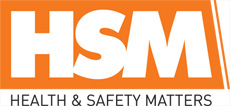
![]() |
Mark Sennett
Managing Editor |
![]() |
Kelly Rose
Editor |
Home> | Premises | >Fire Safety | >Honeywell “revolutionising” gas detection |
Home> | Breathing Safely | >Gas Detection and Monitoring | >Honeywell “revolutionising” gas detection |
Honeywell “revolutionising” gas detection
25 May 2018
HONEYWELL HAS announced a new feature of its cloud-based SafetySuite software platform that makes it easier to manage fleets of portable gas detectors.
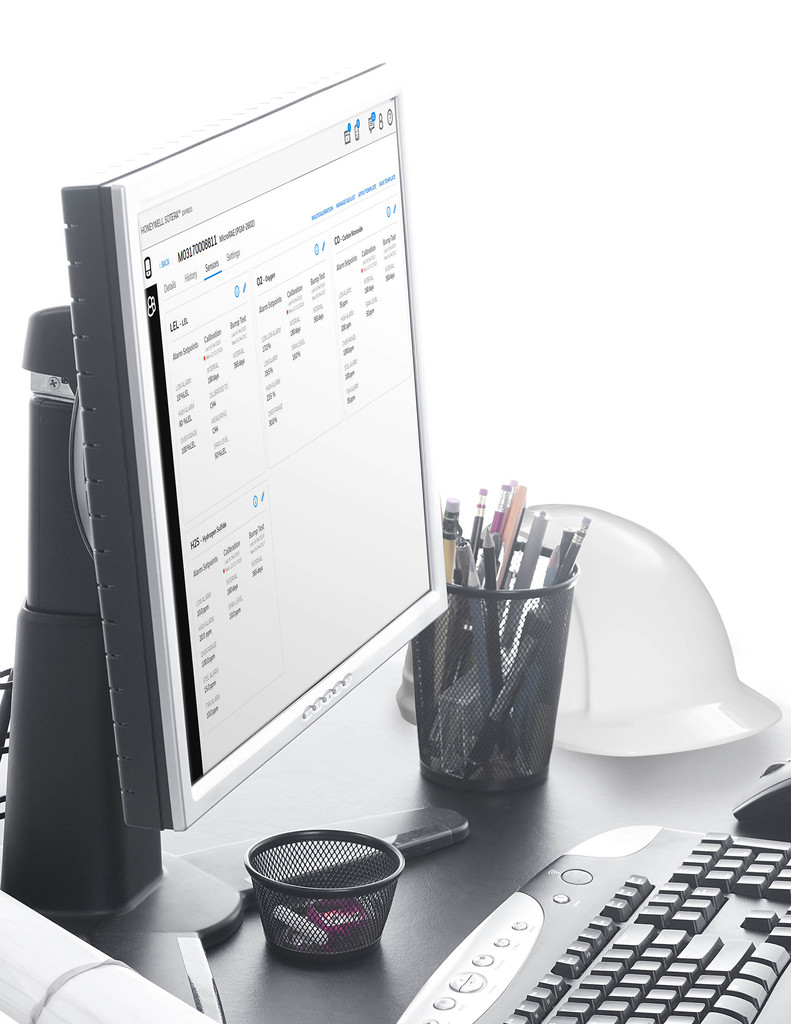
A global leader in gas detection technology, Honeywell has a broad range of sensing technologies developed to protect workers and operations from toxic and combustible gases, volatile organic compounds (VOCs) and other gas hazards. Honeywell gas detectors are used in thousands of commercial buildings, industrial plants, chemical refineries, laboratories, manufacturing plants, power plants, and drilling sites around the world.
The new Honeywell SafetySuite Device Manager software simplifies managing fleets of Honeywell’s leading portfolio of connected gas detectors across multiple sites. It helps to reduce paperwork, increase productivity and improve safety. When Honeywell devices are docked, the software automates configuration and testing of all the devices and implements firmware updates. It also creates a central repository of data for multi-site management of the detectors, and generates reports on device tests, safety events and incident investigations.
Honeywell Industrial Safety global director and connected worker leader Prabhu Soundarrajan explains: “Connected technology has the potential to revolutionise the way health and safety is managed. By providing better visibility over worker and site safety, connected solutions can ease the stress of managing compliance in even the most hazardous applications.
“For example, in the oil and gas industry, where workers often have to operate in confined spaces outside of the line of sight of the safety manager, the technology can reduce risks through increased automation and improved remote monitoring capabilities that enable faster emergency response. By having consistent access to accurate data of workers and their environment, for example delivered by Bluetooth and cloud-based safety solutions, safety managers gain greater insight into the status of the workforce and can take a more proactive approach to protecting and monitoring the well-being of workers.
“While the business advantages of connected working are clear, sometimes cost is a key factor in the decision making process for companies considering the connected worker route. The latest developments on the market however address this need by including retrofittable solutions that bring the main benefits of connected technology to existing devices.
“Ultimately good occupational safety and health is fundamental to the success of any business and real-time worker connectivity empowers and enables safety managers to react before something bad happens, preventing incidents and so taking safety to the next level. The latest connected safety solutions provide better protection for workers, ease the workload of safety managers, and help businesses optimise compliance, productivity and efficiency.”
Honeywell SafetySuite Device Manager features an intuitive user interface and a dashboard feature that quickly identifies areas of concern for safety managers across their organisations. The software manages a broad selection of both Honeywell BW and Honeywell RAE Systems devices on a common application.
It supports key maintenance tasks for gas detectors, including firmware updates and bump tests, and provides centralised monitoring of devices across an organisation with a consolidated view of alarms, faults and device issues for simplified reporting. The system also shows if an instrument failed a test or is overdue for a test.
SafetySuite Device Manager currently supports Honeywell BW Clip, GasAlertMicroClip devices using IntelliDoX and MicroDock II; and Honeywell RAE Systems’ MultiRAE, MicroRAE, ToxiRAE and QRAE 3 devices on the AutoRAE 2 cradle system. Key features of Honeywell SafetySuite Device Manager include:
- Supports both Honeywell BW and Honeywell RAE Systems detectors;
- 24X7 access anytime, anywhere from a computer, tablet or smartphone connected to the Internet;
- Works seamlessly across geographically dispersed locations, with multiple gateways per site and multiple instruments per gateway;
- Powered by Honeywell Sentience, Honeywell’s secure and standards-based Internet of Things (IoT) software platform that supports connected technologies;
- Secure data transmission and centralised data, with redundant storage and role-based access; and
- Requires minimal IT support and system administration, and no individual installs or manual software updates.
Additional Honeywell devices will be compatible with SafetySuite Device Manager soon, including GasAlertMaxXT II, GasAlert Micro 5, GasAlertQuattro and BW Clip 4. Future enhancements to the software will enable it to schedule equipment tests, and automatically generate reports on device tests, safety events and incident investigations. Users will also be able to customise alarm notifications.
For more information, visit www.honeywellsafety.com