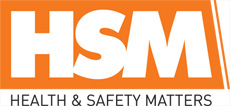
![]() |
Mark Sennett
Managing Editor |
![]() |
Kelly Rose
Editor |
Home> | Slips, Trips & Falls | >Slip Prevention | >No more slip ups |
No more slip ups
18 April 2016
Jim Hanna, Dickies international business development manager, has provided advice on preventing slips, trips and falls.
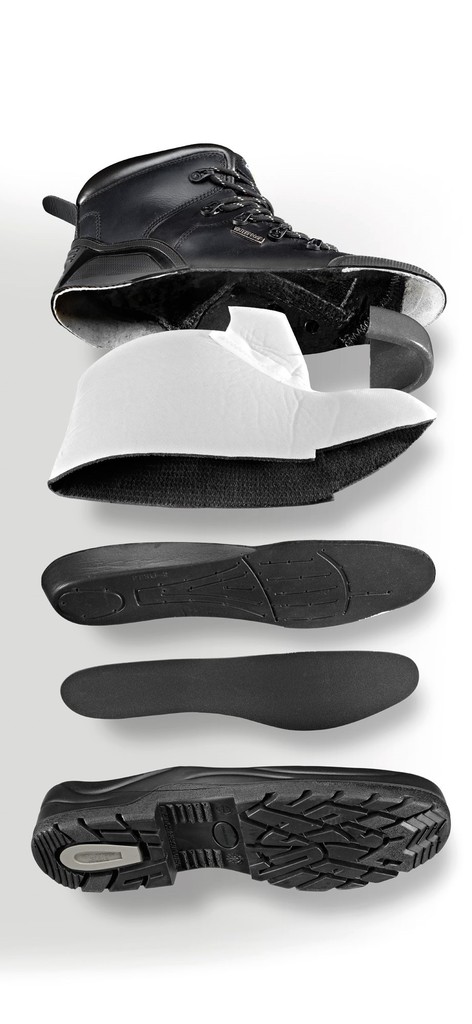
The HSE believe that slips and trips account for over 30% of work injuries and that they are the most common cause of injuries at work. They have attributed a cost of over £500m a year in lost production and other costs to UK industry.
General Health and Safety legislation places an obligation on the employer to ensure their employees are protected from slips trips and falls at work. The Workplace (Health, Safety and Welfare) Regulations 1992 cover all aspects of the workplace and require that floors and surfaces are suitable, maintained correctly in good condition and should be free from obstructions, ensuring that workers are able to walk around their place of work safely.
Housekeeping plays a major factor in preventing accidents both at home and at work. Tidying up not only makes the environment more pleasant to live and work in but it also makes it healthier and safer too. Routine cleaning, removing obstructions and debris on a regular basis all help to contribute to a safer workplace, prevention is better than cure as the old adage goes.
Ensuring things like cables and floor coverings are secured correctly, rendering them incapable of becoming a trip hazard, is everyone’s responsibility. Any contaminants that are spilt or leaking may look harmless enough at the time but even water can become a serious risk later on in freezing temperatures to the unsuspecting. Keeping to designated walkways and ensuring that the same walkways are respected and kept clear keeps everyone safe. Where appropriate they should also be kept well lit, replacing faulty light fittings and bulbs as part of the maintenance procedure.
Walkways should be suitably designed to be sufficiently allow for the type and volume of traffic they are likely to be used for. Surfaces should be kept clear, clean and dry where possible and the type of surfacing should reflect the intended use, both indoor and outdoor. Provision of adequate storage facilities and bins should remove any reason for these areas to become a risk. Any steps or stairs should be clearly highlighted, especially the step nosings with suitable illumination and visual markings. The risers between each step should also be consistent and secure with, of course, provision of a handrail which should be compulsory to hold whilst ascending and descending, one hand free for the purpose at all times.
An often overlooked factor is distraction. Walkways should be screened off or even fenced if there is a possibility that personnel could have their attention distracted or their eyes diverted to other surrounding activities.
Workers should be able to wear the footwear that is appropriate to their occupation, working environment, and feet. That means employers should ensure that the risk assessment they have to do by law includes risks to the feet as well as slipping risks, and if safety or special footwear is required they must supply it.
Safety shoes also need to be comfortable and correctly fitted. There is a misconception that safety shoes, especially protective toecaps, will be uncomfortable, but if the shoes are padded and fitted correctly you should not be able to feel the toecaps at all.
It is important to ensure that the safety shoe is appropriate for the task for which it is intended. Any protective equipment, including shoes provided by an employer, should meet European standards. There are various standards for footwear, including one for safety footwear, another for protective footwear, and a third for occupational footwear. Any footwear that is being supplied must be certified and stamped with the CE mark.
The most important element of any item of working apparel is its comfort and durability. This is especially important with regards to safety footwear, more so when considering that most tradesmen could spend up to nine hours a day working in their footwear. So any safety footwear not only has to be comfortable and provide support to the wearer’s foot but also be strong enough to withstand the rigours of the modern working environment.
Safety footwear standard EN345 has been superseded by EN ISO 20345 and the whole Dickies footwear range has been re-certified to the new standard EN ISO 20345:2011. A good safety footwear supplier will ensure their products are rigorously tested to not only meet, but exceed, the minimum safety standards required by law. Dickies not only ensures complete conformity to UK standards, but also those across the whole of Europe, investing in the development of not only the safety elements of footwear products, but also the comfort and longevity for each shoe or work boot produced.