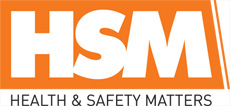
![]() |
Mark Sennett
Managing Editor |
![]() |
Kelly Rose
Editor |
Home> | PPE | >Ear Protection | >Hear tomorrow |
Hear tomorrow
12 August 2021
There's no noise on a dead planet, says Jono Heale as he provides an insight into foam verses custom hearing protection.
NOISE INDUCED hearing damage is one of the most socially disabling conditions known, particularly since the industrial revolution. It is completely avoidable and in noisy working environments, our precious sense of hearing is protected by Noise at Work legislation when suitable personal protective equipment (PPE) is mandated. With these measures in place, this nasty and irreversible condition can be prevented.
Although in the hierarchy of control measures, post a suitable and sufficient risk assessment, we find PPE near the bottom of the list, it remains crucial to provide protection that is fit for purpose, reasonably practicable and cost effective, but most importantly, worn! And therein lies the problem. User acceptance to wearing hearing protectors is low.
I’m not a fan of using the word ‘earplugs’ to describe hearing protectors. Across many sectors, there’s almost an unwillingness to wear this type of protection. The inability to hear work colleagues, warning signals or important instructions, together with the blocked-up sensation (the occlusion effect) that properly fitted disposable earplugs provide are the main reasons for this low user acceptance. It’s quite normal to see poorly fitted earplugs that users have loosened from their ears to hear better, consequently reducing the manufacturers claimed effectiveness!
So, for the person who will choose which type of hearing protection workers should wear, what priorities should they seriously consider?
First and foremost, is the hearing protection certified and compliant to BS EN 352-2, PPE Regulation (EU) 2016/425 and latterly UKCA? The relatively recent legislation moved hearing protection from a category II PPE product into a Category III PPE product and exclusively includes the risk that harmful noise may cause very serious consequences such as irreversible damage to heath. At last, we see some sense in legislation for the hearing protection equipment (HPE) sector. Oh, and if employees are wearing custom hearing protectors, make sure that the company that makes them is either Module D or Module C compliant in their manufacturing and testing standards. I’m proud to say ACS was one of the first custom hearing protection companies in the UK to become fully compliant to the new regulation. Unfortunately, there are still some non-compliant manufacturers who are placing their products into the market, causing the specialist HSE departments some concern. The major problem is to how to ‘police’ this sector, and with the aid of the BSiF surveillance service, exposing these non-conforming manufacturers and calling them into account is in hand.
Secondly, but as important, it must be about reducing to safe levels the sound pressure level (SPL) at the ear compared with the exposure time. SPL is measured in decibels (dB) as a convenient way of expressing a logarithmic pattern of increased sound intensity. Each time there is an increase of 3dB, the sound pressure is doubled and is in fact twice as loud. If it’s twice as loud you should half your exposure time. Simple! All certified and compliant hearing protection have different levels of sound reduction (attenuation), which has been tested to guarantee the protection required and denoted as a SNR (single number rating) number. One important factor is to find the right level of attenuation that will protect the user during their given working time. Another important issue is to find the right level of attenuation that enables the worker to do the job they are doing and, in some cases, still maintain a level of communication whilst being suitably projected and fit for purpose.
There are many different types of hearing protectors on the market. Earmuffs/defenders are simple and very effective, however, may interfere with head gear or face masks and effect communication unless a more expensive ‘active’ electronic system is incorporated.
Custom hearing protection immediately presents an initial investment and bespoke fitting issue, which should be completed by a certified and trained technician. However, the seal integrity and therefore the correct level of protection can be guaranteed with custom; various working environments can be catered for together with a suitable and sufficient passive level of attenuation to maintain communication and awareness in hazardous situations. Medical grade soft silicone hearing protection is best as they are more comfortable and flex within the wearers ear canal when speaking or eating to maintain a good fit. Custom can also have a wide range of applications through a variety of interchangeable sound reducing filters to suit the noisy environment and the wearer’s communication needs. However, the cartilage of the ear continues to slowly grow and change shape as you age, therefore it is recommended that custom hearing protection should be regularly fit tested or remade approximately every four years.
With single use foam hearing protection, first thoughts may present a super cheap and easy solution but with little thought of hidden issues including: - contamination in application, correct application and guarantee of the required level of protection, detrimental to communication and……… disposal.
Let’s just stop here! Disposal?
Would you also seriously consider the environmental impact when choosing any PPE let alone ‘earplugs’? (There, I’ve said earplugs). Single-use Foam Earplugs are contributing to one of the biggest environmental problems this decade. When you look a little more closely into the figures the facts can be quite disturbing.
According to many environmental publications including Earth.Org, National Geographic and science journal Nature, in the 1950’s humans produced more than 2 million tons of plastic per year. This annual production increased to 419 million tons in 2015. Nature has reported that currently 11 million tons of plastic waste finds its way into our oceans. If micro plastics are included the total amount could increase to a further 29 million tons by 2040. The National Geographic found that over 90% of all plastic ever made is not recycled, which presents not only one of the biggest environment problems of our lives, but another shocking and huge market failure. Oh, and some plastics can take 400 years to decompose!
Millions of workers use and throw away foam polyurethane earplugs every single day in the quest to protect their hearing. However, although great (if fitted correctly) for that person’s hearing health these single use foam earplugs become a future health hazard for our children’s environment and planet Earth. Apparently, in manufacturing, construction and even motorsport industries foam earplugs are still the most common type of hearing protection used in the world today. Unfortunately, surprise -surprise, billions of these foam earplugs end up in landfill sites and even our waterways and oceans. Polyurethane foam earplugs are not biodegradable and in landfills they can possibly leach out into water tables. To be fair some polyurethane products can be recycled into other items but inevitably in all ends up as waste. Also, worth noting that they are made from petroleum-based resources and chemical elements in polyurethane do not degrade. So, an option could be to incinerate, but this of course releases toxic chemicals and the dreaded CO2.
Research conducted by marine conservationist Marcus Erikson has concluded that over 92% of all plastic material polluting the world’s oceans, most of this was synthetic polymer foams. Scary facts indeed. Although polyurethanes have solved many industrial related problems since the 1930s, Dr Otto Bayer may now be turning in his grave?
Let’s do some figures! Let’s consider 250 workers, working an average 240-day year, using 3 pairs of disposable foam earplugs each day. One foam earplug weighs around 1 gram, so every year the company will contribute 360,000 earplugs to landfill at a weight of 36kg. With an estimated cost of 5p per individual plug the annual spend would be £18,000 per year and over a four-year period (the average life of one pair of custom earplugs) £72,000. Now, here’s the scary bit: that would equate to 1,440,000 non-recyclable earplugs weighing in at a staggering 144kg! Multiply this by thousands of sites across the world and the issue should warrant serious attention in the PPE and health and safety community.
If we then compare this example to custom moulded hearing protection, at an average weight of 2.5g per plug, over the same 4-year period only 1.25kg of waste goes to landfill or to be recycled, and at an average total spend of £21,500, the company saves £50,500 over the cost of disposable earplugs! There we have it. Not only do single use earplugs cost more in the long run they are also costing the Planet! It is a false economy.
As we well know the best protection is the protection that’s worn. However, in these times the future consideration of whether the PPE manufacturer has a developing environmental policy and what its CO2 emissions are, may also be an ethical purchasing factor. Ultimately, we want our employees to work safe now so they can still hear tomorrow, but if we can also do this ethically and in a more environmental and user-friendly way, then planet Earth will still be heretomorrow!
Jono Heale is director at ACS Custom. For more information, visit www.acscustom.com
- PPE buyers urged to Check-Select-Protect
- Company fined after contractor falls from height
- Experts start a new chapter with book for retailers
- New sentencing guidelines introduced for corporate manslaughter, health and safety and food safety
- Nanofibres may pose health risk
- Practitioner viewpoint - October 22
- Inadequate health and safety practice led to injury
- Unite raises construction death rise concerns
- BA fined after employee crushed in vehicle collision
- Stressful legal matters damaging mental health