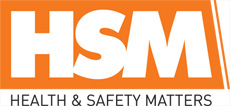
![]() |
Mark Sennett
Managing Editor |
![]() |
Kelly Rose
Editor |
The HAVS and the have-nots
10 May 2013
Hand-arm vibration syndrome (HAVS) is a debilitating condition that can result from over-exposure to vibration in the workplace. Paul Rubens, director of sales & marketing at Svantek, explains how effective monitoring and measurement can help to minimise the risk of employees developing HAVS
In Western societies most people aspire to become ‘Haves’, rather than ‘Have-Nots’, in terms of wealth, although the ‘Haves’ are often looked upon as uncaring, and vice versa. In the workplace, however, these common expressions take on a whole new meaning. It is not a good thing to be a HAV at work, because it signifies that the individual has hand-arm vibration syndrome (HAVS), a serious and sometimes devastating condition that can result if vibration in the workplace is not properly monitored, measured and controlled. It is much better to be a ‘Have-Not’ in this sense, but while no-one wants to be a HAV, two million workers in the UK are actually at serious risk of becoming one.
Causes, effects and symptoms
HAV in the workplace is transmitted into workers’ hands and arms during the execution of their daily tasks. It can occur during the everyday use of any hand-held vibrating power tool or hand-guided equipment, or by holding materials being processed by machines, and is most likely to come about when tools are used for uncontrolled intervals of time.
Permanent damage to nerves, muscles, blood vessels and joints in the arms, hands or wrists – a range of conditions that make up HAV syndrome – can result from regular and frequent exposure to HAV over time. These injuries can cause pain, suffering and reduced grip strength, affecting the ability to perform everyday tasks at home and at work and leading to potential loss of earnings for the victim.
Symptoms of HAVS include tingling and numbness in the fingers, loss of hand strength and white fingers that become red and painful due to reduced blood flow to the hand (vibration white finger). Cold weather and other cold conditions make HAVS worse and with continued use of vibration tools, the condition is likely to become permanent.
HAV is likely to come about when workers regularly use power tools and machines such as concrete breakers, sanders, grinders, disc cutters, hammer drills or powered lawnmowers. Industries where workers are typically at high risk of exposure to vibration include construction, foundries, engineering, heavy steel fabrication and utilities.
Duties of employers
The debilitating effects of HAVS are often underestimated and ignored in the workplace but employers have a legal, as well as an ethical responsibility to prevent their workers contracting HAVS. The Control of Vibration at Work Regulations 2005 state that employers must protect their employees by assessing and identifying control measures to eliminate or reduce risks from exposure to HAV.
This means conducting suitable risk assessments and taking action to reduce exposure by providing alternative working practices or equipment if the daily exposure action values (EAVs), or daily exposure limit values (ELVs) specified by the regulations are likely to be breached.
Risk assessment and management of HAV
Vibration management begins with the risk assessment of any equipment and work process that produces vibration to identify where there could be a risk from HAV, who is likely to be affected, whether further action needs to be taken and how this needs to be put in place.
Employees should be consulted on whether their machines produce vibration and whether they have any of the symptoms of HAV, and the machinery they are using or driving checked, so that action can be taken and controls, information, training and new work methods put in place.
The use of vibration meters to measure the amount of vibration and the length of exposure time from power tools for each operation for which they are used is fundamental to the management of HAV strategy. Vibration meters alert the user to stop using their tools or equipment when they are approaching the maximum exposure levels, thus preventing further daily exposure and ensuring their safety.
Employers should keep their staff informed and aware of HAV by providing updated information and training and explaining good practice to them. If HAV is not monitored and controlled, the consequences for all concerned can be dire, including potential prosecutions or claims against the employer and lost productivity for the business, not to mention the ill health, pain and distress, and reduced ability to work safely, of employees.
In the workplace, it is not a good thing to be a HAV. Far better to take precautionary measures and be a HAV-Not.
- No related articles listed