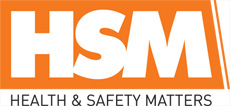
![]() |
Mark Sennett
Managing Editor |
![]() |
Kelly Rose
Editor |
Home> | Handling & Storing | >Forklift Truck Safety | >Raising the bar |
Home> | Handling & Storing | >General Handling | >Raising the bar |
Home> | Handling & Storing | >Safer Manual Handling | >Raising the bar |
Raising the bar
10 October 2022
It's important to involve your whole workforce in the safety of lift truck operations. Laura Nelson explains how to achieve this.

IT IS reported that overall accident rates are lower in workplaces where the wider workforce participates in health and safety. As an employer, what can you do to help engage lift truck operators, supervisors, and managers in health and safety? And how can you positively influence their behaviour?
Employees should feel they have a say
The awareness of the risks of slips and trips is supposedly greater (62%) where the workforce is consulted on health and safety issues, compared to when there is no involvement (28%)*.
Employers want to reduce the risk of incidents. So, it’s important for lift truck operators to understand their role in health and safety. They should feel they can actively contribute.
In research, 77% of the workforce felt encouraged to raise concerns in a good health and safety climate compared to 20% who felt encouraged to do so in a poor health and safety climate*.
Forklifts are one of the most commonplace types of equipment in logistics and warehouse operations, yet they are also among the most dangerous. It is suggested that 8,000 workplace incidents involving lift trucks* are reported annually.
With this in mind, your forklift operators may be some of the best positioned employees to understand workplace risks related to materials handling. And to take an active role in contributing to health and safety improvements.
Communicate the impact of incidents
Having a culture where incidents are never just an inevitable part of the job is key. Operators should have a clear awareness of the potential impacts of a lift truck incident occurring. At worst, this can include life-changing and fatal injuries.
Operators should also understand the fines that are possible should an incident occur. This does not come out of their pocket. But in a worst-case scenario, it could leave them out of a job. The related costs of ill health due to incidents can also have a similar knock-on effect. They create financial pressures within a business.
To tackle these subjects effectively, two-way communication is needed between health and safety managers, and their lift truck operators.
What this looks like will be different depending on your organisation’s size and culture. However, a lift truck operator training environment is a good place to have these conversations. Especially as regular training of operators is required for compliance.
Solutions such as eLearning can help. For example, the eTruck UK forklift and reach truck theory eLearning solution from RTITB helps encourage behaviour change around risk. Rather than a traditional presentation-led style of training, eTruck tells the story of a lift truck accident and the chain of events leading up to it.
Operators must engage with the story to understand and anticipate when, why and where the accident will occur. This gives a greater understanding of safe operating practices and the impact of an incident on the wider operation.
Educate on the role of managers and supervisors
It would be easy for operators to feel that should any incident occur, that it’s not entirely their fault. It is true that their managers and supervisors have a significant role to play. Incidents often occur as a result of poor or non-existent supervision. So, to reduce risks and comply with the law, those in these senior roles must be correctly trained.
MHE supervisors and managers play a vital role post-training. They must enforce the best practice and skills learnt during operator training in the day-to-day operation. Supervisors must ensure that forklift operators continue to perform to the safest and most efficient standards under the pressures of the live workplace.
Forklift operation supervisors or managers do not need to be a qualified lift truck operator. But they are legally required by PUWER (Provision and Use of Work Equipment Regulations) to receive training that enables them to understand potential risks posed by the equipment, and how to avoid or prevent them.
The Health and Safety Executive (HSE) ACoP L117 also states that “users, supervisors and managers must receive adequate training for the purposes of health and safety”.
Managers and supervisors should understand how to carry out an effective observation. They should be able to recognise unsafe practices and behaviour in order to promote health and safety standards within the team. They should also be trained to communicate effectively with both operators and line managers.
It is also the legal responsibility of the lift truck operation supervisor or manager to make sure that safety issues are reported and resolved, and that administrative and training requirements are met.
Many lift truck operations managers and supervisors are unaware that certain day-to-day tasks must be completed in order to ensure legal compliance. At RTITB, we find that not all management level employees are aware of their responsibilities. And are not always aware how to comply with industry laws.
That said, operators must also be made aware that they do have a level of accountability around incidents. Therefore, they must always operate to the safety standards delivered via their lift truck operator training. They should also follow their organisation’s rules and processes around health and safety.
Be transparent about legal obligations
Do your operators have any idea of what you have to do as an employer to remain compliant when it comes to health and safety? Compliance with relevant legislation and guidance is key should an incident occur. This is covered in operator training to a degree. Yet many operators may be unaware of exactly the level of requirements that have to be fulfilled.
Being transparent with operators about these requirements may change an operator’s view on the importance on health and safety. It could positively impact their behaviour.
Ensure they are aware of your responsibilities around:
-
The Health and Safety at Work Act
-
The recommended code of practice for rider-operated trucks (ACoP L117)
-
What is necessary in terms of training
-
Requirements for keeping training records
It all starts with training
Employers must remember that for compliance and safety, lift truck training should always be the first step. It is vital for educating operators on how to use and work around lift trucks. It is also essential for teaching how to reduce risks to themselves and others.
There is a mandatory level of lift truck operator training required for compliance. It is crucial to keep this up to date with refresher training or conversion training (where required). This is important for employed staff, as well as temporary and contract workers.
For safety, only correctly trained staff should be given an Authorisation to Operate MHE equipment. An authorisation to operate can be granted by the employer when it is satisfied that the employee has competently completed the three stages of operator training (Basic, Specific and Familiarisation). It is specific to the tasks the operator will complete, including the specific truck type and capacity and the load types.
It is the employer’s responsibility (not the Instructor) to issue the authorisation, which applies to anyone operating a lift truck full-time, occasionally, and even very rarely. Before an Authorisation to Operate is issued (in writing or via an electronic system), the employer should have a clear record of all of the training that was completed, when and on what type of machine. All authorisations should be logged and recorded.
An authorisation is not a guarantee of safe operation. There are many other factors required such as safe systems of work. Supervision also plays a key role.
Businesses should always continue to monitor and assess an operator’s ability. They should undertake regular risk assessments and assessments of operators. This helps to ensure optimum safety practices. Remedial or additional training (as well as refresher or conversion training) may also be required.
Don’t forget manual handling
Manual handling covers a wide range of everyday activities. Yet it is often overlooked when it comes to training workers, including lift truck operators. According to HSE (Health and Safety Executive), most work-related MSDs (musculoskeletal disorders) develop over time and the most common injuries are to the upper limbs, neck, lower back, and lower limbs.
Manual handling is one of the main contributors to MSDs. It is also a cause of many lost working days in the supply chain each year. It covers a wide range of activities, including lifting, push and pulling. Including moving a pedestrian operated manual pallet truck or roll cage around the warehouse. Something lift truck operators and warehouse workers will all do regularly.
Organisations should take manual handling training and processes seriously. Manual handling training helps to raise awareness of safe practices across the workforce. In turn, reducing risk.
Support safety in your operation
Organisations delivering training in-house, may find that RTITB Accreditation can help their workplace transport operations to improve standards, safety, and compliance.
*https://www.wpsafety.co.uk/blog/involving-your-workforce-in-health-and-safety
Laura Nelson is managing director for RTITB. For more information, visit www.rtitb.com
- Safer return to work with RTITB
- RTITB supports operation-wide compliance with new MHE Accreditation
- Logistics awards
- Event tackles logistics issues
- Developing logistics skills
- Finalists announced
- RTITB eLearning offers advice on managing lift truck operations effectively
- Lifting expectations
- Digital lift truck training tool
- Forklift training warning