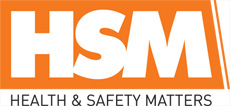
![]() |
Mark Sennett
Managing Editor |
![]() |
Kelly Rose
Editor |
Home> | Breathing Safely | >Gas Detection and Monitoring | >Measuring the microcscopic |
ARTICLE
Measuring the microcscopic
23 January 2013
Whenever organic solvents are used, it is inevitable that a quantity is emitted to air. These solvents or,
as they are commonly known,"Volatile Organic Compounds" (VOCs) pose a health risk to workers.
Thankfully there are
Whenever organic solvents are used, it is inevitable that a quantity is emitted to air. These solvents or, as they are commonly known,"Volatile Organic Compounds" (VOCs) pose a health risk to workers. Thankfully there are increasingly sophisticated methods of detecting VOCs available, explains Paul Walton.
Most industrial organisations are users of VOCs. They may be found in hospitals, universities and colleges as well as chemical and petroleum plants. Hazards arise from print solvents, solvents in adhesives, degreasing agents, in addition to fugitive emissions from hydrocarbons.
The result of over-exposure by an employee is rarely going to prove lifethreatening.
He or she will get home for dinner tonight. But routine exposure could mean they might not survive to enjoy retirement.
So what is a safe level? The Health and Safety Executive publication EH40 (www.hse.gov.uk/COSHH/table1.pdf) lists the occupational exposure limits for hazardous substances at work and publishes tables of figures to allow you to identify the long-term exposure limit (eight-hour TWA reference period) and short term exposure limit (15 minute reference period).
Spot checks Once you know what levels are unacceptable, you can measure and prove everything is okay. But how do you measure? The simplest and least expensive method is with a chemical stain tube.
Using a simple hand pump or electronic pump, a fixed sample volume sample of gas is drawn through the tube. The gas tube incorporates an accurate etched marking to illustrate the gas measurement. A colour change takes place, and the length of the stain translates into a measurement for the gas in question. This long-established method has proved popular for many years as it offers the benefit of low-cost, simple technology and many different tube types are available for different compounds and different ranges. With pricing for these spot checking gas tubes now falling considerably, this method will continue to be popular for many organisations.
The long-term tube But spot-checking does not give a complete picture. What if the worker's exposure level varies continuously? One spot check could show a very high or very low reading. Numerous spot reading would be necessary to arrive at reliable 15 minute and 8 hour average exposures.
An alternative to the spot checking colour stain tube is the long-term tube, using a battery-powered pump, or the use of passive colour-change badges.
More commonly for 15-minute or 8 hour sampling, a sorbent tube and battery operated pump can be used for many gases and vapours. The sorbent tube normally contains two layers of a sorbent material (charcoal for example). Air is pulled through the tube and the solvents to be measured are collected on the first layer. The back-up layer is simply serving as a back-up to identify break-through.
After sampling the sorbent tube requires laboratory analysis. The trapped chemicals are extracted. Details of different chemicals and the quantity of each is also identified using gas chromatography. This technique is long established and gives accurate measurement. However, the use of a pump, a sorbent tube, the time delay in sending the tube to the lab, and the cost of analysis means this method isn't always ideal. Although accurate measurements should be achieved the potential for errors are great if the work is carried out by unskilled staff.
Also, although the measurement is considering a full working period of perhaps eight hours, the result obtained is only the average of the time period. The exposure could have been as a result of a very high concentration for a short time and low or zero exposure for the rest of the day. You cannot tell the profile of exposure throughout the working day from an eight-hour sorbent tube sample, so you are unable to accurately identify if simply adjusting a workers activity will minimise exposures.
The personal VOC monitor Recently introduced to the industry, the personal VOC monitor is small, lightweight and will provide an immediate warning of high concentrations. The monitor incorporates a clip to connect the monitor to the lapel of the worker to allow them to wear it and forget it. But in the event of a high level of gas, it immediately sounds an audible alarm and a flashing light to attract attention. The worker can take corrective action, or simply retire to a safe area.
The personal VOC monitor will measure a broad range of VOC's and display the total on its digital display. The range of solvents measured includes toluene, MEK, Trichloroethylene, and most of the solvents use in the industry.
The VOC monitor is a Photoionisation Detector (PID). A PID uses an ultraviolet light to break down chemical to positive and negative ions that can easily be measured with a detector. This detector measures the charge of the ionised gas and converts the signal into current. The current is amplified and displayed on the meter as parts per million.
Correction Factors are an important tool in the use of PIDs. They permit calibration on one gas while directly reading the concentration of another.
This eliminates the need for multiple calibration gases. PID manufacturers determine Correction Factors by measuring a PID's response to a known concentration of target gas. Correction Factors tend to be instrument, and/or manufacturer specific, so it is best to use the Correction Factors given by the manufacturer of the PID monitor.
To make it easier to work with, the user can select the compound he is interested in from a menu of compounds built into the instrument. Having selected the compound, the Correction Factor is automatically applied.
While the monitor provides an immediate warning to the worker, it will also allow the manager to identify a profile of the workers exposure through its datalogging capability. With capacity for frequent logging over an eight-hour period, data is easily sent to your PC in report and graphical format.
The graphical format will allow managers to pinpoint high concentrations.Through consultation with the worker, it should be possible to identify why these peaks occurred. Action may then be taken to avoid these high exposure periods in future.
The worker could have turned off the ventilation for a short period. The data record would immediately highlight an increased level of exposure. Individual workers may clown around and deliberately expose themselves to high levels. A graphical record showing a severe, high spike would give rise to suspicion of unacceptable working practices.
By carrying out routine monitoring of workers and archiving their exposure details, you have documentary evidence that the workers exposure has not exceeded the requirements of EH40.
The user may program alarm levels.
With reference to EH40, alarms can be set for eight-hour TWA period, 15 minute short-term exposure period as well as an instantaneous high level.
Unlike adsorptive techniques, where the worker is exposed and you simply do not know until it is too late, the VOC monitor tells you immediately whenever there is a problem.
The audible alarm and flashing light leaves no doubt that action needs to be taken. Now. Like a criminologist's magnifying lens helps to identify fingerprints, the personal VOC monitor allows individuals to protect themselves through microscopic measurement of harmful solvents.
While 'four-gas' monitors with explosive-gas, Oxygen and toxic-specific sensors, make up the bulk of continuous gas monitoring in many industries today, they do not provide the protection you need against many toxic gases and solvents used in the some production facilities today. The modern personal VOC monitor delivers accurate real-time continuous measurement of these toxic solvents at levels previously only measured on large transportable instruments. But of course, many users will insist on the capability of a four-gas monitor, plus a VOC monitor. This capability is also now available in a six-gas monitor. The PHD6 will measure VOCs as well as O2, CO, H2S, Explosive gas including methane. Alternative toxic gas sensors for NO, NO2, SO2, Cl2 as well as infra-red sensors for methane and CO2.
Paul Walton is customer services & support director at Shawcity. See Shawcity on Stand 12 at Health & Safety '10 South.
Most industrial organisations are users of VOCs. They may be found in hospitals, universities and colleges as well as chemical and petroleum plants. Hazards arise from print solvents, solvents in adhesives, degreasing agents, in addition to fugitive emissions from hydrocarbons.
The result of over-exposure by an employee is rarely going to prove lifethreatening.
He or she will get home for dinner tonight. But routine exposure could mean they might not survive to enjoy retirement.
So what is a safe level? The Health and Safety Executive publication EH40 (www.hse.gov.uk/COSHH/table1.pdf) lists the occupational exposure limits for hazardous substances at work and publishes tables of figures to allow you to identify the long-term exposure limit (eight-hour TWA reference period) and short term exposure limit (15 minute reference period).
Spot checks Once you know what levels are unacceptable, you can measure and prove everything is okay. But how do you measure? The simplest and least expensive method is with a chemical stain tube.
Using a simple hand pump or electronic pump, a fixed sample volume sample of gas is drawn through the tube. The gas tube incorporates an accurate etched marking to illustrate the gas measurement. A colour change takes place, and the length of the stain translates into a measurement for the gas in question. This long-established method has proved popular for many years as it offers the benefit of low-cost, simple technology and many different tube types are available for different compounds and different ranges. With pricing for these spot checking gas tubes now falling considerably, this method will continue to be popular for many organisations.
The long-term tube But spot-checking does not give a complete picture. What if the worker's exposure level varies continuously? One spot check could show a very high or very low reading. Numerous spot reading would be necessary to arrive at reliable 15 minute and 8 hour average exposures.
An alternative to the spot checking colour stain tube is the long-term tube, using a battery-powered pump, or the use of passive colour-change badges.
More commonly for 15-minute or 8 hour sampling, a sorbent tube and battery operated pump can be used for many gases and vapours. The sorbent tube normally contains two layers of a sorbent material (charcoal for example). Air is pulled through the tube and the solvents to be measured are collected on the first layer. The back-up layer is simply serving as a back-up to identify break-through.
After sampling the sorbent tube requires laboratory analysis. The trapped chemicals are extracted. Details of different chemicals and the quantity of each is also identified using gas chromatography. This technique is long established and gives accurate measurement. However, the use of a pump, a sorbent tube, the time delay in sending the tube to the lab, and the cost of analysis means this method isn't always ideal. Although accurate measurements should be achieved the potential for errors are great if the work is carried out by unskilled staff.
Also, although the measurement is considering a full working period of perhaps eight hours, the result obtained is only the average of the time period. The exposure could have been as a result of a very high concentration for a short time and low or zero exposure for the rest of the day. You cannot tell the profile of exposure throughout the working day from an eight-hour sorbent tube sample, so you are unable to accurately identify if simply adjusting a workers activity will minimise exposures.
The personal VOC monitor Recently introduced to the industry, the personal VOC monitor is small, lightweight and will provide an immediate warning of high concentrations. The monitor incorporates a clip to connect the monitor to the lapel of the worker to allow them to wear it and forget it. But in the event of a high level of gas, it immediately sounds an audible alarm and a flashing light to attract attention. The worker can take corrective action, or simply retire to a safe area.
The personal VOC monitor will measure a broad range of VOC's and display the total on its digital display. The range of solvents measured includes toluene, MEK, Trichloroethylene, and most of the solvents use in the industry.
The VOC monitor is a Photoionisation Detector (PID). A PID uses an ultraviolet light to break down chemical to positive and negative ions that can easily be measured with a detector. This detector measures the charge of the ionised gas and converts the signal into current. The current is amplified and displayed on the meter as parts per million.
Correction Factors are an important tool in the use of PIDs. They permit calibration on one gas while directly reading the concentration of another.
This eliminates the need for multiple calibration gases. PID manufacturers determine Correction Factors by measuring a PID's response to a known concentration of target gas. Correction Factors tend to be instrument, and/or manufacturer specific, so it is best to use the Correction Factors given by the manufacturer of the PID monitor.
To make it easier to work with, the user can select the compound he is interested in from a menu of compounds built into the instrument. Having selected the compound, the Correction Factor is automatically applied.
While the monitor provides an immediate warning to the worker, it will also allow the manager to identify a profile of the workers exposure through its datalogging capability. With capacity for frequent logging over an eight-hour period, data is easily sent to your PC in report and graphical format.
The graphical format will allow managers to pinpoint high concentrations.Through consultation with the worker, it should be possible to identify why these peaks occurred. Action may then be taken to avoid these high exposure periods in future.
The worker could have turned off the ventilation for a short period. The data record would immediately highlight an increased level of exposure. Individual workers may clown around and deliberately expose themselves to high levels. A graphical record showing a severe, high spike would give rise to suspicion of unacceptable working practices.
By carrying out routine monitoring of workers and archiving their exposure details, you have documentary evidence that the workers exposure has not exceeded the requirements of EH40.
The user may program alarm levels.
With reference to EH40, alarms can be set for eight-hour TWA period, 15 minute short-term exposure period as well as an instantaneous high level.
Unlike adsorptive techniques, where the worker is exposed and you simply do not know until it is too late, the VOC monitor tells you immediately whenever there is a problem.
The audible alarm and flashing light leaves no doubt that action needs to be taken. Now. Like a criminologist's magnifying lens helps to identify fingerprints, the personal VOC monitor allows individuals to protect themselves through microscopic measurement of harmful solvents.
While 'four-gas' monitors with explosive-gas, Oxygen and toxic-specific sensors, make up the bulk of continuous gas monitoring in many industries today, they do not provide the protection you need against many toxic gases and solvents used in the some production facilities today. The modern personal VOC monitor delivers accurate real-time continuous measurement of these toxic solvents at levels previously only measured on large transportable instruments. But of course, many users will insist on the capability of a four-gas monitor, plus a VOC monitor. This capability is also now available in a six-gas monitor. The PHD6 will measure VOCs as well as O2, CO, H2S, Explosive gas including methane. Alternative toxic gas sensors for NO, NO2, SO2, Cl2 as well as infra-red sensors for methane and CO2.
Paul Walton is customer services & support director at Shawcity. See Shawcity on Stand 12 at Health & Safety '10 South.
MORE FROM THIS COMPANY
- SV 200A monitoring station offers noise directivity detection
- Fixed gas detection expansion
- Gas sampling solutions
- No excuses, bump it
- Danger is brewing
- Benzene detection
- Gas detection with 2-year runtime
- US Navy approves QuantiFit2
- TVOC 2 fixed PID detector
- Smartphone compatible gas detection from Shawcity
OTHER ARTICLES IN THIS SECTION