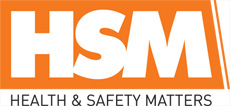
![]() |
Mark Sennett
Managing Editor |
![]() |
Kelly Rose
Editor |
Home> | Industry Update | >Company News | >Reaching new heights |
Home> | Health & Wellbeing | >General Health & Wellbeing | >Reaching new heights |
Reaching new heights
05 June 2024
Drug and alcohol testing is becoming an increasingly common practice is the workplace. Mark Burrup looks at how a UK airport has implemented a drug and alcohol testing policy.

WORKPLACE DRUG and alcohol testing is progressively becoming an area of increasing focus for many businesses, particularly in light of the rising prevalence of mental ill-health and its impact on employee safety and wellbeing.
The areas of concern relate not only to illegal drug and excessive alcohol consumption, but also to prescribed drugs, which can affect people’s responsiveness, concentration and decision-making capabilities. And as a result, this not only affects the safety of the individual but potentially the safety of colleagues and members of the public.
While employers have a legal duty to protect their employees’ health, safety and wellbeing, including providing protection from alcohol and drug misuse, there is also a growing recognition by employees of the dangers posed. Independent research carried out for last year’s Drager Safety at Work report showed that the increased focus on this aspect of health and safety is well-supported, with nearly three quarters (74%) of those questioned in favour of all employees in the organisation being tested for drugs and alcohol – increasing to 80% in the oil & gas / renewables sector.
Dräger has itself introduced an enhanced drug and alcohol testing policy across its UK business in the past two years, whereby everyone from managing director to apprentice is now eligible to be included in randomised testing, and again this has been welcomed by employees.
The company therefore knows first-hand how important it is to handle the subject sensitively, and with dignity and respect. If staff members should have any concerns, for example regarding the impact of prescribed medications, or because of challenges regarding substance addiction, they are encouraged to talk to their managers so they can be given help and support.
The following case study considers the role of drug and alcohol testing in a safety critical sector and looks at how testing can be used to manage situations where employees may pose a safety risk, whether this is operating heavy machinery or driving a colleague to a meeting.
An example in practice
A UK airport employing around 150 people, plus additional contractors, first brought in a drug and alcohol testing policy in 2017, however if there were an incident or a suspicion of someone working under the influence there was a delay due to the dependence on an external contractor to undertake a urine sample, impacting the effectiveness of the test and this service was also expensive.
The airport looked for a better solution, and opted for portable devices from safety and medical technology firm Dräger which work by using a saliva sample (for drug testing) or a breath sample (for alcohol testing). The saliva sample is quick, easy, non-invasive, and provides an observable sample collection, which is difficult to adulterate, and demonstrates recent drug use.
The airport’s new approach was brought into sharp focus when the airport’s health and safety manager was notified about a colleague who was suspected to be working whilst under the influence of alcohol. The colleague in question was in a risk-critical role, and it was imperative that the allegation be investigated properly in order to ensure safe operations, and also safeguard the wellbeing and safety of other colleagues.
The individual denied there was any issue, however, with reasonable grounds to suspect there was a problem, it was mutually agreed that a testing programme would be appropriate. At the same time, the HR department provided pastoral support.
Testing was undertaken every day for six weeks, this consisted of the individual blowing a breath sample every morning.
The airport health and safety manager comments: “It was extremely simple and hygienic to operate – the device made it clear when the person should start breathing and when they should stop, and a reading was displayed a few seconds later, together with a traffic-light system showing whether no alcohol, some alcohol, or a level of alcohol over the legal limit was detected.”
“Each test was clear, which was a great relief to all concerned, and we subsequently reverted to random testing.
“However, sadly, shortly after this, a randomly timed test revealed the same person to be over the prescribed limit for alcohol detection as defined by the company policy.”
The individual was suspended immediately to allow him to seek help via his doctor and support meetings. While doing so, the company continued to support him, ensuring he remained on full pay, and checking in with regular welfare calls.
After two weeks, he returned to work, but shortly afterwards decided to leave his job.
“It was a very sad case to be involved in, but when you consider the risks involved had we not been able to identify the issue and act, it’s unthinkable. It was a huge relief to be able to conclusively know what we were dealing with and be able to test so frequently and easily,” reflects the airport health and safety manager.
The experience prompted a complete review of the airport’s drug and alcohol policy. This resulted in the issue of a new, revised Drug and Alcohol Policy which now includes random tests across all departments on a quarterly basis, which can then be backed up with comprehensive laboratory based confirmatory testing if required.
Additionally, another significant change is the introduction of compulsory drug and alcohol testing for all new starters prior to joining the company.
“In the past, we only required a medical after someone had joined. Now we conduct a routine drug and alcohol test before any employment offer is made. Drug testing is carried out using an oral fluid drug testing device which uses a swab from the person’s mouth placed in the test device. No power source is needed, which means it is portable, hygienic and can be used anywhere – an important consideration on a site such as ours.” comments the airport health and safety manager.
The non-invasive, hygienic, oral fluid test, which takes 3 – 5 minutes to complete, and will conclusively prove if one or more of five substance classes are present, simultaneously: Cocaine (COC), Opiates (OPI), Amphetamines (AMP), Methamphetamine (MET, also known as ‘Designer Drugs’ e.g. ecstasy, MDMA), and Cannabis (THC). It is highly accurate and reliable.
And the new Drug and Alcohol Policy is already proving to be effective: “We had interviewed and planned to employ a new starter, but during our routine testing prior to offering him the position, the test showed the presence of a Class A drug.
“Faced with the indisputable proof, he immediately admitted he was a regular recreational drug user and had taken cocaine two days previously. It was clear that we could not – and would not – employ him.”
“We want to be fair and measured, and we’re keen to support colleagues that are struggling with personal issues or mental health problems. But the safe operation of the airport must be our priority It’s a risky enough operation without the worry of people being impaired in their work, and we have a duty of care to all those on site, both staff and the general public.
“It’s important to have a testing policy which also provides support and pastoral care, and we take our responsibilities as an employer very seriously in this regard. But at the same time, we need to be able to be confident in both a positive and negative test result, and the Dräger drug and alcohol testing technology empowers us to have this confidence and keep people safe as a result,” concludes the airport health and safety manager.
You can view the Drager Safety at Work report at www.draeger.com/en_uk/Safety/Drugs-Alcohol-Testing-At-Work
Mark Burrup is marketing manager impairment and detection Europe, at Draeger Safety UK. For more information, visit www.draeger.com
- Brian Hesler joins Draeger Safety
- New senior appointment at Dräger
- Reliable detection
- Draeger invests in chemicals sector
- Curb drink driving
- Breathing apparatus
- Helping UK businesses tackle drug drive hazards with real time technology
- Measures up to six gases
- Dräger launches hands-free thermal imaging camera to further improve firefighter safety
- Measures up to six gases
- BSIF: Covid-19 Update
- Who has the oldest Buck & Hickman catalogue?
- Dust tight
- SAFEContractor for 5th year
- BSC welcomes proposals to slash legal costs in personal injury claims
- Get some insight
- Asbestos remains number one killer
- Chemical exposure course goes more than skin deep
- Keeping shoppers safe
- Powered up