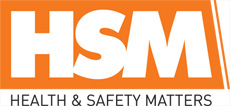
![]() |
Mark Sennett
Managing Editor |
![]() |
Kelly Rose
Editor |
Home> | PPE | >Head Protection | >Doing it right |
Doing it right
07 March 2019
Ian Goodhead discusses Winvic's internal policies on head protection and task specific PPE.
IN 2018, Winvic’s HSEQ team of eight covered a large number of projects across five main operating sectors – 30 were completed, 42 new ones started. We trained the operatives from 279 different suppliers and the individuals employed by Winvic; at the end of December 2018, this was 300 people. From enforced head protection to mental health training, from underground service training to a fair cautioning process, our activities are born out of a desire to ‘do it right’. Our 93.2% staff retention rate is testament to our approach to the role as a protector and investor in people. Reducing our RIDDOR Average Frequency Rate of incidents from 0.21 in 2017 to 0.16 in 2018 – when one million more man hours were used – is proof that our recent process and policy transformations are effective.
Legislation on keeping people’s heads safe isn’t as precise as you might think, with Health and Safety Executive PPE guidance stating: “If there is no risk of injury to the head, then hard hats are not required by law. However, on almost all construction sites, despite controls being put in place, there will almost always be situations where a risk of head injury remains.” Also, the suggested options are “A range of helmets [and] hard hats.” I’m not sure it would be wrong to say there is room for interpretation in the guidance, and an incorrect analysis of a situation – easily done – can lead to injury, or worse.
It was one of our senior HSEQ managers, Adrian Bracken, who really started the ball rolling on our re-examination of head protection. He was appointed as a dedicated on-site health and safety manager at SEGRO Logistics Park East Midlands Gateway – a project first for Winvic – on the 700 acre site, and the goal was for Adrian to integrate within the project team and better understand the needs on the ground. He embodies The Winvic Way – he is respectful, loyal, honest, passionate, and questions industry standards to keep people safe – and only someone like Adrian, who is genuinely concerned about every person, could effectively obtain buy-in from so many. Peak days on-site equalled approximately 700 operatives from 30 different contractors.
Adrian knew that understanding subcontractors’ points of views was integral to successful training and for the supply chain to buy into our proposals. Not only would helmets have to be worn on site at all times but now also chin straps would be compulsory and hand tools must be tethered when working on a mobile elevating work platform (MEWP). Initially, the feedback wasn’t 100 per cent positive so Adrian undertook assessments on the effective management of exclusion zones. Working with colleague Adam Topham, a HSEQ manager, who was tasked with giving all of our in-house training programmes a face-lift, they highlighted the risk of harm; helmets can and do fall off, or get knocked off, and equipment or materials can and do get accidentally dropped. With tangible results and a sensitive approach, suppliers embraced the changes and didn’t see our safety advancements as ‘more unnecessary compliance’.
The domino effect
The simple conclusion was we can do things better and keep more people safe, so very quickly the lessons learned from SLPEMG became company policy for all our sites. Adrian’s focus on a project of such scale sparked transformative changes for Winvic and our supply chain and gaining support from our executive team meant all Winvic-delivered training was offered to all subcontractors. The changes came thick and fast and it’s humbling to hear that most of our subcontractors have since adopted Winvic’s internal standards across the whole of their companies too.
We work very closely with our suppliers in creating accurate risk assessments before they take a step on site, and task specific PPE is a significant area. This means we effectively create a new, specific checklist with each activity and each subcontractor, but then spot checks are regularly carried out on all sites. For example, my managers will ask operatives to remove their eye protection and if they are found to be the incorrect grade in relation to the potential impact, they will have to stop work until the appropriate face-shield or goggles are being worn. With ear protection, we encourage everyone to avoid using ear plugs in favour of clip-on ear defenders; disposable ear plugs easily get lost or dirty and this can leave people with no ear protection when it’s needed or with a nasty ear infection. Furthermore, they litter the site and they have a negative environmental impact.
HSE’s Approved Codes of Practice (ACoPs) that support COSHH, CAR and CLAW stipulate that “tight fitting Respiratory Protective Equipment (RPE) must be fit tested as part of the selection process”.However, the Fit2Fit RPE Fit Test Providers Accreditation Scheme websitecites that up to 50% of all RPE used does not offer the wearer the level of protection assumed due to an ill-fit. The dislocation between legislative requirements and realities on the ground lie with competencies of people performing the fit testing. Undertaking a major diversion of a gas main at SLPEMG was a stark reminder of the risks. We set our sights on increasing everyone’s knowledge of atmospheric hazards, from dust to dangerous gasses, and my team was upskilled on the most accurate fit testing processes. Why push the risk aside to the subcontractors, when we can provide assistance?
Education and training
Adam Topham undertook external training on RPE fit testing then devised an in-house session for the rest of the HSEQ team on how to correctly face-fit disposable respirators, full and half face masks fitted with particulate or combination filters. As the driving force was to better support subcontractors, the HSEQ managers now schedule visits to sites when masks are being used; they can assess working practices, undertake fit tests if required and provide advice to key personnel. The dual test comprises a number of exercises, such as breathing deeply, bending over at the waist and talking, after solutions have been placed in the test nebulisers. Should no taste be detected, the mask is correctly fitted. In the sensitivity test, the taste should be detected.
With ‘carte blanche’ to review Winvic’s in-house training, Adam updated and added to the suite of programmes, developing them through delivery and then training HSEQ colleagues to deliver the refined courses. While this may sound fairly standard, our secret weapon lies within Adam’s ability to make sessions relevant and engaging. The overhaul of all programmes included revised presentation and trainee materials, quiz questions and case studies. A great example of Adam’s style can be seen in a series of gifs he uses to illustrate the dangers of not wearing a hard hat, as well as one without a chin strap. Bolts are dropped from height on a watermelon with a face – at first wearing a helmet, and again after the hat has been knocked off with the first missile – and the effects are shocking. Adam’s warm, light-hearted presentation style works to astonishing affect; it and the team camaraderie he generates provide stark contrast to the very real site risks.
Our proactive, high-standard safety training for employees and subcontractors not only includes a one day minimum health and safety competency course, which covers head protection, but we are also advocates of using task specific PPE. Our honest and sincere approach to keeping people safe means suppliers put their trust in us 99 per cent of the time; we don’t make rules for rules’ sake, and understand some items of protection can cause impediments when getting a job done, for example we don’t expect eye protection to be worn all the time. When we can demonstrate clear risk and benefit, operatives are more than happy to reach for the prescribed equipment.
Respectful rehabilitation
The majority of my team enjoyed hands-on construction careers before they were moved into health and safety roles, and this has resulted in a collective, deep understanding of real hazards and doing what we can to avoid the smallest incident. This also means we appreciate that anyone can make a mistake, a problem can never be solved by just pushing it onto another employer and we don’t want to take someone’s livelihood away when an issue can be remedied through learning. Dismissal is always the last resort.
By not subscribing to industry ‘norms’, such as the misconduct yellow/red card system, we believe we have a fair, respectful and forward-thinking approach to dealing with safety transgressions. For example, when Joe Engineer is spotted with an un-tethered hand tool in a cherry picker ten metres above the ground he will first be asked to come down to the ground and explain his actions. This contravention – and in also for the majority of cases – will result in Joe having to undertake a ‘toolbox talk’ in front of his peers. He will have to explain what he did and why he took the risk, and what he will do next time to correct the mistake. I believe attitude is everything, but even a hot head won’t be sacked on the spot if they’re not immediately repentant; I’ve worked with enough people over my 32-year career to know that some people need time to cool down. People return the next day ready to start a new day, follow the correct procedures and prepare for their explanation to their peers. Everyone is happy and everyone is a little safer.
I’m proud to say my team rejects ‘humdrum health and safety’ and focusses on changing perceptions to make tangible differences in keeping heads – and bodies - safe. We never shy away from questioning how things are done and aim to make every piece of training relevant and engaging. Changes to our head protection policies and methods have been led by solutions, not legislative tick-boxes, and we trust that our unceasing fresh thinking will continue to save lives.
Ian Goodhead is HSEQ director at Winvic. For more information, visit www.winvic.co.uk
- Furniture manufacturer failed to manage vibration exposure
- Crown Censure issued following death of soldier
- £400,000 fine after workers injured by fork lift trucks
- Fine after girl crushed by school gate
- New report shows fire safety compliance concerns
- Workers complacent over Swine Flu risk
- Noisy workspaces keeps staff at home
- Sicker workforce dampens labour stats
- Farmers urged to rethink risk
- Bedford business fined after employee falls from racking