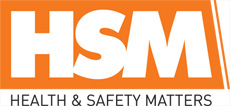
![]() |
Mark Sennett
Managing Editor |
![]() |
Kelly Rose
Editor |
Home> | Breathing Safely | >Respirators | >Improving workplace safety with RPE |
Improving workplace safety with RPE
02 June 2015
Alan McArthur, technical services specialist at diversified technology company 3M, discusses the important role respiratory protective equipment can play in protecting workers from harmful substances.
While at work people may wish to believe that what they can’t see can’t hurt them, this couldn’t be any further from the truth. Dangerous substances, including gases, vapours, dusts and fumes, are often invisible to the naked eye and can cause serious health problems to those who breathe them in.
Each year in the UK approximately 13,000 deaths occur due to occupational respiratory diseases. In addition, there are 10,000 estimated new cases of breathing or lung problems caused or made worse by work.
The most common diseases triggered by harmful exposures are respiratory cancers, chronic obstructive pulmonary disease, occupational asthma and pneumoconiosis. Worryingly, the majority of these conditions are so called long latency diseases – meaning they can go undetected for years. This is why it is imperative that the right measures are put in place to protect workers from exposure to harmful substances.
So, how do we try to prevent damage to respiratory health while at work?
First, and most importantly, companies must ensure a risk assessment has been carried out in the workplace. When a risk assessment identifies airborne hazards, prevention and control of exposure must be addressed. If a worker is likely to come into contact with a harmful substance, appropriate measures need to be put in place to help keep people healthy and safe.
The hierarchy of control must be followed but when the exposure to harmful substances cannot be fully controlled by other means, protection can come in the form of respiratory protective equipment (RPE).
HSE guidance for certain tasks calls for RPE to be used alongside other control measures, for example, respirators with an assigned protection factor of at least 20 when cutting silica containing building materials and compressed air fed RPE when spraying isocyanate containing paints.
Are there any problems with RPE?
There are lots of types of RPE available including masks, helmets, visors and hoods, and it is definitely not the case that one product can suit all situations. Once it has been decided RPE is required careful selection is needed to ensure the product is right for the task at hand. There are lots of contributing factors when deciding on the best solution because not all products are practical for all hazards, situations and people.
Questions that need to be asked when selecting RPE include:
- Is it suitable for the hazard?
- Does it provide enough protection?
- Is it suitable for the job?
- Is additional protection required too?
- Is it comfortable for the user?
- Does it fit and seal properly?
It is not unusual to hear people complain about RPE not being comfortable or not fitting properly. This is because a whole range of factors, including facial hair or a poor match with other personal protective equipment (PPE), can negatively impact on RPE. In some cases this may deter people from using the products. To ensure this doesn’t happen it is important to involve them in the selection process. By including the users, they can trial various options and find the best product for them.
Once RPE has been properly selected, training must be given on how to use the product and for non-disposable products additional training is needed for cleaning, storage, inspection and maintenance. Some products, such as reusable half mask respirators, will require filter change and the wearer must receive instructions on when and how to do so.
For particulate hazards this is relatively straightforward but more care is needed for gas and vapour hazards. With most filters there is no indication of when it needs replacing and employees are often directed to change their filters on a pre-defined schedule. However, mistakes can be made and wearers could be left exposed. Also, if users are too cautious, they could throw their filters away while they potentially still have useful life, resulting in a waste of money.
To tackle these problems, 3M has introduced End of Service Life Indicator (ELSI) Technology to offer a revolutionary way of managing the replacement of organic gas and vapour filters. The new technology incorporates a novel polymer that changes construction as organic vapours travel through the filter. Providing that the vapour concentration is above the Minimum Indication Level (MIL) published by 3M, this causes an easily visible indicator bar to develop as the filter becomes increasingly saturated. This easy-to-interpret, visual indictor empowers wearers and assists health and safety managers, helping to keep people safer at work.
- Disposable respirator offers durability
- Respiratory protection urged
- Welding talk
- Combo passes fit test
- Double protection at half the price
- 3M advanced three-panel design optimises comfort
- Flexible fit disposable respirator
- 3M Pioneers advanced disposable respiratory protection technology
- Respiratory & personal protection
- Latest respirators