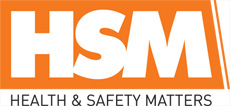
![]() |
Mark Sennett
Managing Editor |
![]() |
Kelly Rose
Editor |
Home> | Managing Health & Safety | >Standards | >Preparing for the unexpected |
Preparing for the unexpected
03 August 2016
Safety consulting is moving into psychology and enterprise risk. Mieke Jacobs, global practice leader operational risk management & employee safety at DuPont Sustainable Solutions, explores these new operational risk strategies.
In an ideal world, people work in a planned environment performing predictable tasks while consistently making rational decisions. But in reality industry operates in often complex situations, with many variables, unknowns and unexpected circumstances.
As professionals in safety, we have worked with companies around the world in industries from rail to mining, pharmaceuticals to oil and gas and have seen what changes a consistent behaviour-based approach to safety and an integrated process safety management system can achieve. Yet there is only so much companies can accomplish with that approach alone.
Statistics by the HSE bear witness to the fact that many UK companies are reaching a plateau in safety performance. In the organisation’s last statistical report the HSE wrote: “Over the last 20 year time period there has been a downward trend in the rate of fatal injury, although more recently (since 2008/09) the trend is less clear.”
In order to manage circumstances that are outside of standardised processes, we at DuPont believe it is important to consider how decisions are selected and acted upon. We have therefore developed an approach to safety that uses neuroscience and affective psychology. This links decision making, conscious and subconscious functioning and affective behaviour, in other words behaviour determined by feelings and emotions.
The balance between risk and reward
When making decisions people almost instinctively balance risk versus reward. Given our past experiences, most of us tend to underestimate risks and overestimate the reward. That often leads to the wrong, unsafe decision.
In a work environment, perceived rewards are everywhere.
- Production pressure will lead to a perceived reward. If you can quickly fix something without locking out, you can continue producing. When you save time, you can also continue with your next task, or take a break, or go home earlier
- Being embarrassed, or not wanting to disappoint your shift or leader – because it will be your shift who was not able to complete the task
- Your personal passion is a strong emotional reward. Typically, maintenance mechanics love fixing things. That’s why they are in maintenance. Waiting for the work permit to be signed, for the equipment to be locked out, for the right oil, etc. does not offer a reward
- Social connectivity is also a powerful emotional reward – why do we text/phone when driving?
Using the risk – reward balance to increase safety
We at DuPont believe we should change conversations to risk and reward conversations and make active use of social contexts. The key question we have to tackle is how to make the right choice the easy choice. What can we change in the environment to allow the correct intuitive choices? There are several methodologies to support organisations.
One is the Nudge Theory: A simple example of a nudge is a walk way in a factory, with feet painted on it. This will nudge people to use it as a path. A colour coded lock-out situation will nudge people to connect the right lock to the right lock out point.
Another area is what we call ‘Lean Thinking in the area of risk and safety’. This looks at the flow of operations or activities from a risk/reward perspective. If a walkway results in a 10-minute detour several times a day, you can be sure that the perceived reward of taking a shortcut is very high, versus the risk of not using the walkway. The idea is to improve workflow so that people are not tempted to take shortcuts. This will not only improve productivity but also significantly reduce risks.
Automated behaviour starts with a cue. A routine triggers a behaviour and a perceived reward. To change a habit, we need to change the cue, the perceived reward and the behaviour, forming and maintaining new habits through repetition and reinforcement.
The new operational risk approach
DuPont now focuses on building capabilities that engage people at an emotional level to change their mindsets and behaviours. The insights gained allow us to develop solutions so people make more rational decisions.
For this to work, it is critical to understand what an organisation’s specific risk profile is, including its tolerance and awareness of risk. This can be done through assessments, behavioural interview techniques and focus group discussions. We then work on challenging preconceptions of safe and unsafe actions, drivers for decision-making, and change the way in which people perceive, analyse and approach risk. It is also critical that senior leaders and supervisors understand their role in shaping the decision-making process of their staff. So we work on helping them inform, inspire and influence their workforce. This approach uses insights from cognitive and affective psychology, as well as neuroscience to move companies off the plateau their safety performance has reached.
- Comfortable arc flash protective clothing
- Kevlar innovation awards
- Protective coveralls
- Risk assessment guide is no flash in the pan
- Call for award entries open
- Suits use in labs
- DuPont Tyvek - 50 years of scientific innovation in the service of protection
- Dedicated web resource
- Not working safely? Go home!
- Coverall & guide
- Ensuring CDM Regs compliance
- HSE Chair calls for consultants to sign up to new benchmark register for health and safety
- Changes to construction site scaffolding regulations:Are you safe?
- Lessons in safety
- The Corporate Manslaughter Act: Why only 2 prosecutions after 4 years?
- Nationwide gets OHSAS 18001 accreditation
- New procedural guidelines at VdS
- Prevention is better than cure
- NQA prize winners
- Latest register of legislation