eyes from the sun’s harmful rays that can cause cataracts, macular degeneration or other eye diseases.
CR39 is thicker than more recently developed impact-resistant lens materials, making spectacles heavier and running the risk of distortion of the appearance of the wearer’s eyes, which may be cosmetically less appealing.
Polycarbonate advantages
Originally developed for the aerospace industry owing to its exceptional impact resistance, polycarbonate is now the ‘go to’ material for safety eyewear.
Made by injection moulding, polycarbonate lenses are up to 10 times more impact-resistant than plastic or glass lenses and give high optical quality.
They naturally provide 100% protection from the sun's harmful UV rays without needing a special coating to be added.
Lenses made of polycarbonate conform to EN166F, the same impact strength as industrial safety glasses and the next level up from EN166S.
They have exceptional strength and resilience and will survive the impact of a steel ball travelling at 160 km/hr (45 metres per second) without cracking, chipping or breaking.
Polycarbonate lenses are 25% thinner and about 20% lighter than CR39 lenses, making them more comfortable and aesthetically pleasing for the wearer.
Owing to its versatility and robustness, polycarbonate can be used for rimmed, rimless and half-rimmed spectacles, allowing manufacturers to offer a large choice of lens and frame options to wearers.
Polycarbonate disadvantages
Polycarbonate lenses are slightly more expensive than CR39 lenses, but their advantages significantly outweigh this small drawback and they are nonetheless extremely affordable.
Because polycarbonate is a relatively soft material, which is what makes it flexible and able to absorb energy without fracturing, a hard, scratch-resistant coating must be applied to the lens to help protect it and prevent surface scratching.
Check your glasses
Many prescription wearers will be unaware that high-street opticians will automatically supply eyewear with CR39 lenses unless polycarbonate is specifically requested, potentially leaving them at risk from impact injuries at work.
Check your glasses by looking at the lens markings, which will be either at the top or on the side of the lens. Look for the letters ‘S’ or ‘F’. If you can see an ‘S’, your glasses are likely to be CR39.
In conclusion, it is important to ask the optician which lens material will be supplied in your safety eyewear and to ensure it is the right one for you.
To find out more, contact your local uvex representative at:
www.uvex-safety.co.uk/en/uvex-safety-group/how-to-contact-us/regional-contacts/