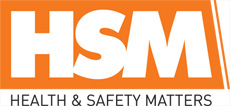
![]() |
Mark Sennett
Managing Editor |
![]() |
Kelly Rose
Editor |
Home> | Managing Health & Safety | >Standards | >An essential investment |
An essential investment
07 September 2015
Gordon Burns, technical fabrics applications engineer at W.L. Gore and Associates (UK) discusses why its essential to invest in the best PPE for the rail sector.
Today we all live and work in a society where pretty much every daily task and activity has some form of safety requirement. At work the Health & Safety at Work Act 1974 drives risk assessment. If a risk cannot be eradicated then appropriate Personal Protection Equipment (PPE) is essential.
In larger organisations there are usually personnel who work with European Norms (EN) and understand the technical performance of the various components of a PPE outfit. In recent years this has become less likely, perhaps for financial reasons or lack of time to gain the knowledge required. In some cases it has been handed over to a buyer who is more focused on cost savings and may be responsible for everything from pencils to computers, boots to cars, so being knowledgeable in every area is impractical if not impossible.
Procurement
When organisations put significant effort and resources into PPE procurement the outcome is that the end user gets the clothing that supports them to do their job efficiently and effectively. An organisation should regard PPE as an essential investment which protects its investment in its employees who are a valued resource.
In fact, all workers, whether fully employed, contractors or sub-contractors, have a responsibility to ensure they are wearing the correct PPE for health and safety reasons. But it is not always the case that employers invest in appropriate performing PPE. Sometimes lack of knowledge of the appropriate Norms means buyers are unable to identify the correct requirements, or those requirements are not well documented in the specification which can result in lower cost options being submitted as part of the tender.
Validation of product performance
Problems with procurement can take many forms, such as the product failing to mitigate the risk identified. This could be due to poor specifications, product suitability and qualification or the buying department may not have ensured the actual product meets the tender. In some cases weatherproof clothing with a reasonable specification has failed in use and not kept the wearers dry due to inferior quality components and finish. This has resulted in wearer complaints and work schedules not being completed, loss of relationships and time consuming investigations to resolve issues and the cost of replacements, all pitfalls which could and should be avoided. If the clothing met the specification requirements then these issues would not arise.
What’s SUCAM?
SUCAM is a technical report: ‘Guidelines for Selection, Use, Care and Maintenance of protective clothing’ (TR15321:2006), approved by CEN, which covers the many activities involved in the procurement process and suitability of PPE after ‘installation’. These include risk assessment, wearer trials, lab testing, instructions for use, routine examination, care and cleaning, decontamination, repair, maintenance, storage and eventual disposal.
The Report takes a thorough approach to PPE selection, sourcing and after care. So why doesn’t industry take all aspects of it into consideration? In today’s environmentally-conscious society most organisations have strategic objectives and mission statements relating to environmental issues but it seems they often fail to fully deploy these tactics. For example, weatherproof garments may be procured, issued and then discarded when they have become too dirty or damaged to be effective as PPE.
In particular with HI Visibility GO/RT 3279:2012 clothing, where the reason for selecting this PPE is the need for wearers to be conspicuous, the employer often fails to identify and deploy a cleaning procedure or process. If no cleaning and care programme is in place garments will reach the end of their life much sooner and end up in landfill and replacement garments will have to be issued. Where is the sense in this approach? It does not make for good environmental policy or good procurement practices.
The Report highlights the points an organisation should consider when procuring PPE, including selection, care, use and maintenance of clothing designed to provide protection to the wearer. It is intended for all types of protective clothing with additional guidelines for garments designed to address specific risks. Regulations on health and safety are based on directive 89/656/EEC which gives minimum requirements on selection and use of PPE in the workplace. The EU Member States may impose more stringent requirements and define exposure limits. The Report can serve as a guide and a checklist for a company preparing its own management system or programme for protective clothing.
Railway Group Standard
The GO/RT 3279 standard is based on the European standard EN 20471 which requires garments to meet at least class 2 (the mid-point of a 3-class scale) of EN 471for the minimum area of high-visibility materials used. Rail locomotive headlights pick out retro-reflective materials and the railway standard draws on EN 20471 + A1:2007 and specifies materials that meet the highest level of photometric performance criteria. The standard also defines requirements for a high-visibility minivest. This must conform to class 2 design requirements of EN 20471 + A1:2007, except that it needs to exceed the requirements in EN 471 for both the minimum area of orange background material and the retro-reflective tape used in the garment.
In conclusion, using a methodical, step-by-step approach to Rail PPE procurement, wear and after care will help to further drive down accidents and injury in this sector.
- Ensuring CDM Regs compliance
- HSE Chair calls for consultants to sign up to new benchmark register for health and safety
- Changes to construction site scaffolding regulations:Are you safe?
- Lessons in safety
- The Corporate Manslaughter Act: Why only 2 prosecutions after 4 years?
- Nationwide gets OHSAS 18001 accreditation
- New procedural guidelines at VdS
- Prevention is better than cure
- NQA prize winners
- Latest register of legislation