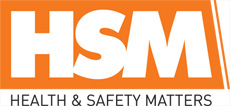
![]() |
Mark Sennett
Managing Editor |
![]() |
Kelly Rose
Editor |
Home> | Breathing Safely | >Gas Detection and Monitoring | >Safety in explosive atmospheres |
Safety in explosive atmospheres
25 July 2017
Manufacturer Witton Chemicals had a critical decision to make when selecting forklift trucks operating in Zone 2 hazardous areas, as standard trucks would be a source of an ignition in the event of a flammable gas or vapour release.
“As a contract chemical manufacturer for blue chip companies, Witton provides a flexible and responsive service,” says Steve Owen, operations manager for Witton Chemicals. “Our operations are highly productive with a quick turnaround, supporting a wide range of international customers including some of the largest adhesive, electronic, paint, sealant, petrochemical and pharmaceutical companies worldwide.”
“The diversity of our work means that we handle many different raw materials, many of which are highly flammable,” says Steve. “Operating as a COMAH* site, safety is our number one priority, and ATEX** and DSEAR*** regulations are central to our operation.”
At the plant in Suffolk, UK, raw materials are mainly handled in liquid form, stored in sealed drums, IBCs and in bulk, with chemical process operators using forklift trucks to transport materials in the production areas. Over 40 employees work on a 24-hour shift basis at the site and the company operates a four day week, a business strategy that has been proven to be more efficient, allowing for growing capacity should its customers really need it.
“All of our production runs are customer specific and can be up to a thousand tonnes, so reliability of the forklift trucks is critical,” insists Steve. “The reactors must be fed at exactly the right time with the right materials, otherwise whole batches of product can be ruined.”
The production areas where the forklifts operate at Witton Chemicals have been classified as Zone 2 hazardous areas which require specially adapted, ATEX 2014/34/EU compliant forklift trucks. Standard forklifts would otherwise be a source of an ignition in the event of a flammable gas or vapour release. Excess heat from the engine, motors, brakes and other components, a spark from unprotected electrical equipment or even a spark from static build up on the truck could create enough energy to cause an explosion.
To meet Witton’s handling needs, two new Doosan D25S-5 diesel forklifts were converted by explosion protection safety company Pyroban for Zone 2 (category 3G) operation. Supplied through Windsor Materials Handling, the trucks feature Pyroban’s system6000 which incorporates gas detection to continuously monitor the direct environment around each truck. In the event of a vapour release, it will alert the driver and automatically shut the trucks down where necessary, eliminating the risk of an explosion.
The Pyroban conversions also featured restricted breathing enclosures, stainless steel cladding of forks and surface temperature cooling to ensure the engine, motors, brakes, electrics and other components remain below the auto-ignition temperatures of flammable materials.
“Since we started using forklift trucks, we’ve worked with Pyroban,” says Steve, explaining that Witton Chemicals has been at the site since the 1970s. “The current arrangement is the best we have ever had. It seems like the Pyroban system is totally integrated into the forklift truck and keeping us all safe each day.”
“The benefit of the Doosan trucks on a site like this is the simplicity of design, which works very well with the Pyroban system and conversion process,” says Josh Newton, Sales Manager, from Windsor Materials Handling. “They are solid and reliable trucks, which has been proven over the last year. To cover every eventuality in this time sensitive production line, we also have a backup Zone 2 converted truck available to Witton.”
Inevitable wear and tear on forklift trucks operating in potentially explosive atmospheres can pose a safety risk. To counteract this, Windsor Materials Handling has established a system of preventative maintenance to ensure the equipment continues to be safe, and trucks are regularly serviced by an engineer trained to work on the Pyroban system.
In line with EN60079-17 and ATEX 1999/92/EC Witton Chemicals also instructed Pyroban to perform its annual safety audit (Ex-ASA) to ensure that the integrity and safety of the trucks were not compromised during the first year.
- Solution for Zone 2 hazardous areas
- Explosion protected forklifts
- Update training for Ex-forklift engineers
- Platforms that cause explosions
- EU emissions regulations prioritise safety
- Explosion-proof package
- How to specify an explosion proof forklift in seven steps
- Static analysis
- Reducing explosion risk
- Coatings firm uses protected tugs