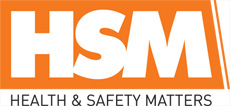
![]() |
Mark Sennett
Managing Editor |
![]() |
Kelly Rose
Editor |
Home> | Plant & Machinery | >Hand Arm Vibration | >Ten reasons to manage vibration |
ARTICLE
Ten reasons to manage vibration
23 January 2013
Vibration is one of the most common,but harmful, workplace hazards. It can lead to permanent disabilities and damage to nerves, muscles and joints and other long-term consequences for health and well-being, unless it is a

Vibration is one of the most common,but harmful,
workplace hazards. It can lead to permanent disabilities
and damage to nerves, muscles and joints and other
long-term consequences for health and well-being,
unless it is avoided by continual monitoring,
measurement and control explains Svantek
According to the HSE, two million people in the UK are at risk from the harmful effects of exposure to vibration in the workplace, yet despite this, vibration is often underestimated and ignored.
There are two main types of vibration - hand-arm vibration (HAV) and wholebody vibration (WBV). Hand Arm Vibration is transmitted from work processes into workers' hands and arms during the use of hand-held vibrating power tools such as saws, angle-grinders, hammer drills, torque wrenches and breakers. HAV can also arise during the use of hand-guided equipment, such as planers and sanders, or by holding materials being processed by machines.
Industries where exposure to HAV is particularly high include construction, motor, foundries, fabrication and heavy engineering.
Whole-body vibration is transmitted through the seat of work vehicles or the feet of employees who drive or operate heavy mobile machines such as tractors, lorries and fork-lift trucks, and is common in industries such as forestry, quarrying and construction. WBV comes from machines or vehicles producing elevated vibration levels that shake the entire body.
Legislation The Control of Vibration at Work Regulations 2005, which implement the European Physical Agents (Vibration) Directive 2002/44/EC in the UK, seek to protect workers from the harmful effects of vibration by placing a duty of care on employers to minimise the risks to their health, reducing exposure to vibration to as low a level as possible.
The Regulations specify daily exposure levels at which employers are required to take action to control risks, known as Exposure Action Values (EAVs). They also set out Exposure Limit Values (ELVs), at which point the employer must prevent further daily exposure.
All new machinery built in or imported into Europe has to comply with the Machinery Directive 2006/42/EC, which contains more precise requirements concerning vibration than its previous version. Suppliers must provide information on the vibration emission value of their equipment.
Consequences of not managing vibration If an organisation ignores the risk of vibration and does not take steps to monitor and measure it, it lays itself open to many serious adverse effects. These include potential industrial or compensation claims, prosecutions, heavy fines and costs. For example, in April this year, Land Rover had to pay out £80,000 for not keeping vibration levels in check at its Solihull plant. Companies may also experience adverse publicity, a loss of productivity and profit.
Failing to manage HAV exposure puts employees are at risk of a large range of unfavourable consequences, including ill health, pain, distress, limiting of tasks and the inability to do fine work or everyday tasks properly. They may also suffer a reduced ability to work outdoors in cold or damp conditions, lowered grip strength affecting their ability to work safely, potential musculoskeletal, neurological, and vascular effects on the hand or arm such as carpal tunnel syndrome, sleep disturbance and a risk of permanent damage with sustained usage of vibrating tools.
How to manage and monitor vibration Vibration is the movement of particles that occurs at a frequency below the range of human hearing. It has distinct characteristics in different directions, making it essential to measure on each of its three axes independently and preferably simultaneously.
Before vibration can be monitored and measured to keep employee exposure within the limits, an initial risk assessment of the vibratory equipment should be done. The employer should consult their employees and check the machinery they are using or driving. Once these tasks have been completed, controls, information, training, and perhaps new work methods, can be put in place.
Vibration meters can then be used to measure the amount of vibration from power tools and over the whole body.
These meters alert the user to stop using the tools or equipment when they are approaching maximum exposure levels.
Factors to take into account when measuring vibration include the length of time the vibrating tool is used (trigger time), the identification of operations that make up an exposure pattern, the measurement of vibration for each operation and the typical exposure time for each operation.
According to the HSE, two million people in the UK are at risk from the harmful effects of exposure to vibration in the workplace, yet despite this, vibration is often underestimated and ignored.
There are two main types of vibration - hand-arm vibration (HAV) and wholebody vibration (WBV). Hand Arm Vibration is transmitted from work processes into workers' hands and arms during the use of hand-held vibrating power tools such as saws, angle-grinders, hammer drills, torque wrenches and breakers. HAV can also arise during the use of hand-guided equipment, such as planers and sanders, or by holding materials being processed by machines.
Industries where exposure to HAV is particularly high include construction, motor, foundries, fabrication and heavy engineering.
Whole-body vibration is transmitted through the seat of work vehicles or the feet of employees who drive or operate heavy mobile machines such as tractors, lorries and fork-lift trucks, and is common in industries such as forestry, quarrying and construction. WBV comes from machines or vehicles producing elevated vibration levels that shake the entire body.
Legislation The Control of Vibration at Work Regulations 2005, which implement the European Physical Agents (Vibration) Directive 2002/44/EC in the UK, seek to protect workers from the harmful effects of vibration by placing a duty of care on employers to minimise the risks to their health, reducing exposure to vibration to as low a level as possible.
The Regulations specify daily exposure levels at which employers are required to take action to control risks, known as Exposure Action Values (EAVs). They also set out Exposure Limit Values (ELVs), at which point the employer must prevent further daily exposure.
All new machinery built in or imported into Europe has to comply with the Machinery Directive 2006/42/EC, which contains more precise requirements concerning vibration than its previous version. Suppliers must provide information on the vibration emission value of their equipment.
Consequences of not managing vibration If an organisation ignores the risk of vibration and does not take steps to monitor and measure it, it lays itself open to many serious adverse effects. These include potential industrial or compensation claims, prosecutions, heavy fines and costs. For example, in April this year, Land Rover had to pay out £80,000 for not keeping vibration levels in check at its Solihull plant. Companies may also experience adverse publicity, a loss of productivity and profit.
Failing to manage HAV exposure puts employees are at risk of a large range of unfavourable consequences, including ill health, pain, distress, limiting of tasks and the inability to do fine work or everyday tasks properly. They may also suffer a reduced ability to work outdoors in cold or damp conditions, lowered grip strength affecting their ability to work safely, potential musculoskeletal, neurological, and vascular effects on the hand or arm such as carpal tunnel syndrome, sleep disturbance and a risk of permanent damage with sustained usage of vibrating tools.
How to manage and monitor vibration Vibration is the movement of particles that occurs at a frequency below the range of human hearing. It has distinct characteristics in different directions, making it essential to measure on each of its three axes independently and preferably simultaneously.
Before vibration can be monitored and measured to keep employee exposure within the limits, an initial risk assessment of the vibratory equipment should be done. The employer should consult their employees and check the machinery they are using or driving. Once these tasks have been completed, controls, information, training, and perhaps new work methods, can be put in place.
Vibration meters can then be used to measure the amount of vibration from power tools and over the whole body.
These meters alert the user to stop using the tools or equipment when they are approaching maximum exposure levels.
Factors to take into account when measuring vibration include the length of time the vibrating tool is used (trigger time), the identification of operations that make up an exposure pattern, the measurement of vibration for each operation and the typical exposure time for each operation.
MORE FROM THIS COMPANY
- Get monitoring
- Noise dosimeter
- Whole body vibration measurement
- Lightweight & robust
- Intrinsically safe noise dosimeter
- Svantek reports increased demand for SV103 personal hand-arm vibration exposure meter
- Noise and vibration monitoring
- Heat monitoring system
- Noise and vibration monitors
- Noise and vibration monitoring
OTHER ARTICLES IN THIS SECTION