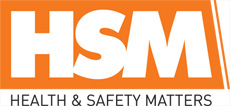
![]() |
Mark Sennett
Managing Editor |
![]() |
Kelly Rose
Editor |
What's trending with cut-resistant gloves?
18 December 2017
Hand injuries represent one quarter of all industrial accidents, a surprising statistic considering the availability of information and technology that makes prevention a reasonable target. Bastiaan de Koning, global business director at DSM Dyneema, offers an outlook in which change continues within the protective gloves business.
As glove materials and glove manufacturing technology evolves, so do the testing procedures. According to the International Safety Equipment Association (ISEA): “Before publication of the first edition of this standard for Hand Protection Selection Criteria in 2000, the practice of rating work gloves’ protection level as ‘good, fair or poor’ created inconsistencies among glove manufacturers in rating their gloves’ ability to provide protection.”
Since the introduction of the PPE Directive (89/686/EEC), all personal protective equipment placed on the market in the EU member states must carry a CE mark to verify compliance with the directive. While some differences exist between the two predominate global cut certification standards, the EN388 standard uses the Coup Tester and the ANSI 105 standard in the US uses the ASTM F1790-97 and F1790-05 test methods, both use a numeric rating system to classify cut resistance.
In general, with the ANSI/ISEA 105-2011 standard cut resistance is measured by the weight required to cut through a glove’s material and is categorised into five levels. Gloves comprised of latex or cotton would receive a cut level of one, while some high-performance gloves, including those made from enough Dyneema Diamond Technology fibre content in the appropriate denier thickness, will have a level five rating.
Evolving glove materials
The cut-resistant gloves industry today offers products with various degrees of cut protection using materials ranging from polyester and nylon to para-aramids, fibreglass, metal mesh, and even UHMWPE (Ultra High Molecular Weight Polyethylene) – invented by DSM Dyneema and sold as Dyneema brand fibre. UHMWPE is 15 times stronger than steel and can be incorporated into gloves that offer up to EN 388 level five cut protection – without mixing in other fibres such as fibreglass that sometimes causes irritation.
In the past few years there has been a push to develop finer gauge gloves that provide high cut resistance without compromising dexterity or comfort. Licensed glove manufacturers can use Dyneema Diamond Technology to, for example, create cut resistant gloves that offer twice the comfort at the same level of cut protection as previous material, or twice the cut protection at the same level of comfort as previous technology.
Shifts in workers' preferences
The rise of these new materials make the cut-resistant gloves of today the best the industry has ever seen. Yet challenges remain because the modern, highly customisable, customer-focused business model has extended to the world of cut-resistant gloves as well. More than ever before workers demand comfort and dexterity just as much as safety. Plus, workers want exceptional cut protection, but also protection from other workplace hazards. Combined safety features, such as cut resistance plus flame resistance or wicking properties with chemical protection, have become a priority.
Glove manufacturers have responded to these new demands by offering more options than ever before. More sizes to find the perfect fit, more colour choices, more feature customisation, and more industry-specific glove options. They’ve developed fabrics that can protect from multiple hazards, while providing the comfort, coolness, and dexterity workers want along with the durability and longevity that employers need.
“A cut-resistant glove provides protection only when employees wear them on the job,” said former OSHA compliance officer and Fortune 500 company EHS director David Lynn, now vice president of signature services with Life and Safety Consultants. “By offering choices that first meet the priority of providing the right protection based on job function, then the necessary comfort, look and feel characteristics workers request, glove manufacturers help employers maintain a workforce confident they can perform their jobs while staying protected. Bottom line – employees wear their gloves when they should.”
Workplace injury data
Workplace injury statistics clearly communicate a success story advancements in cut-resistant gloves have helped to bring about. According to the Bureau of Labor Statistics (BLS), nonfatal occupational illness and injury incidence rates in the private industry have decreased in recent years, from five cases per 100 full-time workers in 2003 to less than 3.5 in 2012. BLS suggests that “education and improvements in cut-resistant glove technology have been instrumental in lowering these injury rates.”
Despite this decline, employers understand better than ever before the direct and indirect costs of workplace injuries. As budgets have tightened in recent years, preventing these injuries has become critical to the bottom line. OSHA’s Office of Regulatory Analysis suggests that companies that implement effective safety and health programs can expect a return of $4 to $6 for every $1 invested.
The future promises further advancement
Employers are investing in the right kind of personal protective equipment (PPE) for their employees, as well as the providing the necessary education and training to ensure that employees are using PPE appropriately.
“The best programmes begin with a thorough evaluation of existing injury concerns, risks, threats and needs,” said Life and Safety Consultants’ Lynn. “That, along with involving the people who will use the gloves on the job in assessing the right factors, helps organisations make the right selection. But the need for continuous communication about the importance of safety procedures and wearing safety equipment must not be overlooked.”
The glove industry has evolved significantly in the last 60 years—with the most dramatic changes taking place just within the last 15. New fibres allow for cut-resistant gloves that are both lightweight and comfortable, while still providing higher levels of cut protection than ever before. This helps meet the demands of workers, who want comfort, dexterity, and industry-specific protection—sometimes from more than one hazard. Furthermore, testing methods have evolved to allow for a more standardised rating system for cut-resistant gloves.