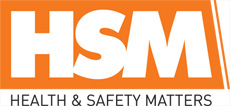
![]() |
Mark Sennett
Managing Editor |
![]() |
Kelly Rose
Editor |
Home> | Slips, Trips & Falls | >Fall Prevention | >High risk |
Home> | Slips, Trips & Falls | >Fall Protection | >High risk |
High risk
17 February 2023
Falls from height are once again the leading cause of fatalities, according to the Health & Safety Executive’s latest statistics. What can the construction sector do to change this? Ruth Armstrong and Kate Oliver explore the options.

FATALITIES ACROSS different industries are, unfortunately, nothing new, but it’s only recently that construction has started to see the highest rates. In 2020/21, the construction industry became the leading industry for deaths at work for the first time in living memory – a trend that continued into 21/22, when construction accounted for a quarter of the 123 work-related fatalities reported. This represents a fatal injury rate that is four times as high as the average across all industries. What’s more, according to the Health & Safety Executive (HSE), falls from height are consistently the leading cause of fatalities, accounting for 39 deaths in 2020/21 and 29 in 2020/21.
The definition of falling from height is broad and is most frequently associated with ladders, due to their perceived instability (and even illegality). However, such incidents also involve vehicles, platforms, stairs, roofs, scaffolding, racking, and skylights. A fall from height can also be from any height. The causes are also varied, but a common thread across most is a risk assessment that has failed to evaluate and remove, mitigate, or reduce the potential dangers of work from height.
It’s likely that falls from height will be a focus for the HSE, particularly in the wake of its latest statistics. In Birmingham, where our head office is based, surprise spot checks by the HSE are already more pronounced and frequent.
A closer look at risk assessments
Working from height carries inherent risk, but these can be reduced or mitigated with careful planning. As mentioned before, it is insufficient, or a lack of, risk assessments that most frequently lead to avoidable accidents, simply because the potential hazards have not been accounted for. Generic risk assessments – that is, ones that cover the basics but do not take account of a site’s specific context and activities – are a particular concern for the HSE.
If an unexpected visit by the HSE results in a Prohibition or Stop Notice, fine or prosecution, however, that means that the costs and timescales of projects are likely to rapidly increase. Investing time in evaluating and updating risk assessments, therefore, is an investment – not just in efficiency and cost-effectiveness – but also the health, safety, and welfare of a site’s most valuable assets – its workforce.
Where to start
A risk assessment and method statement (RAMS) is not a pretty folder that is only whipped out when the HSE comes calling - it’s a living document that everyone on site should be aware of and engage with. It also influences all aspects of your site – from PPE to layout. It is vital that you review your RAMS to make sure they are all still relevant, site specific and properly match the risk and method identified. Has your team dynamic changed, for example? Are there any skills gaps? Have you had to add / change equipment to meet new project deadlines? Have there been significant changes to the site or its surroundings?
A two-year-old risk assessment, or a generic one, is useless and won’t cover you if any incidents occur. Take time to review your assessment, as well as all other documents and policies that this affects, such as training, control measures, handover documents and method statements.
Keep the HSE’s hierarchy in mind as you do this. Remember, you should prioritise removing a risk over reducing or mitigating it. Once done, re-induct your team on its findings and deliver toolbox talks, regardless of whether any major changes have been made. You should also keep records of this training.
The hierarchy for height
An example of the HSE’s hierarchy for working at height might need you to ask yourself the following questions:
Remove – Is it necessary to work from height at all? Could the work be completed on the ground, and then mechanically moved into place?
Reduce – How can you prevent falls? Is there a particular type of ladder or equipment that would be best suited for the task? Does the person undertaking it require supervision, or a specific level of competency?
Mitigate – If someone falls, how can you ensure that they are less likely to be injured? Can you use harnesses or reduce the height of the fall?
Risk assessments should also include evidence of good practice, whether that is method statements, training records, or inspections. Properly communicated, these materials help employees to understand how they can work safely and efficiently, without posing a risk to themselves or others around them.
After long breaks, it is worth taking the time to schedule refresher courses and toolbox talks, particularly for work that involves specialist PPE and equipment, such as plant and machinery.
Rules and regulations
The HSE will be on the lookout for awareness of key legislation. For working at height, this includes INDG401 and the Work at Height Regulations 2005. This can feel intimidating for some, but a wealth of information exists online to help make sense of the latest rules and regulations.
If, after perusing the guidance, updating risk assessments remains a gargantuan and daunting task, then outsourcing its review, redevelopment and dissemination may help reduce the burden of work and ensure no stone is left unturned. As well as knowledge of legislation, specialists can also use previous experience to support their analysis of certain situations, thus potentially spotting hazards that were previously missed.
Once risk assessments are refreshed, specialists can help to make sure that all of this will have a positive impact on the health and safety of a site. For example, they may stage mock inspections or stress tests to review how proposed measures play out in practice, and who on a team is (or is not!) following a site’s policies. Identifying discrepancies is vital to ensuring that everyone is embedding safe working practices across the site, regardless of whether they are a regular worker, a subcontractor, or a visitor. Whatever the findings from these mock inspections, a specialist will encourage site managers to adapt and revise risk assessments or use them as rationale for providing further training.
The HSE’s most recent statistics should encourage the industry into more proactive risk management, regardless of the nature of the site or its work. The development of new homes deserves just as much attention to safety and welfare as does the construction of a nuclear plant, which is why risk assessments should always be a priority and seen as the guiding light for safe working practices.
Working from height need not be the leading cause of fatality in construction. By examining its role within your site and asking yourself how it can be made safer – or whether it is even required at all – you are taking the first steps to improving site efficiency and build quality and ensuring every one of your employees can go home safely at the end of their shift.
Its free Crisis Response & Management App helps businesses to respond, review and manage risk. For more information, or to download the app, please visit: https://gateleyplc.com/services/risk-crisis-response/.
Ruth Armstrong and Kate Oliver are lawyers in the business defence team at Gateley Legal. For more information, visit gateleyplc.com
- Printing employee suffered crush injury
- Failures at waste and recycling centre
- Course to address cellar gas safety
- £1.1M fine following offshore gas blast
- Company lands fine after workers fall from height
- Man injured on North Sea platform
- Unite welcomes relaxation on HGV driver medicals
- MBE for BSIF member
- RoSPA launches groundbreaking ‘Falls Charity Appeal’
- Oil platform collapses injuring employee