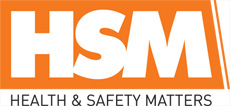
![]() |
Mark Sennett
Managing Editor |
![]() |
Kelly Rose
Editor |
Home> | Health & Wellbeing | >Employee Assistance | >MSDs: Food for thought |
Home> | Health & Wellbeing | >General Health & Wellbeing | >MSDs: Food for thought |
Home> | Handling & Storing | >Safer Manual Handling | >MSDs: Food for thought |
MSDs: Food for thought
06 April 2016
More than a quarter of the reported cases of musculoskeletal disorders (MSDs) in UK manufacturing last year occurred in the food and drink industry. Paul Fenner, of the Institution of Occupational Safety and Health’s (IOSH) Food and Drink Group, highlights some of the work being done within the industry to address the issue.
Around 325,000 people are employed in food and drink manufacturing in the UK, accounting for 13% of our total manufacturing workforce.
A high number carry out manual handling tasks with repetitive movements, or intricate work that has the potential to impact on their health.
HSE statistics show that in 2013/14 and 2014/15, the food and drink sector was responsible for 28% and 26% respectively of the total number of RIDDOR reports made across all forms of manufacturing. Over 13% of all food and drink sector RIDDORs are attributable to MSDs.
In the past I have found that the prevention and management of MSDs has been seen as being too difficult to resolve. Thankfully, more and more companies are realising that investing in their workers’ health is good for both employees and their business.
Good practice
The IOSH Food and Drink Group believes there is a real passion and drive within the industry to improve safety and to cater for the health and wellbeing of workers too.
Through our annual awards we’ve seen companies eliminate hazards and control risks using ideas that have come from both up high, or stemmed from those on the shop floor.
Greencore Food to Go’s Park Royal factory in London, for example, invested in a partnership with a conveyor manufacturer to develop and install a new conveyor system on its ten dispatch lines in order to remove the risk of its staff suffering health problems associated with twisting and overstretching.
It came in response to the factory having experienced a 25% increase in its workload since being awarded a new contract with a customer.
Senior managers were concerned that this increase could have a direct impact on the health and wellbeing of those working on the dispatch packing line, and therefore set about eradicating the risk of MSDs at the design stage.
Not every improvement, however, has required major investment or ground-breaking thought to make a difference.
Employees at Greencore Grocery Hull were reporting cases of back strain as a result of moving tote bins weighing up to 200kg when filled with butter cream around the factory floor.
A handle was designed to attach to the bins to make them easier to move around. In the process it has removed the stooping risk factor, and therefore the risk of people suffering lower back pain, all at a cost of around £3000.
Engineers at Green Isle Foods also came up with a simple solution to eliminate a significant hazard at its pizza factory in Co Longford, Ireland. They had spotted that workers were lifting heavy equipment at height whenever the positioners were used to place dough balls correctly, putting them at considerable risk of developing MSDs.
An engineering solution was therefore developed that limited the risk of causing manual handling injuries, with staff and management working together as a team to implement a safer and more efficient process.
Not all solutions, however, are immediately seen as being good for business.
In my own organisation for instance, we have made an improvement to tackle MSDs on a prawn de-shelling line - one which at first glance seemed counter-intuitive to boosting efficiency and improving yields.
We simply etched boxes on the conveyor for the shelled prawns to be placed in a straight line and in the right orientation, rather that placing them anywhere on the conveyor. The result was that we were able to slow down the conveyor and reduce the number of people at this point on the line, and still achieve an increase in throughput and yield. We used the HSE’s Assessment of Repetitive Tasks (ART) tool to assess its success, and it showed we had reduced MSD risk by doing this.
The future
In conclusion, I feel that in order to improve the situation and drive reductions in MSD risk, RIDDOR incidents and better manage employee health, we all need to educate our organisations on the importance of the ‘health agenda’, and particularly the value that will create for every organisation in the food and drink sector. We need to integrate the assessment and management of MSDs into our organisations, from planning and developing new production lines/techniques and designing in MSD risk reduction, to the occupational health programmes we use when our employees develop an MSD problem.
- Occupational hazards - December 2021
- Occupational hazards - March 24
- Occupational hazards - May 2022
- Competition launched to praise small business health and safety
- A change of perspective
- Occupational hazards - August 2021
- “Landmark day” as ISO 45001 is launched
- Occupational hazards - October 2021
- Occupational hazards - June 2021
- Occupational health and wellbeing 'wake-up' call needed
- BSIF: Covid-19 Update
- Dust tight
- SAFEContractor for 5th year
- BSC welcomes proposals to slash legal costs in personal injury claims
- Get some insight
- Asbestos remains number one killer
- Chemical exposure course goes more than skin deep
- Airlines urged to look at manual handling training
- Getting workers involved in safety
- Dual drug testing