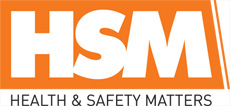
![]() |
Mark Sennett
Managing Editor |
![]() |
Kelly Rose
Editor |
Home> | Managing Health & Safety | >Standards | >Prevention is better than cure |
ARTICLE
Prevention is better than cure
23 January 2013
In light of a number of recent prosecutions for serious breaches of health and safety legislation the NQA explains how developing relevant processes and procedures can help to create a safer working environment It is

In light of a number of recent prosecutions for serious
breaches of health and safety legislation the NQA explains
how developing relevant processes and procedures can
help to create a safer working environment
It is with alarming regularity that we hear or read about accidents at work that could have been prevented. For those involved the injuries they incur are often life changing and this was highlighted recently with the successful prosecution of Cargo Services (UK).
Lorry driver, Robert Deverell, was injured at the company's site in Cardiff Docks as his vehicle was being loaded with 18m steel beams. A forklift truck, owned and operated by Cargo Services, struck Deverell as it reversed and ran over his right leg. Doctors were later forced to amputate the limb below the knee. He also suffered a fractured wrist and has been unable to return to work at Dyfed Steels in Llanelli.
Cargo Services was subsequently charged with breaching Section 3(1) of the Health and Safety at Work etc Act 1974.
What happened to Robert Deverell is not an isolated incident. However, such events can, and should, be prevented by the adoption of an accident prevention and risk management strategy. One of the most effective ways this can be achieved is via compliance with OHSAS 18001.
OHSAS 18001 is the internationally recognised assessment specification for occupational health and safety management systems. It was developed by a selection of leading trade bodies, international standards and certification bodies to address a gap where no thirdparty certifiable international standard existed.
NQA has vast experience in helping organisations implement OHSAS 18001.
Its health and safety sector manager, Jonathan Wilson, explains, "The process involves establishing a management system to eliminate or minimise risk to employees and other interested parties who may be exposed to dangers associated with its activities. It covers both physical and mental wellbeing and includes the monitoring of health and safety management failures, auditing of performance and review of policies and objectives." Certification demonstrates a company's commitment to a safer working environment and the protection of employees against injury at work. It supports an organisation in identifying regulatory requirements and helps to enforce procedures for compliance with legislation. By involving all levels of the organisation through setting objectives, targets and documented responsibilities, a better awareness of health and safety is made possible.
Digging deeper When investigating the events leading up to Robert Deverell's injuries, the Health and Safety Executive (HSE) found that the forklift truck that struck him had a defective reversing alarm and horn.
Records showed that the horn had been faulty for around four years. The HSE also found that there were insufficient segregation procedures at the site to prevent visiting drivers from being too near forklift trucks.
Had OHSAS 18001 been in place these issues could have been avoided, as compliance to the standard is checked against a number of clauses.
In this particular instance clause 4.4.6 Operational Control would have meant that Cargo Services had implemented procedures to control the identified hazards and risks of its operations including stipulating operating parameters and establishing and maintaining procedures for the design of the workplace. Therefore, the defective reversing alarm and horn would have been repaired much earlier, as they would have been tested as part of the compliance process, and segregated areas would have been clearly defined.
In addition, clause 4.4.7 Emergency Preparedness and Response would have ensured that the company had identified the potential for accidents and incidents, and established plans and procedures to respond to them, including the mitigation of any illness or injury.
Counting the cost Some business owners might think that they can't afford to implement an occupational health and safety management system - but the real question they should ask is, can they afford not to? Following the guilty verdict, Cargo Services was fined £110,000 and ordered to pay costs of £60,246.18.
Having to pay these types of sums as the result of a preventable accident will have serious repercussions for the company both financially and in terms of damage to its reputation.
Preventative measures This particular case should act as an incentive for any company that hasn't yet done so to consider OHSAS 18001 certification. NQA's Jonathan Wilson concludes: "Reducing risk for stakeholders in the work environment demonstrates diligence and commitment towards good and responsible health and safety management, significantly reduces the likelihood of accidents, and provides a framework for legal responsibilities.
Furthermore, insurance companies recognise the standard as a means of reducing risk, and offer more attractive premiums."
It is with alarming regularity that we hear or read about accidents at work that could have been prevented. For those involved the injuries they incur are often life changing and this was highlighted recently with the successful prosecution of Cargo Services (UK).
Lorry driver, Robert Deverell, was injured at the company's site in Cardiff Docks as his vehicle was being loaded with 18m steel beams. A forklift truck, owned and operated by Cargo Services, struck Deverell as it reversed and ran over his right leg. Doctors were later forced to amputate the limb below the knee. He also suffered a fractured wrist and has been unable to return to work at Dyfed Steels in Llanelli.
Cargo Services was subsequently charged with breaching Section 3(1) of the Health and Safety at Work etc Act 1974.
What happened to Robert Deverell is not an isolated incident. However, such events can, and should, be prevented by the adoption of an accident prevention and risk management strategy. One of the most effective ways this can be achieved is via compliance with OHSAS 18001.
OHSAS 18001 is the internationally recognised assessment specification for occupational health and safety management systems. It was developed by a selection of leading trade bodies, international standards and certification bodies to address a gap where no thirdparty certifiable international standard existed.
NQA has vast experience in helping organisations implement OHSAS 18001.
Its health and safety sector manager, Jonathan Wilson, explains, "The process involves establishing a management system to eliminate or minimise risk to employees and other interested parties who may be exposed to dangers associated with its activities. It covers both physical and mental wellbeing and includes the monitoring of health and safety management failures, auditing of performance and review of policies and objectives." Certification demonstrates a company's commitment to a safer working environment and the protection of employees against injury at work. It supports an organisation in identifying regulatory requirements and helps to enforce procedures for compliance with legislation. By involving all levels of the organisation through setting objectives, targets and documented responsibilities, a better awareness of health and safety is made possible.
Digging deeper When investigating the events leading up to Robert Deverell's injuries, the Health and Safety Executive (HSE) found that the forklift truck that struck him had a defective reversing alarm and horn.
Records showed that the horn had been faulty for around four years. The HSE also found that there were insufficient segregation procedures at the site to prevent visiting drivers from being too near forklift trucks.
Had OHSAS 18001 been in place these issues could have been avoided, as compliance to the standard is checked against a number of clauses.
In this particular instance clause 4.4.6 Operational Control would have meant that Cargo Services had implemented procedures to control the identified hazards and risks of its operations including stipulating operating parameters and establishing and maintaining procedures for the design of the workplace. Therefore, the defective reversing alarm and horn would have been repaired much earlier, as they would have been tested as part of the compliance process, and segregated areas would have been clearly defined.
In addition, clause 4.4.7 Emergency Preparedness and Response would have ensured that the company had identified the potential for accidents and incidents, and established plans and procedures to respond to them, including the mitigation of any illness or injury.
Counting the cost Some business owners might think that they can't afford to implement an occupational health and safety management system - but the real question they should ask is, can they afford not to? Following the guilty verdict, Cargo Services was fined £110,000 and ordered to pay costs of £60,246.18.
Having to pay these types of sums as the result of a preventable accident will have serious repercussions for the company both financially and in terms of damage to its reputation.
Preventative measures This particular case should act as an incentive for any company that hasn't yet done so to consider OHSAS 18001 certification. NQA's Jonathan Wilson concludes: "Reducing risk for stakeholders in the work environment demonstrates diligence and commitment towards good and responsible health and safety management, significantly reduces the likelihood of accidents, and provides a framework for legal responsibilities.
Furthermore, insurance companies recognise the standard as a means of reducing risk, and offer more attractive premiums."
MORE FROM THIS COMPANY
- A step closer to ISO 45001
- ISO 45001 OH&S training course from NQA
- NQA launches COVID SECURE Guideline Verification
- Ruth Lee & ISO 9001 Quality Standards
- One year down the line for ISO 45001:2018
- Don't get shocked - get checked
- Rexel achieves ISO standard
- The increasing relevance of OHSAS 18001 for SMEs
- Get up to speed with NQA training
- Choose the right certification body
RELATED ARTICLES
- Ensuring CDM Regs compliance
- HSE Chair calls for consultants to sign up to new benchmark register for health and safety
- Changes to construction site scaffolding regulations:Are you safe?
- Lessons in safety
- The Corporate Manslaughter Act: Why only 2 prosecutions after 4 years?
- Nationwide gets OHSAS 18001 accreditation
- New procedural guidelines at VdS
- NQA prize winners
- Latest register of legislation
- Looking ahead to legal changes
OTHER ARTICLES IN THIS SECTION