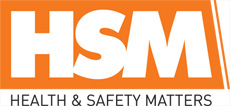
![]() |
Mark Sennett
Managing Editor |
![]() |
Kelly Rose
Editor |
Home> | PPE | >Ear Protection | >Breaking free from a cycle of failure |
ARTICLE
Breaking free from a cycle of failure
23 January 2013
When faced with a persistent problem in any Hearing Conservation Program safety managers often try to
use the same traditional measures to solve the problem.Here Paul Barker suggests a new approach
When faced with a per
When faced with a persistent problem in any Hearing Conservation Program safety managers often try to use the same traditional measures to solve the problem.Here Paul Barker suggests a new approach
When faced with a persistent problem in any Hearing Conservation Program, such as extreme noise exposures, safety managers often use the same cycle of tactics and interventions to solve the problem. Too much noise? Provide workers with earplugs of a higher attenuation rating. Use dual protection - earplugs and earmuffs. Install acoustical enclosures, baffles and dampeners; increase the frequency of machine maintenance; rotate workers in noisy areas on shorter shifts. Then re-measure the ambient noise with sound level meters and dosimeters.
If the estimated reduction is insufficient, the answer is clear: do the same again — perhaps ad infinitum. In such situations, the solution seems to become the problem and safety managers become frustrated as they face a seemingly endless cycle that yields minimal results and little real-world data.
At Dixie Industries, the forging and assembly company based in Tennessee in the USA, Ed Tougaw the production manager, was experiencing such problems. But, by applying new technology to create meaningful Hearing Conservation Program tactics he was able to break free from the cycle of failure.
Forging is one of the loudest of all manufacturing processes and at Dixie Industries, employee noise exposure levels can reach 108 to 112 dBA. As forging is also a precision process, Tougaw says "the operators must be able to see and manipulate the product as it is being formed and effective shielding is nearly impossible. We rely on the proper personal protective equipment (PPE) to protect them after the engineering is performed." Dixie Industries' Hearing Conservation Program requires all workers to wear hearing protection throughout the facility, and in the forge area where exposures average 110 dBA throughout the course of a workday they use dual protection.
Over a decade, the operation also underwent over 30 different projects to reduce overall noise. More than $1.8 million was spent on a variety of different noise reduction yet, a noise problem persisted and Dixie Industries was cited by the local equivalent of the HSE.
The Solution Tired of working through the same cycle of failure Tougaw sought out alternative methods to document and control noise exposure. He turned to a new technology, QuietDose from Howard Leight, which measures and collects an individual's daily noise exposure dose. Integrated into earplugs or earmuffs, QuietDose measures and records the worker's actual noise dose over their entire work shift. When it is worn as hearing protection, it measures sound pressure levels in the interior of the protector. During periods when it is not worn, QuietDose measures ambient noise levels. Overall, it accounts for the ear's actual noise exposure, and provides realtime monitoring throughout the workday.
QuietDose's Exposure Smart Protector dosimeter alerts the worker when noise dose approaches or exceeds safe limits, and the data available allows the safety manager to access daily noise exposure reports.
Using a QuietDose In-Ear Starter Kit six workers recorded their daily noise dose over several months. Concurrent, ambient noise measurements were also recorded with a sound level meter.
The Results The data from both in-ear and ambient dosimetry was collected and analysed, to some interesting results. Workers using in-ear dosimetry experienced noise exposures under the Personal Exposure Limit and in fact nearly all measurements were under 80 dBA. The workers exposed to the loudest noise achieved only 25% of their daily dose. The protection was working. For all the previous efforts to mitigate noise, only in-ear dosimetry was able to determine that with proper protection, training and motivation, workers can be adequately protected from extreme noise over an entire work shift — with the numbers and documentation to validate the findings.
"From our field studies, we weren't surprised to see that the workers were adequately protected, especially since they were wearing double protection, said Dr.
Kevin Michael, one of the inventors of the technology, "In fact, nearly all industrial exposures can be reduced to a safe level with a properly fitted single hearing protector. But, what this demonstrates is that conventional de-ratings can be grossly inaccurate." The data was presented to the local HSE and the citation was abated two months later but today, Dixie Industries continues to use QuietDose. "The success of our in-ear dosimetry program sent a message that everyone could and should make a contribution to the overall safety environment at Dixie," says Ed Tougaw.
He considers QuietDose a "foundational element" of Dixie Industries' overall safety program.
When faced with a persistent problem in any Hearing Conservation Program, such as extreme noise exposures, safety managers often use the same cycle of tactics and interventions to solve the problem. Too much noise? Provide workers with earplugs of a higher attenuation rating. Use dual protection - earplugs and earmuffs. Install acoustical enclosures, baffles and dampeners; increase the frequency of machine maintenance; rotate workers in noisy areas on shorter shifts. Then re-measure the ambient noise with sound level meters and dosimeters.
If the estimated reduction is insufficient, the answer is clear: do the same again — perhaps ad infinitum. In such situations, the solution seems to become the problem and safety managers become frustrated as they face a seemingly endless cycle that yields minimal results and little real-world data.
At Dixie Industries, the forging and assembly company based in Tennessee in the USA, Ed Tougaw the production manager, was experiencing such problems. But, by applying new technology to create meaningful Hearing Conservation Program tactics he was able to break free from the cycle of failure.
Forging is one of the loudest of all manufacturing processes and at Dixie Industries, employee noise exposure levels can reach 108 to 112 dBA. As forging is also a precision process, Tougaw says "the operators must be able to see and manipulate the product as it is being formed and effective shielding is nearly impossible. We rely on the proper personal protective equipment (PPE) to protect them after the engineering is performed." Dixie Industries' Hearing Conservation Program requires all workers to wear hearing protection throughout the facility, and in the forge area where exposures average 110 dBA throughout the course of a workday they use dual protection.
Over a decade, the operation also underwent over 30 different projects to reduce overall noise. More than $1.8 million was spent on a variety of different noise reduction yet, a noise problem persisted and Dixie Industries was cited by the local equivalent of the HSE.
The Solution Tired of working through the same cycle of failure Tougaw sought out alternative methods to document and control noise exposure. He turned to a new technology, QuietDose from Howard Leight, which measures and collects an individual's daily noise exposure dose. Integrated into earplugs or earmuffs, QuietDose measures and records the worker's actual noise dose over their entire work shift. When it is worn as hearing protection, it measures sound pressure levels in the interior of the protector. During periods when it is not worn, QuietDose measures ambient noise levels. Overall, it accounts for the ear's actual noise exposure, and provides realtime monitoring throughout the workday.
QuietDose's Exposure Smart Protector dosimeter alerts the worker when noise dose approaches or exceeds safe limits, and the data available allows the safety manager to access daily noise exposure reports.
Using a QuietDose In-Ear Starter Kit six workers recorded their daily noise dose over several months. Concurrent, ambient noise measurements were also recorded with a sound level meter.
The Results The data from both in-ear and ambient dosimetry was collected and analysed, to some interesting results. Workers using in-ear dosimetry experienced noise exposures under the Personal Exposure Limit and in fact nearly all measurements were under 80 dBA. The workers exposed to the loudest noise achieved only 25% of their daily dose. The protection was working. For all the previous efforts to mitigate noise, only in-ear dosimetry was able to determine that with proper protection, training and motivation, workers can be adequately protected from extreme noise over an entire work shift — with the numbers and documentation to validate the findings.
"From our field studies, we weren't surprised to see that the workers were adequately protected, especially since they were wearing double protection, said Dr.
Kevin Michael, one of the inventors of the technology, "In fact, nearly all industrial exposures can be reduced to a safe level with a properly fitted single hearing protector. But, what this demonstrates is that conventional de-ratings can be grossly inaccurate." The data was presented to the local HSE and the citation was abated two months later but today, Dixie Industries continues to use QuietDose. "The success of our in-ear dosimetry program sent a message that everyone could and should make a contribution to the overall safety environment at Dixie," says Ed Tougaw.
He considers QuietDose a "foundational element" of Dixie Industries' overall safety program.
MORE FROM THIS COMPANY
- No related articles listed
OTHER ARTICLES IN THIS SECTION