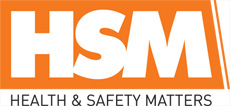
![]() |
Mark Sennett
Managing Editor |
![]() |
Kelly Rose
Editor |
Home> | PPE | >Head Protection | >Keep your head |
Keep your head
06 April 2021
As the range of head protection on the market has increased, selecting the correct helmet has become more difficult. Louise Charlton discusses the details to help you get your head around the standards and helmet selection.
INDUSTRIAL SAFETY helmets, approved to EN 397, are traditionally most commonly used. This type of product provides impact protection to the crown area. Additionally, the standard includes options such as resistance to lateral deformation, against a risk of crushing, molten metal resistance, and 440V electrical insulation. Originally published in 1995, the performance requirements remain largely unchanged since.
Trends toward higher energy impact and side protection have seen growing numbers of customers specifying mountaineering helmets, conforming to EN 12492. These helmets provide crown impact protection up to 100J, plus side, front, and rear impact tested to 25J, compared to 50J crown-only required by the industrial standard.
While EN 12492 provides all-round protection at higher energy, it lacks key performance requirements necessary for safe use in construction and industry. Important optional clauses contained within EN 397 that are not covered by EN 12492 include electrical insulation, lateral deformation, and molten metal resistance. It is often necessary to select a helmet which meets a number of these standards to offer the right protection.
An additional electrical protection specification complicates matters further. EN 50365 is a complementary standard for increased electrical insulation up to 1000V, which can only be applied alongside two main helmet standards: EN 397, industrial safety helmets, or EN 443, helmets for firefighting. This means that, although they can pass the testing requirements, EN 12492 helmets cannot fully conform to EN 50365.
A need for increased shock absorption and increased electrical protection meant both EN 12492 and EN 50365 began to be specified, posing a problem for helmet manufacturers.
Due to their respective applications, industrial safety helmets and mountaineering helmets feature distinctly different retention systems. An EN 397 chinstrap mechanism must release under a force of 150-250N, allowing the helmet to be quickly removed, to prevent the wearer becoming caught in machinery. In an EN 12492 helmet, however, the chinstrap must not release or stretch when a force of 500N is gradually applied and held for 120 seconds, to ensure it will remain securely on the head in the event of multiple falling objects. The required action of each retention system rendered the two types incompatible, with one helmet unable to perform both jobs.
New products have been designed to meet both standards, plus EN 50365, which was initially only achievable with two different harnesses used in one helmet shell. Though a step forward, these types of products required tools, which is not always practical, and can also cause concern over correct fitting. Following advances in design, helmets offering full protection and conformity to both standards with a single harness are now available, enabling quick selection of retention system function via a switch on the chinstrap.
Confusion over the status of EN 812 bump caps brings added complexity. This close-fitting baseball style cap is intended for protection against bumps and scrapes from static objects, tested with an impact energy of 12J. Unlike helmets designed to reduce the impact of falling or projected objects, bump caps are designed to protect the wearer where there is a risk of colliding with stationary hazards, such as pipes or a low ceiling. An effective way to remember their purpose is to remember that bump caps ‘protect the wearer against themselves’. Despite critical differences in design and protection level, misleading information continues to describe EN 812 as a helmet standard. It is important to understand that ‘head protection’ does not equal ‘safety helmets’, and remember that when selecting a product.
On the other end of the scale are EN 14052 helmets intended for use in high-risk environments, such as demolition and quarrying. These products are tested with 50J impact energy on the side, front, and rear – double that in EN 12492 – and 100J on the crown. While it may appear easier to select this high-performance product than to spend time working out the other options, it is important to remember that all helmet types have drawbacks. EN 14052 helmets used on low-rise construction sites will provide some protection against the risks encountered but other considerations mean they may not be the best option.
Cost is one distinction. EN 397 helmets can be purchased fairly cheaply in DIY stores but EN 14052 helmets are more specialist, with additional parts and enhanced materials. A high-performance helmet can therefore set you back over twice the price of the traditional industrial option.
Selecting an EN 14052 helmet for general use can in fact jeopardise safety. PPE is designed to be as lightweight and comfortable as possible, but heavy-duty products can be heavier and more cumbersome. Generally available EN 397 helmets can weigh 350-400g, whereas an EN 14052 option can come out nearer 600g before adding any accessories. The profile is also often taller than an industrial helmet, meaning reduced clearance for moving and working. Increased weight and bulk mean unsupervised wearers are more likely to remove the helmet in discomfort.
To improve wearer acceptance and reduce non-compliance, it is imperative to select the best helmet for the task and wearer rather than to simply seek out the highest performing. Comfort is an important factor for safety, as ultimately PPE only works if it is worn and maintained correctly.
In other regions, requirements for multiple helmet types are set out in a single standard. The ANSI/ISEA Z89.1 American standard establishes impact types and electrical classes for helmets, called “hard hats”. Impact types include lateral and top-only, with a “reverse wearing” option for which helmets are tested in reverse orientation, plus electrical classes go beyond the 1000V European standard, meaning this single national standard covers the equivalent requirements of EN 397, EN 12492, EN 50365, and more. Other national standards use a similar structure, including Australia and New Zealand standard AS/NZS 1801, Canadian national standard CSA Z94.1, and Chinese national standard GB 2811.
Helmets can meet multiple regional standards – for example, one helmet can conform to EN 397, ANSI/ISEA Z89.1, CSA Z94.1, AS/NZS 1801 fully with no conflicts. Global helmets are best to select as they encompass a wide range of important features and are independently tested multiple times in different ways.
Head protection standards each give specific requirements for product marking, labels, and user information. This can mean multiple information leaflets and labels must be provided, reducing the likelihood of all necessary safety information being fully read and understood. Therefore, while helmets meeting all relevant regional standards provide the best solution currently, there is room for improvement.
International standard ISO 3873 seeks to harmonise requirements globally, but in its current form, though most helmets meet the standard, it is rarely claimed or specified. Unrevised since 1977, regional standards have overtaken it with updates. ISO 3873 is currently being reviewed and updated to be re-released. The new revision should simplify selection, enabling wearers to focus on comfort and compatibility.
In addition to the correct helmet, it is important to identify compatible bolt-on products and accessories. It may seem logical to assume that two or more items fitting together means they will work together, but that is not always the case. Products must be tested and assessed in combination to ensure they can be used safely together, to achieve the correct protection levels.
Helmet-mounted eye protectors conforming to EN 166 or EN 1731 should be assessed on the helmets with which they are suitable for use. Testing is required to ensure wearing height allows the eye or faceshield to be positioned correctly, without visual distortion, and to protect against impact and other hazards effectively.
The EN 352 standards, covering hearing protection, include a dedicated standard for ear muffs attached to a safety helmet. EN 352-3 requires ear defenders to be tested on helmets they are intended for use with, ensuring that each helmet model provides the correct pressure to enable the product to perform effectively, without causing discomfort. Hearing loss is a long-latency hazard, meaning irreparable damage can go unnoticed for many years. It is therefore imperative to ensure helmet-mounted ear defenders are certified as compatible with your chosen helmet.
Head protection standards give requirements for certain accessories, including tests for chinstraps. Other accessories outside of standard requirements, such as thermal liners and neck capes, should be assessed and, where applicable, tested. This is why helmet manufacturers offer accessories and recommend selecting from their range.
When selecting compatible PPE, it is best to buy from a manufacturer offering complete above-the-neck solutions, who can provide everything required and offer advice on selecting and using their products. Making sure PPE is truly compatible before you buy ensures proper protection, as well as saving money and time.
Louise Charlton is technical specialist at JSP Ltd. For more information, visit www.jspsafety.com
- PPE, height safety & traffic management
- Mask available in 3 sizes
- JSP launches new premium range of PPE
- JSP celebrates 60 years of manufacturing for safety
- Staying ahead
- Head protection range evolves
- JSP licenses eyewear brand
- JSP - Leading Manufacturer of ‘above the neck’ PPE
- Keep ahead
- Working in harmony