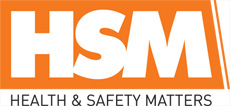
![]() |
Mark Sennett
Managing Editor |
![]() |
Kelly Rose
Editor |
Home> | Handling & Storing | >Forklift Truck Safety | >Help increase safety in lift truck operations |
Home> | Handling & Storing | >General Handling | >Help increase safety in lift truck operations |
Home> | Training & Development | >Guidance | >Help increase safety in lift truck operations |
Help increase safety in lift truck operations
03 October 2022
WHEN LIFT truck incidents occur, often the finger of blame points at operators. Sub-standard operator training or performance are deemed to be the issue.

Yet, poor supervision and management are often part of the cause. Without effective supervisors, operators will naturally pick up bad habits and cut corners. We all need reminding about the right way to do things from time to time.
Even experienced, fully trained forklift operators should be routinely supervised. They should be monitored when operating machinery to determine whether that they are abiding by safety protocols. This makes it important that the supervisor has up to date training.
In materials handling operations, the sense of pressure to meet tight deadlines can be huge. This may lead an unsupervised operator to neglect certain safety protocols. The result can be mistakes being made or incidents occurring.
Supervisors and managers must ensure that forklift operators continue to perform to the safest and most efficient standards. Even under the pressures of the live workplace.
Responsibilities of managers and supervisors
Supervisors and managers of lift truck operations play a vital role in their operators’ careers after training. Part of their role is to make sure what is learnt during training is applied in the day-to-day operation.
It is also the legal responsibility of the supervisor or manager to report and resolve safety issues. Also, that administrative and training requirements are met. A properly trained supervisor or manager will help encourage an environment of transparency and openness. Alongside promoting safe working principles and challenging poor standards.
Managers and supervisors should be aware of the day-to-day tasks that must be completed for compliance. Employers are required to provide adequate supervision for material handling operations. This is part of the Health and Safety at Work etc Act.
The Health and Safety Executive (HSE) ACoP L117 also states that “users, supervisors and managers must receive adequate training for the purposes of health and safety”.
You don’t need to be a forklift operator
Managers and supervisors do not need to be a qualified lift truck operator. But they are legally required by PUWER (Provision and Use of Work Equipment Regulations) to receive training. This should enable them to understand potential risks posed by the equipment. Plus, how to avoid or prevent them.
Managers and supervisors should be trained on how to conduct an effective observation. They should be able to communicate effectively with both operators and line managers. They should also be able to recognise unsafe practices and behaviour. This then helps to promote health and safety standards within the team.
These areas, and much more, are covered in the RTITB eLearning course ‘Managing and Supervising Material Handling Equipment Operations’. The purpose of this course is to introduce learners to the requirements of this critical role. Plus, the training and safe operating practices that should be at the heart of any MHE environment.
The self-paced training gives candidates the ability to recognise safe and unsafe practices. It covers how to understand potential risks and how to avoid them.
The interactive eLearning approach gives employers a simple and cost-effective way to arm their team with the necessary knowledge to improve workplace safety and comply with relevant legislation.
Learn more at www.rtitb.com
- Why telematics can never replace LGV driver training
- Forklift training warning
- Outsourced lift truck training is not always your best option
- Logistics conference and awards
- RTITB supports operation-wide compliance with new MHE Accreditation
- Raising the bar
- Lifting expectations
- RTITB eLearning offers advice on managing lift truck operations effectively
- Logistics awards
- Digital lift truck training tool