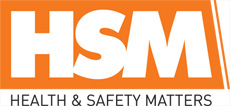
![]() |
Mark Sennett
Managing Editor |
![]() |
Kelly Rose
Editor |
Home> | Industry Update | >Company News | >Step forward with confidence |
Home> | PPE | >Safety Footwear | >Step forward with confidence |
Step forward with confidence
07 February 2024
Knowing the important elements to consider when selecting safety footwear for your workforce will help save you time, money, workforce absenteeism and also help the environment. Here, Oli Willson helps you navigate your way through footwear procurement.

THE FIRST step to decide if your workforce needs safety or industrial footwear is to carry out a risk assessment. This is a legal requirement of any employer. There are two distinct regulations to be aware of here. The Health and Safety Executive (HSE), Health and Safety at Work Regulations 1999, which outlines the general duties of employers and employees regarding health and safe at work. The second, Personal Protective Equipment at Work regulations 1992 (PPER 1992) which concerns the actual provision and use of PPE at work.
It’s worth flagging up that the PPER 1992 regulation was extended in April 2022 to also include PPE provision to casual and/ or contract employees who were not covered previously in the PPER 1992.
In general, a footwear risk assessment will consider such things as the work being carried out, the environment in which it is conducted and the end user. Potential hazards that might be identified include wet conditions, metal and chemical splash, extreme temperatures, slips, trips, or falls, punctures or cuts, falling objects, electrostatic build-up and outdoor or indoor use. The minimum an employer must do is identify what could cause illness or injury. After this, assess the risk of how likely someone could be harmed and how seriously. Finally, take action to eliminate the hazard or if this isn’t possible then to control that risk.
Once a risk assessment has been carried out this will provide a clear framework and understanding of the potential hazards you will need to protect your workforce against and also the appropriate safety footwear that is needed. Slips, trips and falls are a key hazard in the workplace, so if these are identified risks in your assessment then you might be required to review the flooring and you will also be required to provide employees with slip-resistant shoes or boots.
Risk assessment templates can be easily found on websites of health and safety governing bodies and associations, such as HSE or British Safety Industry Federation (BSIF).
Safety footwear – comfort and design
Many factors come into play when the selection of safety footwear is considered. You might be surprised to learn that there are constant innovations and developments in footwear components, laminates, design and manufacture with the aim of enhancing the wellbeing, safety and health of the end user, and with consideration to sustainability and the environment.
The good news here is the concept of hard on feet, difficult to break in and heavy and sweaty safety footwear is quickly becoming outdated. Safety footwear today combines PPE with fit, comfort and style. For example, Gore recently launched new EXTRAGUARD upper technology for GORE-TEX safety footwear that provides the end user with robust, waterproof-breathable and protective safety footwear which is permanently lightweight and comfortable from the first wear. Commercial styles are currently available in the UK from Elten, Atlas, Solid Gear and Steitz.
An average pair of adult feet typically has 250,000 sweat glands which produce approximately half a pint of perspiration per day, more in hot temperatures or during rigorous work. So, an important consideration to footwear comfort is breathability. If shoes aren’t breathable then they are likely to cause feet to become hot, cold, damp and potentially cause blisters. Plus, the extra perspiration will increase the weight of the actual shoe. A serious comfort consideration for workers who have active indoor or outdoor work requiring them to be on their feet and walk around daily.
For end users who work outdoor in all-weather environments waterproof protection from their safety footwear is essential. Conventional uppers for safety footwear become soaked, over time in a damp environment once the impregnation has been lost. This makes them heavy. Thanks to the low absorption of moisture, the re-drying time of GORE-TEX EXTRAGUARD safety footwear is minimal in comparison: the upper material allows a much faster drying time compared to work shoes with conventional uppers.
Testing to ensure quality
It’s important to consider quality when it comes to footwear selection. Durability is key here and every stage of production, manufacture and after care plays an important role to produce durable safety footwear. Procuring or purchasing cheap safety footwear is false economy because they aren’t designed to be robust or durable and will need frequent replacement. This isn’t environmentally or financially smart. Only consider purchase from manufacturing companies that ensure that all key components meet the specific quality requirements of their application, from foot beds, waterproof laminates, product technologies, through to lace eyelets, seam sealing and threads so that all elements will last for the life of the product. Established manufacturers such as Elten, one of Europe’s leading manufacturers of quality safety and work shoes, certify the quality of all products that carry their name — from understanding the conditions in which the product will be used, to utilising the latest laminates and product technologies, through to responsible manufacturing techniques and testing the final product. Check manufactures have the BSIF Trusted Supplier Shield – members offer PPE that meets the correct standards, fully complies with the regulations and is UKCA or CE marked.
Keeping up with safety standards
Once you have your risk assessment its vitally important when starting the procurement process to ensure that the boot or shoe complies with the relevant BS EN ISO Standard.
International standards are developed by International Organisation for Standardisation (ISO), European standards are developed by the European Committee for Standardisation (CEN) and the British Standards Institute (BSI) is recognised by the UK government as the national standards body and is a member of ISO. Simply put, they work in co-operation and harmony together to ensure that products, in this case footwear, are safe, reliable and of good quality. Both International and European standards are created by a wide range of stakeholders which includes consumer groups, governments and industry experts. Since regulations and standards are liable to change, due to modifications in technologies and market needs and conditions, standards are regularly reviewed and updated. Visit www.en-standard.eu and www.iso.org to keep up to date.
Three important standards to be aware of:
BS EN ISO 20345:2021: for safety footwear
BS EN ISO 20346:2021: for protective footwear, including slip resistance
BS EN ISO 20347:2021: for occupational footwear.
BS EN ISO 20345 specifies that all safety footwear must have toe protection and sets a standard of 200-joules impact-resistance (equivalent to a 20kg weight dropped 1,020mm onto the toes) and a 15KN compression test (equivalent to 1.5 tonnes resting on the toe area).
In additional to general safety footwear protection, there will be identified risks related to specific jobs. Footwear is marked with simple 1, 2 or 3 letter codes to ensure the correct product protects against a specific identified risk.
A - Antistatic
AN - Ankle protection
C – Conductive
CI - Insulation against cold
CI – Insulation against cold
CR - Cut resistant upper
E - Energy absorption
HI - Insulation against heat
HRO - Heat resistant outsole
I - Insulation against electricity
M - Metatarsal protection
SB – Toe protection
SBP – Midsole penetration protection
WR - Water resistant
WRU - Water resistant upper
Durable products for sustainability
When considering footwear purchase or procurement, we can all have a role in protecting our planet and people by reducing our environmental footprint. The single most effective way to do this is to produce or procure better, more durable products which last longer. This saves money and the planet. Check with manufacturers that any claims made regarding sustainable products are fully backed up with science based evidence. I’d advise to look out and learn about the credible accreditations such as the UK Government’s Green Claims Code (1); STANDARD 100 BY Oeko-Tex (2), OEKO-TEX STeP (3), bluesign (4), ISO14001 (5) and Higg MSI Index (6).
Ask your workforce
In addition to the legal requirements of safety and occupational footwear provision, its also worth consulting your workforce. Engaging them with wearer trials is increasingly important in these current difficult economic conditions, when price has become even more of a key factor in any purchasing decision, because it helps avoid wastage or a purchase error. When discomfort strikes the reality is workers usually switch supplied footwear over for their own footwear in a quest for comfort (which might not meet the correct protection requirements) or in some cases go out and purchase their own safety or occupational footwear from a local distributor.
Safety and occupational footwear procurement doesn’t need to be a mind field if you consider the points above. Keeping up to date on new product developments, new standards in safety, and considering such elements as quality, design, durability for sustainability is the right direction to help protect your employees.
References
₁ https://greenclaims.campaign.gov.uk/
₂ www.oeko-tex.com/en/our-standards/oeko-tex-standard-100
₃ www.oeko-tex.com/en/our-standards/oeko-tex-step
₅ www.iso.org/files/live/sites/isoorg/files/store/en/PUB100371.pdf
₆ https://apparelcoalition.org/higg-product-tools/
Oli Willson is professional footwear associate at GORE-TEX. For more information, visit www.gore-workwear.com
- Highly protective high visibility range
- Weather the storm
- Take a 360° virtual tour and see how Gore tests PPE
- Sporty safety shoe
- Warm climate boots
- New recycled soft GORE-TEX shell laminates for workwear
- Put to the test
- New arc rated PYRAD switch suit
- Volcano workers kitted out
- Pioneering protection in electrified industries