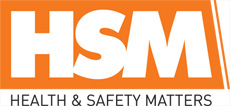
![]() |
Mark Sennett
Managing Editor |
![]() |
Kelly Rose
Editor |
Home> | Health & Wellbeing | >General Health & Wellbeing | >Unacceptable statistics in the manufacturing sector |
Unacceptable statistics in the manufacturing sector
14 October 2015
On average two workers are injured every day in the manufacturing sector. That means in the last year alone 784 people were injured, with the majority (465) involving moving machinery. Bryan Richards, managing partner and chartered safety and health practitioner at Arinite says that for an industry that directly employs 8.5% of the workforce and 15% of the UK’s gross domestic product this is unacceptable, and expensive: 4.7 million working days were lost in 2013/2014 due to injury. So what can b
Deterrence, by means of fines and convictions, is one way to force the industry to change. According to data from health & safety consultants, the HSE has convicted an average of 141 companies in the manufacturing sector per year since 2009, with an average fine of £31,277. However, this is not a real solution to improving safety in the workplace: the damage has already been done; the workers have already been injured. The problem needs to be stopped at its source, so we need to identify the risks before they can cause damage.
Risk management
Recently a saw mill in Kettering was fined £5000 after an agency worker’s left hand was drawn into the blade. His injuries were so severe that he required plastic surgery. It was later found out that the company had failed to take measures to prevent access to dangerous parts of the saw. It should be clear that the company had not properly risk assessed this piece of machinery, and in doing so a worker had paid the price. So let’s use this as an example of how not to do things and as a test-case of how this could have been prevented.
The first step in any risk assessment is to identify the potential hazards in your workplace. Walking around and surveying your place of work is a good first step, and as you do so ask yourself these questions:
- Have I followed the manufacturer’s instructions on the proper means of storage and operation of equipment and chemicals?
- Have I experienced problems before that led to accidents and ill-health?
- Have I taken proper measures to minimize the scenarios that can harm health in the long term e.g. high noise levels or dangerous substances?
For this case the worker was feeding material into the saw when he slipped and his left hand was drawn into the blade. It is clear then that the operator should not be in a position where such an incident can occur. The risk in this case is the injuries that can happen with the moving machinery of the saw blade.
The next step is to identify those at risk. Again it is a good start to ask your employees as to what they think they are and how they would themselves deal with it. They might see something that you overlooked.
In the case of the saw mill worker it seems they were hired by an agency. This means that they would be less familiar with equipment compared to normal employees, and so would be more at risk. It is therefore important, in terms of agency and new workers, to provide the proper training in order so that they can safely carry out their work.
Then what you have to do next is to decide the likelihood of that something harmful can occur and what you should do about it. Generally speaking your action should be proportional to the risk, e.g. wearing more safety equipment than is necessary or economical for the job would not be optimal.
Now in the case of the saw-mill a wooden box was installed so that workers could not stand close to the saw, therefore preventing access to the hazard.
In this case the employer did not appear to carry out a risk assessment which identified effective risk control measures for using the saw. This was highlighted by the employer installing additional protective measures after the accident occurred.
When you’ve looked at and identified sources of risk and what to do about them it is important to record your findings by writing them down (you don’t have to if you have fewer than five employees) as it is required by law. It’s not necessary to write an essay on your findings, a short sentence is often the only thing that’s needed eg: 'Danger from moving saw blade: install box to prevent worker from getting too close'. If you have a workplace that frequently changes location, for example the construction industry, then focus on the more general risks that may occur in that field.
Brigstock saw mill was fined £5000 with additional charges because it did not adequately risk assess its site, and consequently a worker was harmed for their negligence. This did not have to happen, it could have been prevented and avoided a heavy fine if they just identified the saw blade as the danger it obviously is and made the easy steps to stop it.
- England's World Cup exit good for the nation's health
- Producers of The Walking Dead hit with maximum fine
- Charitable trust and contractor fined for asbestos safety failings
- Older workers less accident prone
- Food for thought
- 1974 Act 40th anniversary
- Mordaunt remains health and safety minister
- Rugby legend Rory Underwood to speak at Health & Safety Event
- Firm prosecuted following the avoidable death of a roof worker
- Contractor receives suspended prison sentence after worker seriously injured
- BSIF: Covid-19 Update
- Dust tight
- SAFEContractor for 5th year
- BSC welcomes proposals to slash legal costs in personal injury claims
- Get some insight
- Asbestos remains number one killer
- Chemical exposure course goes more than skin deep
- Getting workers involved in safety
- Dual drug testing
- On-site health screening