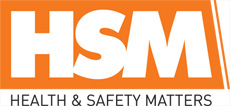
![]() |
Mark Sennett
Managing Editor |
![]() |
Kelly Rose
Editor |
The gloves are on
06 September 2024
One of the biggest challenges faced by health and safety managers is compliance, and one of the most important factors – especially when it comes to hand protection compliance – is in considering human nature. In this article, Sarah Bridge looks at the value of going ‘back to basics’.

IN TODAY’S hand protection market, the development of European performance standards is enabling health and safety managers to more readily able find the right performance gloves for the hazards their workers face.
Making sure that people wear them however is a whole different thing.
Compliance remains one of the biggest challenges for any health and safety manager and there are multiple factors involved in getting it right.
We hear it so often from safety managers - as soon as my back is turned – the gloves are off – literally!!
What we are dealing with here is the challenge of human nature and its impact on PPE compliance. The ultimate goal for us at Unigloves is to provide gloves that people forget they are wearing.
And when you get fit, feel, comfort and sizing right (combined with appropriate protection performance) you will fundamentally increase your chances of worker compliance. But how do you achieve that?
It’s a matter of going back to basics. Building worker-driven considerations into the PPE selection process.
Where the risks are clearer and higher by nature – consider people working with strong chemical solutions capable of immediately damaging the skin significantly - compliance levels are generally higher. If people understand there is a grave risk of harm or instant risk of harm there is a clearer understanding of the seriousness of the hazard and a greater willingness to use the protection provided.
So, compliance challenges can often be felt most in what can be seen as middle risk environments. For example, building sites where hand protection risks exist but they can be seen by workers as not likely to cause a sudden and extreme hand injury.
In these types of environments there is a temptation for workers to take their gloves off – especially if they are uncomfortable in any way - because they don’t perceive the risks as posing immediate danger and the discomfort outweighs the perceived hazard.
So, some relatively simple yet critical considerations can make a real difference to compliance. We are not talking about complex, technical knowledge – we are talking about getting the foundations right first by thinking of the human impact.
It is important to focus on:
- Fit
- Feel
- Comfort
- Size
Aligned to - of course – the right levels of protection performance.
Consider appropriate proportions for men and women – by nature their palm size and finger length is different so this needs to be woven into the PPE thinking to reflect physiological differences.
There are fabulously technical gloves out there but if people avoid wearing them because the gloves are uncomfortable, because their hands sweat, because the gloves are too big or too tight then the performance benefits are going to be negated and risk is increased.
These may seem obvious and simple considerations but the reality is they work together to increase compliance but are too often overlooked.
How many people in the organisation truly knows their hand size? If workers don’t, they are more likely to wear something they think might be the right fit from the stores or if the right size isn’t in stock, they will automatically be wearing something inadequate. Wrong gloves sizing increases the risk of non-compliance.
Think about something as simple as the growing emergence of touch screens in the workplace. If someone is wearing gloves that are too big or don’t fit properly, it could hamper their ability to use the touch screen. If the touch screen is an important part of the job, the worker is much more likely to remove the glove it as it is negatively impacting their ability to get the job done.
Make a big difference
As an example of this approach, sweating hands – doesn’t sound too bad – but is a major reason why people take their gloves off.
Glove breathability is critical but where perhaps there is an unsupported glove with no built-in liner, for example a chemical protective glove, our advice would be to provide a pair of cotton liners to wear underneath helping remove the issues and increasing compliance.
We are talking about human beings and feelings. If something feels uncomfortable, we are highly likely to avoid the thing that is uncomfortable. And that often means taking gloves off.
So don’t underestimate the power of fit, feel, comfort and size.
Involve the workforce
Including the workforce in the hand selection process is likely to be reflected in higher compliance levels. They are much more likely to have a connection and understanding of why they are being asked to use hand protection.
Undertake trials that focus not just on performance. The workforce that feels they are being considered, involved and listened to in the hand protection process is much more likely to comply. It is often about perceived value. It is not just about the best protection – it really is about comfort. The safety manager who listens to their workers and allows them into the process will more likely be rewarded in increased compliance.
It is helpful to present options and encourage choice from the workforce. Force people to do something, to wear something mandated, something they have not been invested in and most will push back. It’s human nature.
We have such great performing products – so the focus should be about compliance and it’s about hearts and minds. And our experience is that from a glove selection process, hearts and minds are often won through worker involvement.
Understanding cut resistance rerformance
There is confusion around the cut resistance performance test ratings and what they mean and how they apply to workplace hazards.
Some of the things we hear from safety managers is: Why are there so many levels and how can we use them practically? For example, at what point does a level C need to be replaced by a level D?
It is not straightforward.
There is a trend we have seen within the industry for safety managers to default to the highest levels of protection they can, almost as a way of de-risking their exposure and ensuring a workers’ hands are safe. You can understand the strategy.
In recent years under EN388 we have had testing and cut resistance performance scores from 1-4, then we added 5 and now it has developed to provide performance ratings from A-F. It’s often not clear for health and safety managers so the default position is F.
But is that level F glove going to be the best solution for workers who don’t need that level of protection?
Not always.
Coming back to compliance, if the F is a slightly heavier, less flexible or less comfortable glove that impacts a workers’ capability to do their job, there is an increased risk of them taking the glove off.
Check your gloves for wear and tear
Other hand protection risks lie in not regularly checking gloves or replacing them when they are no longer fit for purpose. And different types of gloves offer different challenges.
With a mechanical glove for example, you can often visibly see signs of wear - including the degradation of the coating or furring of the cut resistant liner – these are indicators that it’s time to replace the glove.
A lot of businesses now also launder their own workwear – including safety gloves - and we know from experience that not all gloves are tested post-industrial laundering. But it’s a reality that a cut resistant gloves for example can have their performance reduced if they go through a repeated laundry process. You are talking about water, heat, detergents, other garments with oils and greases being washed with them all capable of impacting the original cut performance.
Some gloves are tested post five washing cycles. But again, this is not something done automatically across the board. It is something that companies have to think about and monitor as performance compromise is likely. You have to re-test gloves.
Conclusion
Compliance reduces risk. And for organisations that consider and build the human factor into their hand protection programmes – the reward is likely to be higher compliance.
Hand protection companies such as Unigloves have teams available to support health and safety managers in the hand protection selection process – from hazard assessment to the right solutions provided, workplace trials and hand protection training. Utilising this expertise can help support any workplace hand protection programmes.
Sarah Bridge is sales director at Unigloves. For more information, visit https://uk.unigloves.com
- Unigloves strengthens its team with hand protection expertise
- Unigloves keeps winter working hands warm
- Keep winter working hands warm
- Glove sampling service
- Pearl range adds to its colours
- Helping hands
- Glove sampling service
- Industrial hand protection
- Unigloves announces Brexit contingency plans
- Website update delivers user benefits