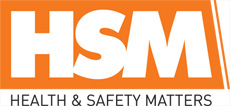
![]() |
Mark Sennett
Managing Editor |
![]() |
Kelly Rose
Editor |
Home> | PPE | >Ear Protection | >Peace of mind |
Home> | Managing Health & Safety | >Noise Monitoring | >Peace of mind |
Peace of mind
21 September 2022
Future proofing your hearing prevention programme is essential to ensure employers achieve peace of mind for their future employee wellbeing goals. Neal Muggleton looks at how this can be achieved.

THERE ARE some well recognised and frequently cited facts that support our assertion that Noise-induced hearing loss – or NIHL – is of pandemic proportions. An estimated 1.3 billion people globally suffer from hearing loss due to noise exposure – either through work or leisure activities.
Occupational noise exposure is responsible for 16% of all cases of disabling hearing loss in adults. Workers employed in the construction, manufacturing, mining, agriculture, utility and transportation industries, as well as military personnel and musicians, have the highest occupational NIHL.
In the UK, the HSE reported 14,000 new cases of work-related hearing loss in 2021 – and this is likely to be a conservative estimate.
A key problem of NIHL is that people don’t realise they have damaged their hearing until it is too late. And the effects are irreversible.
Within an occupational setting NIHL can limit an individual’s ability to communicate with others. This can lead to increased social stress, sadness, diminished confidence, poor self-identity, and adversely impact interpersonal relationships. Research also suggests it leads to an increased risk of dementia.
And the real tragedy? Occupational hearing loss is 100% preventable.
But NIHL doesn’t just affect individuals. The impacts of occupational noise exposure cause a tremendous financial burden on society. In the USA, the estimated annual compensation for occupational NHIL is approximately $242 million (more than £185 million per year). And this economic burden is increasing year on year.
These are a snapshot of the facts behind NIHL, but the question is how can this be so when we have regulation, established hearing conservation programmes, sophisticated measuring and monitoring equipment to understand the noise risk and wide variety of hearing protection devices to cater for all applications, personal preferences and yes budgets. So where does the problem lie?
Legal obligation
An Employer has a legal obligation to protect their employees from workplace risks, including noise. Ensuring compliance with safety regulations is obvious, but just meeting compliance could impact the business in other ways. If an employee claims for occupational hearing loss the burden of proof – and the cost of investigation – rests with the employer. It is the employer’s responsibility to prove that all precautions were taken and/or that the injury happened outside work.
To put that into context, the World Health Organisation estimates that more than 1 billion people (and growing) are at risk of hearing damage due to unsafe recreational hearing practices. Employers beware – you could see an increase in the number of hearing threshold shifts detected in your healthy surveillance.
Safety managers are highly motivated to help, but have many other priorities than just noise. They organise and deliver training, undertake workplace surveys and monitoring, ensure compliance, keep up with legislation and guidelines, update records – that’s a lot administration! Just think of all the data that generates – and none of it is in a format that helps them to do their job better or smarter.
The employee, meantime, attends mandatory training and may have the best intention of wearing the hearing protection provided – even if they are a bit cumbersome and uncomfortable. But once out in the field, employees are focussed on the task in hand. Background noise does not necessarily register – our brains filter it out when we are concentrating. Put simply, employees receive no information about personal noise exposure levels and are therefore not motivated to take necessary action.
So the problem therefore must rest with the PPE manufacturers? They have traditionally focussed on passive protection. Ear muffs and ear plugs when compliant with regulations (designed for manufacture) are more than adequate at attenuating noise, but they do not address the core issues around prevention of occupational NIHL. According to the HSE, 40% of PPE users get no protection whatever. For the other 60% protection is deemed inadequate. And about 14% of people just don’t wear their PPE at all. This probably isn’t the fault of the hearing protector, but is related to the incorrect selection, poor fitting, incompatibility with other PPE and actual use (wear-rate).
The safety industry is high in regulation and relatively low on innovation. Occupational NIHL is such a big problem it requires a step change – both in technological solutions and behaviour, because current occupational hearing loss processes are a failing.
Employers need better, more efficient ways to prove they are fulfilling obligations.
Safety managers need to be given pertinent information to enable them to make timely interventions, rather than being tied to a desk drowning in paperwork.
Employees require information and incentives to become proactive and take responsibility for their own wellbeing.
PPE needs to be reassessed – it’s too passive, often cumbersome or uncomfortable to wear, and it doesn’t help the user stay protected.
Driving habitual change
In safety critical, noisy environments, the ‘way it’s always been done’ can no longer be accepted. A new technology designed from a human centred perspective that focusses on active participation, with easy-to-access user features will help to drive habitual change. Lending that critical helping hand to the already stretched, safety managers’ efforts to provide a safer working environment for their team.
Future proofing hearing prevention programmes, is an enormous step that will require industries to evolve if they are to achieve their future employee wellbeing goals. Using integrated hearing loss solutions that act as personal, on-body tools, reinforces the value businesses place on the safety of every individual in their team.
It improves the life of the employer, who now has a reliable and continuous record of the noise exposure for every single employee, so that occupational risk can be distinguished from other sources of noise.
It improves the life of the safety manager, who can now easily identify where interventions are required. And they have more time to dedicate to such tasks, because they are no longer spending hours record-keeping and data-crunching.
Most importantly, it improves the life of the employee by warning them at the point of danger and giving them access to the information they need to keep themselves safe.
In summary, we need to accept that efforts of the past 20 years have not been working, and as an industry we need to pivot. Embracing a future of automation and integration into the process of noise monitoring to encourage better noise-related behaviour.
Neal Muggleton is chief operating officer at Minuendo. For more information, visit www.minuendo.com