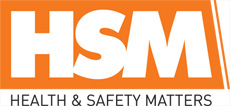
![]() |
Mark Sennett
Managing Editor |
![]() |
Kelly Rose
Editor |
Home> | Breathing Safely | >Gas Detection and Monitoring | >Raising the bar |
Raising the bar
09 September 2024
For both traditional and renewable energy, new technology keeps workers safer than ever before. Julian Jarvis looks at how connected safety raises the bar for gas detection.

FROM TRADITIONAL oil and gas extraction to renewable energy production, there are multiple threats to worker safety. According to the International Association of Oil & Gas Producers (IOGP)1, fatalities were up by 70% year-over-year in 2022, and the total recorded injury rate increased by 17%.
However it is produced, the creation of energy to power our homes, workplaces and wider infrastructure comes with risk to workers at every stage, from upstream exploration and extraction to midstream transportation and storage and downstream refinement. In this article we will consider both traditional and more modern ways of generating energy – and how gas detection is a critical tool for keeping workers safe during the operation.
The evolution of gas detection
Gas detection has evolved over time from the primitive ‘canary in the coal mine’ through the Davy lamp to today’s sophisticated connected gas detection technologies, which feed data to the cloud in real-time during use and are fast becoming the standard as workplaces transform digitally. Today’s connected safety devices can link employees to monitoring services and control rooms for live awareness, enable real-time information sharing, collect vital location data, support informed decision-making, and facilitate faster emergency response.
Advances in automation like data visualisation, compliance reporting and analytics also mean less time is spent gathering information and more time can be spent acting on it to improve worksite safety.
With devices offering direct-to-cloud connectivity, you can monitor multiple facilities or multiple workers—whether they are on the other side of town or the other side of the world—from any internet-connected device through an intuitive software portal.
Traditional energy activities
Oil and gas have long been important industries globally, engaged in the extraction of natural resources which are then used as fuels, or in terms of oil, processed in many different ways to become chemicals, pharmaceuticals, asphalt and more. Operators have learned the dangers associated with these activities – from fires and explosions to releases of toxic or combustible gases. Below are some of the key gas risks associated with oil and gas production, and how connected devices can mitigate them.
Many oil and gas operations involve the handling of combustible gases, such as hydrogen sulphide (H2S), methane (CH4), and propane (C3H4). These gases are highly flammable, and in the case of H2S, can be deadly if inhaled at high concentrations.
Furthermore, various conditions and processes can cause oxygen deficiencies such as oxidation from rusting, consumption of oxygen by fire or the displacement of oxygen by other gases. Highly explosive atmospheres can also occur in oxygen-enriched environments during refining processes or if caused by, for example, leaks.
Confined space risks
Confined Space Entries (CSEs) present a particular challenge and a variety of risks that can result in serious injury or death. They involve a worker entering a space such as a storage tank, mud pit, reserve pit or an excavated area around a well. According to the U.S. Department of Labor, from 2011 to 2018, 1,030 workers in the U.S. died from occupational injuries involving a confined space.
There are two main hazards associated with CSE. Firstly - atmospheric hazards - confined spaces can contain toxic or flammable gases such as methane, H2S, or CO, some of which can be deadly if inhaled. These gases can accumulate due to poor ventilation, leaks from equipment, or the breakdown of chemical compounds. Connected gas detector devices can be set to a pre-entry mode to measure gas levels before entering a confined space and then switched to diffusion mode to protect the worker while they complete the necessary work.
In addition to atmospheric hazards, the cramped and dark nature of these spaces makes them difficult to navigate which can lead to slips, trips and falls, i.e. physical hazards. Should an entry worker suffer an injury, it can be difficult to summon help, but connected gas detectors with fall and no-motion detection can automatically notify monitoring personnel when a worker experiences a fall. Connected devices also enable two-way communication to rapidly convey details of an incident.
Whether from a dangerous atmosphere or the physical hazards within a CSE, with connected safety devices, workers can feel confident knowing their safety is being monitored should an event occur. And, data analysis of exposure to harmful gases through a software portal can indicate gas leaks, ensuring areas of concern are addressed before they cause a serious or fatal incident.
Shutdown and turnaround risks
During a shutdown or turnaround at an oil or gas facility, there are additional hazards that HSE personnel and workers must be aware of to make sure safety is always a top priority. This includes significant added risks such as:
- Oxygen displacement and flammable or toxic gases released during the process of shutting down and restarting equipment for maintenance or repairs.
- Additional confined space entries under a short timeline.
- Contractors new to the site who are unfamiliar with the facility and its specific safety procedures. An IOGP study1 showed that 75% of lost work incidents were related to contractors in 2022.
- Fatigue from working longer hours and to compressed timelines can also put workers at greater risk.
Renewable energy activities
As the world embraces the need to decarbonise to cut damaging greenhouse gas emissions, renewable energy is becoming a more prevalent fuel source, but, just like the production of energy from oil and gas, creating it is associated with hazards to health and safety.
One of the largest areas of risk surrounds hydrogen which has a growing reputation as a clean fuel that could be used in applications from fuel for vehicles, to replacing current feedstocks in industries such as steel making, chemical manufacturing and oil refining. Hydrogen can also be stored and fed into the renewable energy system when required to balance supply.
However, hydrogen is both extremely flammable and, in its natural gas form, is the smallest molecule on earth, prone to leaking out of containment. It is also odourless and very light. Even if an odorant is added, by the time a worker smells the odorant, the hydrogen concentrations might have already exceeded its lower flammability limit. It therefore needs careful handling and hydrogen workers need protection.
Hydrogen risks for workers
At each stage of its journey from production to use, the nature of hydrogen as a flammable gas means it poses risk. Many industries that use gas detection are already protecting workers against gases produced as part of their operations.
As energy providers in particular move towards the production of cleaner fuels, they will need to broaden the spectrum of the gases they detect to include hydrogen. Based on voluntary reports to the U.S. government’s H2Tools website2, 40% of hydrogen incidents included property damage severe enough to close facilities and 5.2% of the voluntarily reported incidents included one or more fatalities.
It’s clear that as the industry develops, precautions around leaks must be taken to prevent accidents and death. Gas detection devices that include hydrogen sensors along with real-time connectivity will allow companies to stay on top of the risks to their workers. Built-in analytics will allow companies to spot and track trends that might indicate leaks, so they can be addressed before they become a hazard to worker safety.
In terms of new infrastructure that is already in development across the world, there are also several high-risk scenarios where gas detection devices that include hydrogen sensors are crucial.
Storage facilities
Large-scale storage of hydrogen, whether as a compressed gas or cryogenic liquid, presents hazards due to its flammability and the potential for leaks. Storage tanks must be designed to withstand high pressures and extreme temperatures, and facilities must have measures in place to rapidly disperse any leaking hydrogen to prevent accumulation and potential ignition.
Transportation
Hydrogen is transported in high-pressure pipelines and cryogenic tankers. The integrity of these transport systems is critical to prevent leaks and ruptures that could lead to fires or explosions. Safety measures include rigorous inspection protocols and maintenance schedules to ensure that pipelines and tankers remain safe.
Inspection and maintenance
As gas pipelines require inspection and maintenance, this can involve lone workers being out on the road covering large distances. As hydrogen is odourless, tasteless and colourless, a personal gas detector can warn the lone worker of a hydrogen leak before they get too close.
Refuelling stations
As the demand for cleaner fuel increases, we will see more hydrogen refuelling stations, bringing with them the risks of poor management. These stations will need interconnected safety systems and gas detectors to detect and mitigate leaks, and proper emergency protocols to handle potential fires or explosions. Hydrogen burns with a near invisible flame so it’s vital to detect leaks before they lead to ignition.
Bioenergy risks
Other renewable energy sources include Bioenergy which encompasses a range of technologies that convert organic matter, such as agricultural residues, forestry waste, and dedicated energy crops, into various forms of energy, including electricity, heat, and biofuels. Advanced bioenergy technologies, like second-generation biofuels and biogas, offer promising pathways for sustainable energy production.
However, the production of biogas results in the release of several toxic or flammable gases including Hydrogen sulphide (H2S). This toxic gas can be released from biogas facilities (and geothermal power plants) that use organic matter as fuel. Exposure can cause respiratory issues, dizziness, and even death at high concentrations.
Sulphur dioxide (SO2) is another toxic gas that can arise during geothermal and biodiesel production processes, where Ammonia (NH3) similarly represents a risk to bioenergy workers. Also toxic, it can cause respiratory issues and eye irritation.
Methane (CH4) is produced during anaerobic digestion in biogas facilities and from the decomposition of biomass. It is a combustible gas that is colourless and odourless, and high levels of methane can reduce the amount of oxygen breathed from the air. This can result in mood changes, slurred speech, vision problems, memory loss, nausea, vomiting, facial flushing and headache. In severe cases, there may be changes in breathing and heart rate, balance problems, numbness, and unconsciousness.
Conclusion
As we continue our journey towards decarbonisation in order to limit the greenhouse gas emissions that are causing global warming and subsequently climate change, new risks will emerge at all stages of the production and delivery of cleaner energy. And while exposure to gas is not a new threat for the energy industry, the types of gases we need to monitor for will expand in line with the growth of different energy generation activities. But, with the wider adoption of connected solutions with more options for sensors, including hydrogen, operators can be confident they are protecting workers from existing – and emerging – risk.
References
1 www.iogp.org/bookstore/product/safety-performance-indicators-2022-data/
2 h2tools.org/sites/default/files/Hydrogen_Incident_Examples.pdf
Julian Jarvis is zone manager at Blackline Safety. For more information, visit www.blacklinesafety.com
- Blackline Safety hires principal software architect
- Single-gas detector with enhanced features
- Safety solutions at Anticipate London
- Connected worker innovations
- Blackline Safety wins two product awards
- Next gen monitoring system
- Lone Worker portfolio
- Push-to-talk capability
- Cloud-connected area monitor on show at A+A
- More than just gas detection