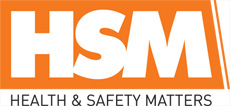
![]() |
Mark Sennett
Managing Editor |
![]() |
Kelly Rose
Editor |
Home> | PPE | >Ear Protection | >Protecting workers' hearing in four simple steps |
Home> | Health & Wellbeing | >General Health & Wellbeing | >Protecting workers' hearing in four simple steps |
Home> | Managing Health & Safety | >Noise Monitoring | >Protecting workers' hearing in four simple steps |
Protecting workers' hearing in four simple steps
01 March 2017
Simon Field, a technical specialist at science-based technology company 3M, offers some sound advice for protecting workers against hazardous noises.
Tinnitus Awareness Week ran from 6 to 12 February this year, once again making national headlines and helping to raise awareness of the condition. Tinnitus causes sufferers to hear ‘phantom’ noises, described as anything from ringing to banging or screeching. It is often linked to loud noise exposure and hearing loss.
Conditions linked to noise exposure are often entirely preventable, yet also irreversible. In persistent cases, they can significantly impact a person’s day-to-day life. According to the Health and Safety Executive, around 17,000 people in the UK suffer from deafness, tinnitus or other ear conditions as a result of exposure to loud noise at work.
As part of The Control of Noise at Work Regulations 2005, employers are required to protect employees from exposure to hazardous noise in the workplace. To help employers, 3M has designed a four-step approach to keeping workers safe from hearing damage, involving detection, protection, training and validation.
Detection
The first step is to carry out a workplace assessment to determine whether there is a problem with hazardous noise to begin with. As a rule of thumb, if employees need to raise their voices when speaking to one another, or if the noise is otherwise intrusive, it is likely that sound levels are too high. In any areas in which this is the case, accurate noise measurements should be taken, either in-house by a competent person, or by a hired consultant. These results can help determine which noise control methods to use, re-evaluate risk assessments and select appropriate hearing protection equipment (HPE).
Protection
Like any workplace hazard, employers should look to the hierarchy of control and implement ‘control at source’ measures wherever possible in order to reduce noise levels in the area. However, in some environments employees may need to wear HPE even after such measures have been taken. In these cases, it is vital that HPE provides adequate protection for the task at hand and is also suitable for the wearer, the task and their workplace environment. Here, adequate means the equipment must protect against harmful noise levels present in the given environment.
However, employers should also bear in mind the need for essential communication and awareness of audible alarms and warnings. Choosing hearing protection with the most noise attenuation is not necessarily the best solution. Employers should also consider whether or not HPE is compatible with any other personal protective equipment (PPE) being worn. For instance, large bulky temple arms on spectacles can decrease the effective protection offered by ear muffs.
Overall suitability is about the optimum level of protection combined with user preference, compatibility, hygiene considerations, product maintenance and many other factors.
Workers should be offered a range of HPE and should be involved in the selection process, whether through feedback sessions, questionnaires or similar means. When HPE is suitable, workers are far more likely to use it properly. If it is not, they are more likely to frequently remove or adjust it for comfort or to communicate with colleagues – and even temporary removal can increase the risk of harm.
Training
Training is as important as picking the right equipment in the first place. For training to be effective, it should cover several areas. First, the importance of HPE should be explained, together with when it should be worn. Employees must also understand the specific noise hazards present in their workplace, the control measures to be used, how to wear and adjust their equipment, and any maintenance and storage procedures required. This will help to make them more aware of their own hearing safety and that of their colleagues, as well as improving their ability to protect against hazards.
The level of protection provided by any given piece of HPE will differ between users, largely depending on their physical characteristics and how they wear the equipment. For example, people with wider ear canals may receive less protection than those with narrower ear canals. Those who have not been suitably trained on how to insert their ear plugs may also face greater exposure to hazardous noise levels. Fit testing can account for all these factors, providing quantitative data to show the level of protection achieved by each worker.
This four-step approach can be used as a checklist to reassure employees that they have covered everything in the HPE selection process and are making the right product decisions.
- BSIF: Covid-19 Update
- Dust tight
- SAFEContractor for 5th year
- BSC welcomes proposals to slash legal costs in personal injury claims
- Get some insight
- Asbestos remains number one killer
- Chemical exposure course goes more than skin deep
- Breaking free from a cycle of failure
- Getting workers involved in safety
- Dual drug testing