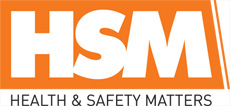
![]() |
Mark Sennett
Managing Editor |
![]() |
Kelly Rose
Editor |
1/357 (1 to 10 of 3569)
Third of workers not using health benefits | 19/08/2025 |
---|---|
NEW DATA from healthcare services and plan provider Simplyhealth reveals that many employees are not using their workplace health benefits due to barriers to accessing them. Spanning the views of both employees and employers, Simplyhealth’s research shows that a third (34%) of British workers don’t use their workplace health benefits at all, while over half (53%) that do use them have experienced barriers to accessing them. In terms of specific barriers to access, a sixth (16%) of employees said they had to ask their line manager for information or approval beforehand, while more than one in ten (13%) needed pre-authorisation from their manager or insurer to use their health benefit. A similar proportion (13%) found the process too complicated, while 9% said their pre-existing conditions were not included in the cover. There is clear demand for health benefits to be simpler, with over a third (37%) of employees saying this would make them most likely to use the benefits. This is followed by quick access to health services (36%), and cover for pre-existing conditions (22%). Overall, a fifth of employees (20%) said they would be more likely to use their health benefits if they knew their claims would be paid quickly, and if it meant they didn’t have to take time off work for appointments (19%). Employers want to do more Simplyhealth’s research also reveals that employers feel a responsibility to do more to support their workforce, with three quarters (73%) wanting to look after their employees’ health due to longer NHS waiting times. Despite this, most employers (86%) have at least one concern or worry when putting in place health benefits for their employees. For example, nearly a third (31%) are worried that they will have difficulty finding health plans for employees with pre-existing health conditions. The benefits of simple, accessible workplace health benefits are also clear. Six in ten (60%) employees say it makes them happier at work, nearly half (48%) say health benefits are an important reason for staying in their job. For those not currently receiving workplace benefits, over half (54%) say having them would make them more productive at work, while a similar proportion (48%) believe they would take fewer sick days as a result. Paul Schreier, CEO at Simplyhealth, said: “Employers recognise the huge responsibility they have to support the health of their people and the value it creates in terms of reducing long-term sickness and boosting productivity. Workplace health benefits are a big part of these efforts, but too often traditional offers are complex and difficult to access. “The government’s 10-Year Plan for the NHS has put prevention at heart of ambitions for the health service, and businesses are very well placed to further those objectives –promoting preventative healthcare that improves productivity while easing pressure on the NHS. “Simplifying health benefits is one of the first steps businesses can take. It’s why at Simplyhealth we’ve focused on developing a range of affordable healthcare services, including 24/7 GP access, mental health support, health cash plans and pay-as-you-go services. These aim to simplify access, reduce costs and boost uptake, with no GP referral or pre-approval required and the majority of plans covering pre-existing conditions.” The government recently published its 10-Year Plan for the NHS, which looks to improve patient outcomes and ensure the sustainability of the health service, by shifting focus onto community services, greater digitalisation and prevention over treatment. Improving workers’ access to healthcare has the potential to reduce long-term illness, boosting economic activity and furthering the government’s wider growth ambitions. Some 2.8 million working age adults in Britain are currently out of work because of a long-term health condition1, and more than 200,000 people left work specifically for health reasons in 2023-24 2. This sickness crisis has led to Britain’s economy being 10% smaller than it would otherwise be3, holding back growth and productivity, and costing £150 billion per annum4. To help get more employees to access healthcare, Simplyhealth says it makes it easier and more affordable for employees to access healthcare. References |
|
|
|
Industries with highest workplace illness revealed | 19/08/2025 |
RESEARCH HAS revealed that health and social care workers are the worst-affected by workplace illness, as a new government pilot scheme aims to address worrying annual sick note volumes. The £1.5 million WorkWell pilot will see specialist staff placed in GP practices to help tackle the 11 million fit notes issued last year - 93% of which offered no guidance - by connecting patients with tailored support to stay in or return to work. Health and Safety Executive (HSE) data reports 1.7 million cases of work-related illnesses in total annually, which cost UK businesses a staggering £14.5 billion each year. The business finance experts at money.co.uk business savings have analysed the latest HSE data on workplace illness to identify the industries where businesses face the most significant challenges. Industries with the highest rates of workplace illness: *Three-year average of new cases (2021/22-2023/24) - industries with sample sizes marked as too small have been removed. Topping the list is the human health and social work sector, with around 129,000 cases of work-related illness reported for workers’ current or most recent jobs, a rate of 2,780 per 100,000 workers (or about one in 35). Roles in this sector are often physically and emotionally demanding, from providing care to managing complex human needs. These figures highlight the importance of continued focus on wellbeing support, adequate staffing, and mental health resources for those on the front line of care and support. Joe Phelan, money.co.uk business savings expert, comments: "With the daily pressures of running a business, it's easy to push savings down the priority list. However, this data is a stark reminder that a healthy contingency fund isn't a 'nice-to-have' – it’s crucial to protecting your people and your operations. “By building a safety net, you’ll be better placed to support colleagues, while keeping the business running smoothly. Building up a contingency fund doesn’t have to be complicated. Even small, regular contributions to a savings account can help businesses stay resilient through staff absences, workplace incidents, or crime-related disruptions. “These accounts allow you to earn interest on your savings and, crucially, the money is on hand the moment you need it. This can help you protect your employees and your business if your team members get injured or fall ill, or if you’re a victim of a crime.” |
|
|
|
Civilian crushed by faulty lift | 19/08/2025 |
A LONDON property developer has been fined £40k after a member of the public was crushed by a faulty falling lift at a block of flats. The 23-year-old had returned to the flats on Cambridge Heath Road in East London, with a group of friends on 9 September 2019. When he and seven others entered the lift on the ground floor, it began to shudder and descend with the doors still open. As it began to fall, the young man attempted to exit the lift but he was crushed between the ground floor and the top of the lift. The crush injuries he sustained were so serious he eventually required a liver transplant. Nofax Enterprises Limited had been acting as the property manager for the five-storey block flats. The investigation by the Health and Safety Executive (HSE) found that it failed to act when defects with the lift were identified by a third party, resulting in a member of the public being harmed. Health and safety law places specific obligations on those providing, controlling and using lifting equipment. HSE has detailed guidance for how to properly manage these risks. Thorough examinations should be carried out by a competent person at six month intervals for lifts designed to lift people. When a defect is identified that poses a danger to people the lifting equipment should not be used until the defect is remedied. Nofax Enterprises Limited of Swiss House, Beckingham Street, Tolleshunt Major, Essex, pleaded guilty to breaching Section 3(1) of the Health and Safety at Work etc. Act 1974. The company was fined £40,000 and ordered to pay £8,540 in costs at Southwark Crown Court on 22 July 2025. HSE inspector Pippa Knott said: “As a result of this company’s failures, a young man who was simply returning from a night out with friends has suffered life-changing injuries. “The fine imposed on Nofax Enterprises Limited should underline to everyone in property management that the courts, and HSE, take these failures extremely seriously. “We will not hesitate to take action against companies which do not do all that they should to keep people safe.” This HSE prosecution was brought by HSE enforcement lawyer Nathan Cook and paralegal officer David Shore. |
|
|
|
Chemical company fined after worker suffers burns | 19/08/2025 |
A CHEMICAL company has been fined £100k after one of its workers was permanently scarred from burns from a steam hose at a site in Motherwell. A 23-year-old was burnt across his back and other areas of his body as he attempted to clean a process water tank on 23 October 2019. At the time he had been working for Dundas Chemical Company (Mosspark) Limited at its site at Omoa Works in Newarthill for around two years. The company operates a large rendering plant that processes animal waste and food industry waste to produce proteins, fats and oils used in the oleo chemical, fuel, and feed industries. As a result of this process, the water tank and vickery would need occasional cleaning. It was during a nightshift that the man had been instructed to undertake cleaning duties on the process water tank, the vickery and the walls and floors in that area. The company provided pressure washers as well as a steam hose for cleaning down difficult areas where there may be tallow or other animal residues. The steam hose was heavy and cumbersome to manoeuvre, with the uninsulated nozzle also becoming hot.. The man and a colleague therefore took it in turns to carry out the steam hose task. After a period of time they stopped to have a break. While his colleague then went on to carry out other duties, the 23-year-old proceeded to finish the cleaning on his own. He did this with the aid of a small cherry picker – attaching the steam hose to its basket. After the basket had been raised to the required height, the steam hose and nozzle spun round and steam began flowing into the cherry picker basket directly at him. He quickly turned his back to prevent his face being burned, while manipulating the nozzle of the hose away from him and lowering the basket of the cherry picker, at which point he was then able to run through to one of the deluge showers to cool his burn injuries. He was taken to hospital with steam burns to several parts of his body, which have left scars to this day. An investigation carried out by the Health and Safety Executive (HSE) found the nozzle fitted to the steam hose was unsafe as it did not have a trigger or other mechanism fitted to allow the operator to start or stop the flow out of the nozzle at the point of operation. It also found that the mixing valve and set-up for supplying hot water for cleaning purposes was not maintained in an efficient working order or in good repair. Supervisors at the site were aware that the mixing valve was passing steam, however no action was taken to investigate the issue or prevent it from happening. HSE inspectors also found the maintenance and engineering team had no sound engineering understanding of the risks involved when setting up such a washdown system and how to mitigate or control those risks. The company provided information to HSE that there were no records associated with the maintenance of the valve, hose or nozzle. Dundas Chemical Company (Mosspark) Limited, of Mosspark, Brasswell, Dumfries, pleaded guilty to breaching section 2(1) of the Health and Safety at Work etc Act 1974. It was fined £100,000 at Hamilton Sheriff Court on 18 August 2025. HSE inspector Ashley Fallis said: “Had a safe system of work been in place then this incident would not have happened. “The lack of appropriate risk assessment, method statements, training and supervision for both the maintenance team who installed the valve, and the operators tasked with using the system, led to a situation where those involved were unaware of risks or simple control measures. “This catalogue of failures resulted in a young man sustaining very serious burns, to which he still bears the scars to this day. “We will not hesitate to take action against companies that fail to protect their employees.” |
|
|
|
Pharmacy teams face threats and abuse, survey finds | 17/08/2025 |
A NEW survey finds that 87 per cent of phamacy workers have seen an increase in aggressive and intimidating behaviour in the last year, while 22 per cent have seen physical assaults on staff. Of those that reported these criminal incidents to the police, 73 per cent believed they received an insufficient response. The National Pharmacy Association (NPA), who represent over 6,000 independent pharmacies in the UK, have condemned the abuse of hard working pharmacy staff and urged the police to do more to deter shoplifters. The survey of around 500 pharmacies by the NPA found that 9 in 10 (88 per cent) of pharmacies have seen a surge in incidents of shoplifting in the last year. Pharmacies have warned that the potential theft of medicines, including controlled drugs, could have serious consequences for someone's health and may be being stolen for criminal gain. Some medicines could be being mixed, making dangerous concoctions, and theft from pharmacies is potentially a more serious criminal offence than common shoplifting. Some pharmacies have reported to the NPA that they have taken additional steps to protect their teams, such as the introduction of body worn cameras and the employment of security staff. Some pharmacies have also reported that hostile behaviour from a minority of patients can be caused by frustrations due to national shortages of certain medications. Pharmacy teams can often be more vulnerable to threatening or abusive behaviour than other parts of the NHS. Pharmacies are often more isolated and can bear the brunt of frustrations from patients who been let down by wider parts of the health system. Pharmacies are not required to supply NHS medicines to people committing or threatening to commit a criminal offence or who is accompanied by someone doing so. The NPA have called on the NHS to provide a similar level of support that is offered to other parts of primary care, such as GP practices, to help protect pharmacies and their teams. In the past, the NHS has provided funding to GP surgeries to make changes to improve security, such as to fit panic alarms and install CCTV. Around 90-95 per cent of an average pharmacy’s work is providing NHS services such as the dispensing of medication or running vaccination campaigns. Henry Gregg, chief executive of the National Pharmacy Association said,, "These are appalling findings and show that pharmacies are seeing a significant increase in shoplifting and other criminal behaviour. “It is particularly concerning to hear of reports of physical assaults as well as threats towards pharmacy staff, which is totally unacceptable. "Due to their accessible nature, pharmacy teams can often be more exposed to abuse and threats than their primary care colleagues. “Although pharmacies are taking their own steps to protect their staff and premises, the police should do much more to tackle crimes like shoplifting which is becomingly increasingly common place. “We need to do more to tackle shoplifting as well as offering pharmacies similar support to other NHS colleagues in primary care to protect their staff and their premises.” |
|
|
|
RoSPA urges action as pedestrian deaths hit 400 annually | 17/08/2025 |
THE ROYAL Society for the Prevention of Accidents (RoSPA) is calling for immediate government action to address the ongoing crisis of road deaths and serious injuries in England. On Sunday 17 August, road safety campaigners remembered Bridget Driscoll, who was killed by a driver of a motor vehicle in 1896, and was the first recorded road fatality. Since then, there have been over 500 thousand fatalities on British roads. RoSPA uses this anniversary to highlight the urgent need for the government to adopt two critical reforms: introduce a road safety strategy for England and establish a dedicated body to investigate serious road incidents. Rebecca Guy, senior policy manager at RoSPA said, “For the past few years, England has remained the only UK nation without a refreshed national road safety strategy in place. The news that Labour will be publishing its own in the Autumn is a welcome move, but it is vital that it is a coordinated framework with clear targets and accountability to reduce fatalities and serious injuries. “Secondly, unlike aviation and rail, road collisions are not routinely investigated by an independent authority. RoSPA supports the creation of a specialist body to examine serious and fatal incidents, identify systemic risks, and prevent future tragedies. “Bridget Driscoll’s death was the first recorded road fatality in the UK. More than a century later, lives are still being lost unnecessarily. These reforms are essential if we are serious about saving lives.” The recommendations are drawn from RoSPA’s recent National Accident Prevention Strategy report, titled Safer Lives, Stronger Nation—a cross-sector initiative aimed at reducing accidental harm across the UK. The strategy outlines a clear roadmap for improving road safety, including additional measures such as Graduated Driver Licensing (GDL) to protect young drivers. |
|
|
|
HSE issues urgent offshore gangway safety notice | 17/08/2025 |
THE HEALTH and Safety Executive (HSE) has issued a safety notice to highlight the risks of potentially fatal gangway accidents to offshore workers. Serious risks have been identified where motion compensated gangways retract without warning due to power failures or control system errors. This puts workers at risk of falling from height, being struck by moving parts, or suffering serious injuries including death. HSE is calling on operators in oil and gas, and renewable energy sectors to review their gangway arrangements. Any gangways that cannot provide sufficient warning before automatic retraction must be taken out of service until proper safety controls are installed. Howard Harte, operations manager (Offshore Regulation) at the Health and Safety Executive, said: “Despite a previous safety alert in 2024, and the publication of industry good practice, we have become aware that gangways that provide insufficient warning before auto-retraction are still being used in the offshore oil and gas and renewables industry. “This safety notice addresses continuing incidents where gangway failures have resulted in unexpected retraction without adequate warning to operators or personnel crossing between platforms. Workers have been left unable to move to safety or brace for sudden movement when systems fail.” Under the requirements, dutyholders must conduct technical risk assessments of all automatic gangway functions. Control systems must only allow auto-retraction when personnel are confirmed safe. The use of gangway operators to manually override automatic retractions requires rigorous risk assessment. The HSE emphasises that adequate warning systems must provide advance notice before dangerous events occur. Howard added: “A warning by definition is advanced notice that a potentially dangerous event is about to occur. The purpose of the warning is to enable persons to make themselves safe before the event occurs. Audible and/or visual alarms that are triggered at the same time the gangway retracts are not considered to provide adequate warning to enable workers to reach safety.” Dutyholders must review their gangway design, including the testing that has been carried out of all automatic functions. They should carry out a suitable and sufficient technical risk assessment to understand all operational states of the control system under which the gangway may auto-retract, including that the control system will only result in auto-retraction if personnel are not at risk. Use of gangway operators to override auto-retractions should be rigorously risk assessed. The safety notice can be viewed at: https://www.hse.gov.uk/safetybulletins/motion-compensated-gangways-auto-retraction.htm |
|
|
|
Stress is main cause of workplace incidents, research shows | 17/08/2025 |
NEW RESEARCH from EcoOnline reveals that 44% of workers have been involved in a workplace incident or know someone who has - and stress is the main cause. EcoOnline has released its latest research findings: How Safe & Sustainable Is Your Workplace? The study surveyed over 5,700 employees across North America, the UK & Ireland, and the Nordics to understand how safe and sustainable workplaces really are, from the frontline view. The findings from 1,000 UK&I workers expose gaps in chemical safety, digital solutions and lone worker protection – alongside rising stress levels – calling for a renewed focus on the full workplace experience. How safe are UKI workplaces? Workers overwhelmingly feel that their workplace is safe (82%), however nearly half (44%) have personally experienced, either themselves or through a relative, a workplace accident or work-related illness. The majority relate to stress, affecting 64% of UK&I workers, higher than the global average (59%) and North America (54%). Exposing chemical safety gaps Chemical management is complex and rife with risk. 42% of UK&I workers are exposed to hazardous chemicals and, of that, 37% say their company is not actively working to substitute hazardous chemicals. Though 83% have received chemical handling training and 75% have access to Safety Data Sheets (SDS), major digital gaps remain. 40% of employees lack access to QR codes for SDS and 36% have not been provided with a digital chemical management system, highlighting a critical chemical safety shortfall. Rising pressure on lone workers Over a third (35%) of UK&I workers classify themselves as lone workers. While 68% say their employer takes lone worker safety seriously, only 41% strongly agree – showing a notable confidence drop compared to 53% across the full workforce who strongly agree their workplace is safe. Top concerns among lone workers are psychosocial: fatigue (48%), stress and mental health (43%), and threats of aggression (42%). Concerns also vary by country –aggression or assault ranks second highest in the UK at 44%, whereas accidents and falls are the second biggest worry in Ireland at 46%. Digitisation and AI: Trust in a Safer Future? Two-thirds (67%) of employees say they’d feel safer with more digital health and safety tools, rising to 82% among those aged 18-34. Digital training is already widely used – 86% of those trained used e-learning – but other areas still lag. Nearly half (48%) want digital incident reporting, yet most still rely on manual processes. While just 20% believe AI will “definitely improve” safety, 65% of workers are open to AI improving workplace safety, increasing to 78% for 18–34-year-olds. Trust will depend on how it’s implemented, and the biggest opportunities lie in showing how AI can support, not replace, human safety processes, with potential use cases such as predictive alerts or virtual assistants. Safety and sustainability: Two sides of workplace experience While health and safety is a key part of workplace experience, sustainability matters deeply too. 76% of workers say environmental responsibility is important, and 54% say their employer placed greater focus on sustainability in 2024. However, only 34% say their business uses a recognised Environmental, Social and Governance (ESG) framework and 29% don’t know what ESG is, signalling a disconnect between ambition and understanding. Speaking on the research, EcoOnline’s CEO, Tom Goodmanson, said, “Today’s workplace experience hinges on the three S’s: Safety, Stress and Sustainability. Supporting employee wellbeing means going beyond compliance – creating environments that are productive, supportive, and safe. With 82% of workers saying they’d consider leaving due to poor conditions, the link between safety, sustainability and job satisfaction is clearer than ever. Embracing technology to tackle psychosocial risks and make tangible sustainability commitments will be essential to keeping people protected and engaged.” Read the full report for further insights on frontline worker perspectives. |
|
|
|
Care home provider fined after death of patient | 13/08/2025 |
A CARE home provider has been fined more than £50k after an elderly patient died in the early hours of Boxing Day in 2022. Hugh Kearins, 77, had managed to leave the Chester Park Care Home in Glasgow via a series of stairways and fire doors. An inspector from the Health and Safety Executive (HSE) counted 320 steps from Mr Kearins’ room to the care home’s car park just off Lambhill Street, where his body was found at around 7am. Mr Kearins, who had dementia, had been living in a room within the Clyde Unit of the home since 2012. As part of its investigation, HSE made enquiries regarding the use of an internal fire door and was unable to obtain corroborated evidence of who was last to use the door prior to Mr Kearins, who is thought to have exited through it just before 1am. The same door was closed about an hour later by an unknown member of staff carrying out routine checks. It was confirmed by the care home manager that once the door was noted to be insecure, the member of staff should have initiated a head count of all of the residents to ensure their safety. However, this was not carried out. The HSE investigation found the company had failed to have a safe system of work in place. Records held by the company in relation to Mr Kearins, extensively noted the clear risk that he might abscond or ‘wander’. It was part of his care plan that he be checked or monitored every hour. HSE guidance states that the security of doors and gates should be considered where assessment identifies that specific residents leaving the premises will present a significant risk to their safety. It adds that in some instances it may be appropriate to consider devices that alert staff of their location and whether they are at risk of harm. A senior care assistant and a care assistant who had responsibility for Mr Kearins’ care were also found to have falsified records, stating that they had performed tasks involving him at a time when he was in fact no longer in the home. Both were unaware he was no longer in his room until news of his death became known following the discovery of his body in the car park. The management failures in respect of the alarm door reactivation were not causative of Mr Kearins’ death and would likely not have even come to light but for four individual errors:
Oakminster Healthcare Limited, of Lambhill Street, Glasgow, pleaded guilty to breaching Sections 3(1) and Section 33(1)(a) of the Health and Safety at Work etc. Act 1974. The company was fined £53,750. HM Inspector Amna Shah said: “This incident was completely avoidable. It is hugely concerning that a vulnerable man was able to walk so far and through so many doors without being noticed. The fact this incident happened at Christmas time makes it all the more tragic. “We will always take action against those who fail in their responsibilities.” |
|
|
|
Waste firm prosecuted after worker crushed by excavator | 13/08/2025 |
A COUNTY Durham waste management company has been fined after a young employee was run over by an excavator. Farm XS (Northern) Limited, based in Barnard Castle, was sentenced after an incident on 29 January 2024 that left the 24-year-old with serious injuries. The employee was only in his second week of employment at the Staindrop Road site when he was struck from behind by an excavator and run over. He suffered fractures to both feet. An investigation by the Health and Safety Executive (HSE) found that the company had failed to ensure a safe system of work was in place. The 24-year-old was working on a waste pile near moving vehicles with no physical separation between them. There was no risk assessment or system of work to protect pedestrians from vehicle movements. HSE guidance clearly states that pedestrians and vehicles should be segregated when waste is being manually sorted. By law, employers must ensure traffic routes can be used without risking the safety of workers nearby. The case against Farm XS (Northern) Limited, Shaw Bank, Staindrop Road, Barnard Castle, County Durham, DL12 8TD, was heard at Teesside Magistrates’ Court on Tuesday 5 August 2025. The company pleaded guilty to breaching Section 2(1) of the Health and Safety at Work etc. Act 1974.It was fined £4,000 and ordered to pay £4,285 in costs. After the hearing, HSE inspector Richard McMullen said, “The outcome could have been much worse. But the failures that day meant a worker received serious injuries. “This incident was easily avoidable by implementing control measures and safe practices to ensure that workers were not put at risk from moving vehicles, including clear segregation and safe refuges. “This should be a reminder to the waste industry of the need to consider workplace transport risks and to introduce appropriate control measures to separate vehicles and pedestrians.” This prosecution was brought by HSE enforcement lawyer Iain Jordan and paralegal officer Helen Jacob. |
|
|