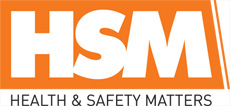
![]() |
Mark Sennett
Managing Editor |
![]() |
Kelly Rose
Editor |
Home> | Managing Health & Safety | >Decontamination Showers | >A hand with safety |
A hand with safety
15 October 2020
AT THE beginning of the COVID-19 pandemic, supplies of disinfectants, PPE and alcohol gel were too low to meet the demands of both front-line workers and the general public.

Micro-breweries and distilleries stepped in to meet the increased need. These manufacturers quickly altered their processes to make way for the production of thousands upon thousands of bottles of hand sanitiser. Already skilled in the production of alcohol products, it was a natural move for these companies. Many generously donated supplies straight to the front line in healthcare and production is ongoing with demand levels remaining high.
Dealing with the differing hazardous chemicals required to manufacture alcohol hand gel requires additional safety procedures. Isopropyl alcohol and ethanol used to produce these hand sanitisers are not only highly flammable but can also cause moderate skin irritation or serious eye injury and must be washed off immediately if there is a spill.
To help countries ensure safety and produce alcohol-based handrubs, WHO identified formulations for their local preparation. The hydrogen peroxide used in the WHO Handrub Formulations is a chemical that is incompatible with many substances (e.g., organic material, caustics, some acids), is corrosive to the skin, and may cause eye irritation in its diluted form (concentrations of <8%). At higher concentrations (>30%), hydrogen peroxide solutions can react explosively with many substances, and are even more corrosive and irritating to the eyes, skin, and respiratory tract.
As an employer, it is your responsibility to ensure you know of potential risks in your workplace, including chemical risks. Where procedures are changing, even temporarily, and new chemicals are being handled it is essential that risk assessments are updated or created, and any required safety measures are put in place.
Where a substance can cause harm or severe irritation to skin or eyes, it’s imperative that a specifically designed safety shower or eye/face wash is provided to effectively wash off the contaminant in the event of an accident or to clean off PPE.
Safety shower considerations
Standard hygiene facilities have their place as part of workplace health and safety, especially in the case of keeping hands clean in the current climate. However, in the case of hazardous substances like highly concentrated alcohol, they cannot replace the effectiveness of emergency safety showers and eye/face wash equipment when it comes to swift decontamination.
So that hazardous materials are quickly washed from the skin and eyes to minimise potential injury, emergency safety showers must be located within 20 metres or 10 seconds of a hazard. If a chemical is particularly dangerous, it is recommended that safety showers and/or eye/face wash equipment should be placed immediately adjacent to the area where the material is being handled.
Additionally, the water delivered by an emergency safety shower must be tepid. In the EN 15154 standards, this is defined as being between 15-37 C (59-99 F). At temperatures above 37 C (99 F) the hot water could scald the casualty and increase absorption of harmful chemicals into the skin. If cold water, below 15 C (59 F), is used this adds a risk of thermal shock or hypothermia and may stop the casualty from using the shower to decontaminate effectively for the full recommended 15 minutes.
Hughes Safety Showers range of indoor emergency safety showers are ideal for a brewery or distillery environment. The indoor range includes ceiling, wall and over-door mounted models, designed for environments where space is at a premium. The combination units comprise of a plumbed in safety shower and an eye/face wash for full decontamination.
Emergency safety equipment showers must be inspected and activated weekly along with an annual service for reliable and effective operation and to conform with European and International standards.
Both the EN 15154 and the internationally recognised American National Standard, ANSI/ISEA Z358.1-2014 provide uniform minimum requirements for the performance, use, installation, testing, maintenance and training of emergency safety shower and eyewash equipment. View the EN and ANSI summaries here.
For advice on the most suitable solution for your application or to request a quote, contact us today.
- Are your safety showers ready for winter?
- Why is safety shower maintenance so important?
- Spare parts from Hughes
- Safety award winner
- Facing hazards in the food industry
- The importance of tepid water
- Protecting quarry workers
- Protect lab workers from chemical burns
- Spritz of safety to fragrance manufacturing
- Showered with accolades