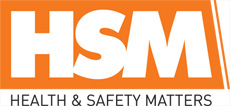
![]() |
Mark Sennett
Managing Editor |
![]() |
Kelly Rose
Editor |
Home> | Health & Wellbeing | >General Health & Wellbeing | >Not working safely? Go home! |
ARTICLE
Not working safely? Go home!
23 January 2013
Glenn Kmecz explains how Dupont has developed an approach to contractor safety management which helped to ensure that a $200 million construction project was completed under budget, on time, and without any recordable injur

Glenn Kmecz explains how Dupont has developed an approach to contractor safety management
which helped to ensure that a $200 million construction project was completed under budget, on time,
and without any recordable injuries in over one million man hours
Confluent factors such as globalisation, the recession and the integration of new technologies and extraction techniques have led to an increased use of contractors across all sectors.
Nonetheless, it is still the operating company that is responsible for maintaining safety in the workplace.
With over 150 sites worldwide, large capital projects involving significant numbers of contractors and considerable risk are relatively commonplace for DuPont, a science-based products and services company.
In the beginning, we had our own construction organisation and was therefore able to refine the capital project management processes, both in terms of safety and efficacy. But when DuPont began to use contractors in ever greater numbers, we confronted the same issues that many companies using contractors still face today: contractors do not share the same safety culture as permanent employees. The question was how to adapt our existing capital project management system to encompass temporary workers that were unfamiliar with the DuPont safety culture.
In 2007, DuPont expanded its Nomex plant in Asturias, Spain and built a new "greenfield" chemical ingredients facility as part of a major capital project worth US$ 200 million - one that involved between 15 - 20 local contractors.
Numerous factors made these expansions challenging: the presence of highly toxic materials, a high ratio of contractors to DuPont employees and an extremely tight schedule. In order to ensure the safety of all workers on site, we had to work closely with each of the contracting companies to ensure their employees knew the rules, were committed to following them and understood the consequences of not doing so. All contractors bidding for the Asturias project were invited to visit the site together, to discuss the project and find out in situ what was expected of them. In other words, we created a level playing field. Even before the project had got underway, all contractors were fully aware of our safety standards and working conditions. Once we had the processes, procedures and commitment in place, our system proved to be effective: the project was completed under budget, on time, and without any recordable injuries in over one million man hours.
Working safely, or not working at all We have frequently sent contractors home if they are not working safely, for example if they violate a cardinal rule about fall protection when working at heights. Of course, this is always done in line with the contract. If a contractor is sent home because he was found to be working unsafely, it sends a strong message to others and reinforces our visible commitment to safe. It is the owner who sets the tone and the pace of a project. If he is proactive and attentive to the needs of contractors, there is a higher chance of avoiding life-threatening situations.
Though it seems daunting to train and monitor temporary workers, establish safety as a condition of work, frame the contract with this tenet in mind and monitor behaviour, this is what makes it possible to complete a large capital project without injury.
The DuPont approach to contractor safety management DuPont has developed an approach to contractor safety management that has proved effective in decreasing the frequency of injuries and accidents among its contractors. The system consists of six complementary processes: (1) Contractor selection While the owner firm plays an integral role, it is the contractor who is ultimately responsible for ensuring the safety of its employees. Selecting a contractor with an exemplary safety record makes it much more likely that the work will be performed safely.
An effective contractor selection process involves evaluating the contractors on their past safety performance. The contracting organisation must seek data like the LTI rate or Total Recordable Frequency Rate (TRR) or similar statistics from the national regulatory body. The owner company should also do a safety competency assessment of the contractor.
Some common mistakes during this step are placing more weight on past records or written programmes than on current safety competency; selecting the lowest bid without examining what the contractor will actually deliver for that price; and using internal decision-makers who do not have right skill sets to make informed choices regarding safety.
(2) Contract preparation When preparing the contract, all contract terms and conditions must clearly document safety parameters, such as expectation for performance, behaviours, standards and capabilities of key personnel.
The parameters should be targeted to the scope of work and be clearly related to a hazard analysis performed by the owner.
Furthermore, the contract must specifically place responsibility and accountability for contractor and subcontractor safety with the main contracted party. On a more practical level, the contract should also define the communication channels through which the contractor will disseminate knowledge relating to safety, and also stipulate that sufficient resources be made available for orientation and training.
(3) Contract Award/Establish expectations and standards - On awarding the contract, the owner company must communicate and test understanding of the safety expectations defined in the contract. The owner cannot assume contractors will read and understand all safety requirements and should walk supervisors through the rules. Roles and responsibilities must be communicated,.
(4) Orientation & Training The owner should use his own knowledgeable, experienced employees to provide effective orientation and safety training. Attributes of an effective orientation include a qualified instructor, proper explanation of the hazards and specific work environment, as well as a system that measures understanding of safety requirements.
Common mistakes made by owner companies during this step are the failure to customize the orientation to suit the audience; the treatment of orientations as a trivial, and thus rushing through them; a disconnected orientation not driven by results; and operating under the perception that orientations are single events rather than an on-going effort.
(5) Managing Contractors and Administering the Contract In order to ensure compliance with safety rules, the owner must develop a robust system for daily monitoring work activities. The main responsibility for monitoring lies with the contracting party, yet a robust enforcement system is also necessary. Key elements of such a system would be formal safety audits and inspections, incident investigations, continuous updating of job plans and periodic review of safety systems. The owner and contractor should jointly develop safety meeting materials, conduct periodic status review meetings, targeted pre-job safety plan reviews and must investigate any incident or accident for potential learnings.
(6) Evaluate safety performance against contractual expectations The owner should critique contractor performance against contractual expectations, and also provide detailed, constructive feedback to the contractor to aid improvement. Where expectations were not met, records must be updated to reflect this. If the contractor has not performed sufficiently as regards safety, they should not be selected for further contracts. Some of the review areas are: injuries/incidents, workers compensation and general liability claims, lost workday cases, TRFR, property and vehicle damage integration.
Glenn Kmecz is global practices leader for Capital Effectiveness and Contractor Safety Management at DuPont
Confluent factors such as globalisation, the recession and the integration of new technologies and extraction techniques have led to an increased use of contractors across all sectors.
Nonetheless, it is still the operating company that is responsible for maintaining safety in the workplace.
With over 150 sites worldwide, large capital projects involving significant numbers of contractors and considerable risk are relatively commonplace for DuPont, a science-based products and services company.
In the beginning, we had our own construction organisation and was therefore able to refine the capital project management processes, both in terms of safety and efficacy. But when DuPont began to use contractors in ever greater numbers, we confronted the same issues that many companies using contractors still face today: contractors do not share the same safety culture as permanent employees. The question was how to adapt our existing capital project management system to encompass temporary workers that were unfamiliar with the DuPont safety culture.
In 2007, DuPont expanded its Nomex plant in Asturias, Spain and built a new "greenfield" chemical ingredients facility as part of a major capital project worth US$ 200 million - one that involved between 15 - 20 local contractors.
Numerous factors made these expansions challenging: the presence of highly toxic materials, a high ratio of contractors to DuPont employees and an extremely tight schedule. In order to ensure the safety of all workers on site, we had to work closely with each of the contracting companies to ensure their employees knew the rules, were committed to following them and understood the consequences of not doing so. All contractors bidding for the Asturias project were invited to visit the site together, to discuss the project and find out in situ what was expected of them. In other words, we created a level playing field. Even before the project had got underway, all contractors were fully aware of our safety standards and working conditions. Once we had the processes, procedures and commitment in place, our system proved to be effective: the project was completed under budget, on time, and without any recordable injuries in over one million man hours.
Working safely, or not working at all We have frequently sent contractors home if they are not working safely, for example if they violate a cardinal rule about fall protection when working at heights. Of course, this is always done in line with the contract. If a contractor is sent home because he was found to be working unsafely, it sends a strong message to others and reinforces our visible commitment to safe. It is the owner who sets the tone and the pace of a project. If he is proactive and attentive to the needs of contractors, there is a higher chance of avoiding life-threatening situations.
Though it seems daunting to train and monitor temporary workers, establish safety as a condition of work, frame the contract with this tenet in mind and monitor behaviour, this is what makes it possible to complete a large capital project without injury.
The DuPont approach to contractor safety management DuPont has developed an approach to contractor safety management that has proved effective in decreasing the frequency of injuries and accidents among its contractors. The system consists of six complementary processes: (1) Contractor selection While the owner firm plays an integral role, it is the contractor who is ultimately responsible for ensuring the safety of its employees. Selecting a contractor with an exemplary safety record makes it much more likely that the work will be performed safely.
An effective contractor selection process involves evaluating the contractors on their past safety performance. The contracting organisation must seek data like the LTI rate or Total Recordable Frequency Rate (TRR) or similar statistics from the national regulatory body. The owner company should also do a safety competency assessment of the contractor.
Some common mistakes during this step are placing more weight on past records or written programmes than on current safety competency; selecting the lowest bid without examining what the contractor will actually deliver for that price; and using internal decision-makers who do not have right skill sets to make informed choices regarding safety.
(2) Contract preparation When preparing the contract, all contract terms and conditions must clearly document safety parameters, such as expectation for performance, behaviours, standards and capabilities of key personnel.
The parameters should be targeted to the scope of work and be clearly related to a hazard analysis performed by the owner.
Furthermore, the contract must specifically place responsibility and accountability for contractor and subcontractor safety with the main contracted party. On a more practical level, the contract should also define the communication channels through which the contractor will disseminate knowledge relating to safety, and also stipulate that sufficient resources be made available for orientation and training.
(3) Contract Award/Establish expectations and standards - On awarding the contract, the owner company must communicate and test understanding of the safety expectations defined in the contract. The owner cannot assume contractors will read and understand all safety requirements and should walk supervisors through the rules. Roles and responsibilities must be communicated,.
(4) Orientation & Training The owner should use his own knowledgeable, experienced employees to provide effective orientation and safety training. Attributes of an effective orientation include a qualified instructor, proper explanation of the hazards and specific work environment, as well as a system that measures understanding of safety requirements.
Common mistakes made by owner companies during this step are the failure to customize the orientation to suit the audience; the treatment of orientations as a trivial, and thus rushing through them; a disconnected orientation not driven by results; and operating under the perception that orientations are single events rather than an on-going effort.
(5) Managing Contractors and Administering the Contract In order to ensure compliance with safety rules, the owner must develop a robust system for daily monitoring work activities. The main responsibility for monitoring lies with the contracting party, yet a robust enforcement system is also necessary. Key elements of such a system would be formal safety audits and inspections, incident investigations, continuous updating of job plans and periodic review of safety systems. The owner and contractor should jointly develop safety meeting materials, conduct periodic status review meetings, targeted pre-job safety plan reviews and must investigate any incident or accident for potential learnings.
(6) Evaluate safety performance against contractual expectations The owner should critique contractor performance against contractual expectations, and also provide detailed, constructive feedback to the contractor to aid improvement. Where expectations were not met, records must be updated to reflect this. If the contractor has not performed sufficiently as regards safety, they should not be selected for further contracts. Some of the review areas are: injuries/incidents, workers compensation and general liability claims, lost workday cases, TRFR, property and vehicle damage integration.
Glenn Kmecz is global practices leader for Capital Effectiveness and Contractor Safety Management at DuPont
MORE FROM THIS COMPANY
- Coverall & guide
- Improving conscious decision-making for risks
- Safer more durable cables
- Operational excellence information day
- Free training
- Comfortable arc flash protective clothing
- Safety and Sustainability Awards 2017
- Process safety solution
- Safety Awards applications open
- DuPont Tyvek - 50 years of scientific innovation in the service of protection
RELATED ARTICLES
- BSIF: Covid-19 Update
- Dust tight
- SAFEContractor for 5th year
- BSC welcomes proposals to slash legal costs in personal injury claims
- Get some insight
- Asbestos remains number one killer
- Chemical exposure course goes more than skin deep
- Getting workers involved in safety
- Dual drug testing
- On-site health screening
OTHER ARTICLES IN THIS SECTION