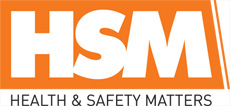
![]() |
Mark Sennett
Managing Editor |
![]() |
Kelly Rose
Editor |
Home> | Managing Health & Safety | >Noise Monitoring | >Sound control |
Sound control
10 June 2021
There is still more to be done when it comes to controlling noise at work. Here, Laura Jenkins explores five steps you can take to ensure you are fulfilling your obligations.
ALTHOUGH GREAT strides in noise control have been made by companies since the introduction of the 2005 Control of Noise at Work legislation, there is more to be done; according to the UK’s Health and Safety Executive some 17,000 people in the UK suffer deafness, tinnitus or other ear conditions as a result of exposure to excessive noise at work.
It seems the problem of understanding noise remains in several industries and many people don’t know where to start in finding ways to reduce noise at source as well as control the impacts on their staff. This is evidenced by the questions we often get asked, including “How do we measure noise?”, “What do we need to measure?” and “How do I know who’s affected?”.
Hopefully, we can shed some light on these with our simple 5 step guide for controlling noise in the workplace.
Step 1: identify hazards
Firstly, you need to find out whether there are any noise hazards within your workplace. This can be achieved through a combination of your knowledge of work practices, making straightforward observations and taking some simple noise measurements in areas you suspect may present a risk.
Step 2: identify who is at risk
Having found out which areas may be hazardous; you need to identify any and all employees who could be at risk of overexposure to noise. Evaluate how harm may occur, for instance damage to hearing, deafness, tinnitus, impaired communication and inability to hear audible alarms.
Also, take into consideration susceptible employees or those that already have an existing hearing condition.
Step 3: assess noise
Talk with the employees to find out their typical work routine. You then have a choice of measurement methods using either a sound level meter or noise dosimeter.
Noise levels that are over 80dB for a length of time have the capacity to damage our hearing causing Noise-Induced Hearing Loss, Tinnitus and other effects. We measure both A-weighted sound (a weighting that is added to mimic the human ear) and C-weighted (the weighting that helps us understand peak levels of noise – C-Peak) in decibels (dB).
For noise at work, we might be interested in how noisy a piece of machinery is or a process, and we are concerned with finding out the overall noise exposure of an individual during their working day/shift or week. This is the LEP,d (daily exposure) or LEP,w (weekly).
Noise Dosimeters
Noise dosimeters should be used when you want to find out the direct noise exposure of an employee. Normally they are small cable-free shoulder worn devices that measure noise right at the worker's ear, in other words, the actual noise affecting the worker. They measure both the LAeq and LCPeak values as well as calculating daily exposure levels (LEP,d). This method is particularly effective for workers with unpredictable shift patterns, those constantly on the move, or people working in confined or difficult to access areas.
Sound Level Meters
While a dosimeter is perfect for personal noise measurements there are some measurements where a sound level meter is required, this includes where a detailed series of individual noise measurements is needed. This might include where you need to know the overall noise level of a task or of a piece of machinery.
For compliant noise at work measurements the legislation stipulates that you need at least a Class 2 Integrating Averaging meter that meets IEC 61672-1:2002 to give you the data you need. These meters give you the A-weighted average noise levels (LAeq) as well as LCPeak, predicted exposure and more.
Whether you use a noise dosemeter or sound level meter, what you are trying to identify is whether any employees are exposed to noise at or above the Action Values.
If you find the overall level of noise is over 85dB(A), some form for hearing protection must be provided to bring the noise level at the ear below this. Your meter should help you choose the correct level of protection either by the HML method or by analysing the frequency content of the noise using octave band filters.
Often forgotten is the necessity to assess the risk from any impulsive noise (sudden very loud bangs and crashes) which is done by making a ‘C’ weighted Peak measurement (LCpeak). The action levels for impulsive noise are 135dB(C) and 137dB(C) respectively with the legal limit being 140dB(C).
Noise Control Action Plan
Having made and evaluated your measurements, a Noise Control Action Plan is required. This plan is the most important part of the whole survey process and should demonstrate that you are taking the necessary steps to control the identified risks. Once an action level has been reached, a corresponding set of actions need to be implemented.
Your plan should include a list of prioritised actions to solve immediate risks and to give consideration to your general duty to reduce noise levels in the workplace.
Where noise can’t be reduced at source, suitable hearing protection is required which must be made available to all workers at risk. Arrangements must be made to provide information, instruction and training to both management and workforce with respect to the risks and how to minimise and control them.
For any levels where exposures of 85dB or above are likely, a programme of health surveillance must be introduced to monitor the hearing condition of the employees involved.
Step 4: report
All your findings should be used to create a clear report which should be in a style and format that could be easily referenced in the future. This will provide permanent evidence of the decisions you have taken to comply with the law.
- Document findings of survey (including noise measurements)
- Identify extent of Noise Hazard Areas
- Details of placement of warning signs
- Prescription of suitable hearing protection where required
- Details of Education / Training program for the workforce
- ‘Buy Quiet’ purchasing policy
- Health Surveillance records
- Company Noise Policy
- The prioritised measures to be taken to control noise levels themselves rather than reliance on PPE.
- Engineering solutions, enclosures, breaking noise transmission paths, use of absorptive materials etc.
Step 5: review
The effectiveness of your noise control programme should be regularly reviewed. This will be necessary if new equipment has been introduced or there have been changes to the ‘shop floor’ layout or working hours.
For those companies with workers receiving exposures of 85dB(A) or above, your health surveillance programme should highlight any workers whose hearing deteriorates due to inadequacies in your noise control programme.
Further help
Pulsar Instruments can offer help and advice regarding noise measurement equipment, measurement know-how as well as practical advice. A variety of high-quality competency courses are regularly presented by organisations such as IOSH and the Institute of Acoustics. Shorter focused one day courses are available for those wishing to get a solid introduction to noise risk assessments or to reinforce or revise their existing skills.
For those requiring more in-depth support, please contact Pulsar Instruments.
Laura Jenkins is marketing manager at Pulsar Instruments. Fore more information, www.pulsarinstruments.com
- Safe teaching
- Great value, compliant sound level meters (from £300)
- Save up to 30% on a new sound meter
- Learn to measure noise in a day
- Save up to 30% on a new sound meter
- Intuitive design
- Aiding noise compliance
- e-shop for noise measurement
- New Pulsar Noise Awareness Courses increase understanding of measurement and control of noise in the workplace
- Noise awareness courses