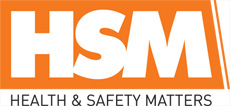
![]() |
Mark Sennett
Managing Editor |
![]() |
Kelly Rose
Editor |
Home> | Plant & Machinery | >Hand Arm Vibration | >To HAV and to hold |
ARTICLE
To HAV and to hold
23 January 2013
The HSE estimates that up to two million workers are exposed to levels of vibration that could result in ill health. With several solutions for managing Hand Arm Vibration exposure available, Jim O'Hagan considers the optio

The HSE estimates that up to two million workers are exposed to levels of vibration that could result in
ill health. With several solutions for managing Hand Arm Vibration exposure available, Jim O'Hagan
considers the options and makes the case for deploying an automated solution
The main regulations that govern the management of HAVs are the European Union's Physical Agents Directive and the UK's Control of Vibration at Work Regulations. Central to these Regulations are the hand arm vibration exposure action-value (EAV) and exposure limit-value (ELV). The EAV may be described as a level of daily vibration exposure, that if exceeded, requires the employer to introduce control measures such that exposure is reduced to a level as low as reasonably practicable. The ELV may be described as a level of daily exposure that by law must not be exceeded.
Key to these values is what is termed 'A(8)'. This is a unit that might conveniently be described as representing a 'dosage' of vibration exposure, over an assumed 'typical' eight hour shift.
The EAV is equal to an exposure of average vibration magnitude of 2.5 m/s2 for a total period of 8 hours in a working shift.
The ELV is equal to an exposure of average vibration magnitude of 5m/s2 for a total period of eight hours.
There are several solutions available to help manage Hand Arm Vibration Exposure ranging from paper based solutions to fully automated management solution, these include:
Tool labelling Some organisations fit green, orange or red plastic or water resistant labels to their power tools that are pre-printed with vibration data and the maximum amount of time that an operative can use that particular tool before reaching their EAV or ELV level. The onus is then on the operator to ensure they do not exceed the recommended time.
Manual records Other organisation rely on their operative to report on a daily basis what tools they used and for how long in a manual "school jotter" type document. Ideally this data should be captured at the end of the shift prior to the operator leaving site.
Individual Dosimeter There are commercially available dosimeters that provide a traffic lights system to alert the operator when EAV and ELV levels are met. The operator programmes the dosimeter and fits it in turn to each of the tools used throughout the shift. Prior to using the dosimeter on each tool the operator has to: 1. Determine the vibration level of that tool by referring to its manual 2. Programme that into the dosimeter 3. Fit the dosimeter to that tool
Fully automated solution Although the above methods are widely used, they have limitations. For example labels can get damaged and become unreadable, or are even lost and not replaced, and manual methods are often inaccurate unless they are strictly monitored. However there are several technologies available today that can be deployed to create an automated solution that can achieve the following: Easy to use Minimise operator interaction Accurately measure trigger time Provide a real time display of actual exposure points in line with HSE recommendation Give visual traffic lights to immediately alert the operator Require no programming by the operator Collate and gather operator exposure data automatically Generate useful management information
The HAVmeter from Reactec for example, is a solution that delivers the above benefits. The HAVmeter can calculate and record cumulative real-time vibration data across all vibratory hand tools in use by an operator throughout the working day. Each power tool is fitted with an RFID tool tag that contains basic asset data and average vibration level. A personal swipe card enables the operator to swipe out a HAVmeter from a base station. The HAVmeter magnetically attaches to the tool tag and "connects" with that tool data. The operator moves the HAVmeter from tool to tool throughout the working day and returns the HAVmeter to the base station at the end of the working day, at which time the data for the tool usage is transferred automatically to the Basestation. The data on the Basestation is stored on a memory card for upload into a comprehensive suite of reporting software that provides detailed and accurate analysis of operator exposure records. The data collected enables management to completely automate reporting, identify staffing issues on particular jobs and help protect the company from false claims. Companies that see the system as a management tool rather than just a health & safety device can see a return on investment well with 12 months.
Jim O'Hagan is the managing director of the HAVmeter division, Reactec. Visit Reactec, Stand 240 at Health & Safety '10 North
The main regulations that govern the management of HAVs are the European Union's Physical Agents Directive and the UK's Control of Vibration at Work Regulations. Central to these Regulations are the hand arm vibration exposure action-value (EAV) and exposure limit-value (ELV). The EAV may be described as a level of daily vibration exposure, that if exceeded, requires the employer to introduce control measures such that exposure is reduced to a level as low as reasonably practicable. The ELV may be described as a level of daily exposure that by law must not be exceeded.
Key to these values is what is termed 'A(8)'. This is a unit that might conveniently be described as representing a 'dosage' of vibration exposure, over an assumed 'typical' eight hour shift.
The EAV is equal to an exposure of average vibration magnitude of 2.5 m/s2 for a total period of 8 hours in a working shift.
The ELV is equal to an exposure of average vibration magnitude of 5m/s2 for a total period of eight hours.
There are several solutions available to help manage Hand Arm Vibration Exposure ranging from paper based solutions to fully automated management solution, these include:
Tool labelling Some organisations fit green, orange or red plastic or water resistant labels to their power tools that are pre-printed with vibration data and the maximum amount of time that an operative can use that particular tool before reaching their EAV or ELV level. The onus is then on the operator to ensure they do not exceed the recommended time.
Manual records Other organisation rely on their operative to report on a daily basis what tools they used and for how long in a manual "school jotter" type document. Ideally this data should be captured at the end of the shift prior to the operator leaving site.
Individual Dosimeter There are commercially available dosimeters that provide a traffic lights system to alert the operator when EAV and ELV levels are met. The operator programmes the dosimeter and fits it in turn to each of the tools used throughout the shift. Prior to using the dosimeter on each tool the operator has to: 1. Determine the vibration level of that tool by referring to its manual 2. Programme that into the dosimeter 3. Fit the dosimeter to that tool
Fully automated solution Although the above methods are widely used, they have limitations. For example labels can get damaged and become unreadable, or are even lost and not replaced, and manual methods are often inaccurate unless they are strictly monitored. However there are several technologies available today that can be deployed to create an automated solution that can achieve the following: Easy to use Minimise operator interaction Accurately measure trigger time Provide a real time display of actual exposure points in line with HSE recommendation Give visual traffic lights to immediately alert the operator Require no programming by the operator Collate and gather operator exposure data automatically Generate useful management information
The HAVmeter from Reactec for example, is a solution that delivers the above benefits. The HAVmeter can calculate and record cumulative real-time vibration data across all vibratory hand tools in use by an operator throughout the working day. Each power tool is fitted with an RFID tool tag that contains basic asset data and average vibration level. A personal swipe card enables the operator to swipe out a HAVmeter from a base station. The HAVmeter magnetically attaches to the tool tag and "connects" with that tool data. The operator moves the HAVmeter from tool to tool throughout the working day and returns the HAVmeter to the base station at the end of the working day, at which time the data for the tool usage is transferred automatically to the Basestation. The data on the Basestation is stored on a memory card for upload into a comprehensive suite of reporting software that provides detailed and accurate analysis of operator exposure records. The data collected enables management to completely automate reporting, identify staffing issues on particular jobs and help protect the company from false claims. Companies that see the system as a management tool rather than just a health & safety device can see a return on investment well with 12 months.
Jim O'Hagan is the managing director of the HAVmeter division, Reactec. Visit Reactec, Stand 240 at Health & Safety '10 North
MORE FROM THIS COMPANY
- HAV technology put to the test
- Five mistakes of HAVS risk management
- What is proximity detection technology and why is it important?
- New report shines light on HAVS threat
- HAVmeter survives coldest winter since 1914
- The connected safety ecosystem - integration is key
- HAVexposure management
- Health and safety at work statistics
- A modern approach to managing dust exposure at work
- Share safety messages with onsite teams
OTHER ARTICLES IN THIS SECTION