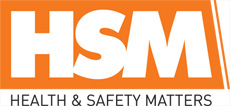
![]() |
Mark Sennett
Managing Editor |
![]() |
Kelly Rose
Editor |
Home> | Breathing Safely | >Gas Detection and Monitoring | >Harnessing technological advancements |
Home> | Breathing Safely | >Respirators | >Harnessing technological advancements |
Harnessing technological advancements
10 February 2015
Managing worker safety is challenging at the best of times but where gas is concerned, you are dealing with something that is often silent, invisible, odourless and potentially deadly. Chris Shaw talks to Honeywell about the increasing use of technology based systems that help protect workers through a combination of continual environmental monitoring and analysis, worker tracking, bump testing and respiratory protection.
Despite advancements in gas detection systems in the past 20 years, accidents continue to happen, with fatal or severe ill health consequences. In November 2014, four workers at a Texas insecticide factory died after being exposed to methyl mercaptan, a toxic gas used in the production of insecticides. Weeks later in South Korea, three workers died on a nuclear power plant construction site after a nitrogen gas leak.
For anyone managing gas safety, the Control of Substances Hazardous to Health (COSHH) Regulations set out the requirements for managing risks, from exposure avoidance to the provision of appropriate PPE.
According to Honeywell Analytics and Honeywell Safety Products, essential worker and asset welfare relies on continual monitoring, quick and accurate detection, respiratory protection and safe and effective escape from contaminated environments.
"Technology is playing an increasingly vital role in helping organisations achieve enhanced safety programmes, driven by the desire to remain ahead of increasing regulatory compliance and evolving insurance pre-requisites,” said Matthias Schwarz, product manager portable devices, Honeywell Analytics.
So what are the latest developments in gas detection?
Gas detection on the move
Portable systems now account for about half of the gas detection market due largely to their multiple functionality of personnel safety and continual location testing – often the only way of testing a remote location.
"Technology is not just about protection but also about up-to-the-minute, continuous information delivery and measurement," Schwarz noted. "Wireless technology is bringing major safety benefits, with 24/7 real time and plant-wide remote atmospheric monitoring linked to every individual or a specific location, along with GPS-based monitoring and Man Down tracking. "Reliable and accurate data is also critical. Wireless systems offer the flexibility to not only measure environments, but also provide remote instrument configuration and diagnosis, which can be sent to one central location or even multiple international sites.”
If a leak does occur, it’s vital to know the contaminant and exposure levels straight away. This helps manage not just the immediate situation, in the case of a major leak, but safeguards workers against smaller, longer-term exposures that can lead to chronic health issues over time, thereby reducing long-term liability risks.
The gas detection process should also include bump testing – the process of briefly exposing gas detection sensors to gas in order to check that they are working correctly. Whether you opt for a manual or automatic test method, bump testing should take place daily for static detection systems and before any portable devices are used.
Worker protection
Where the presence of harmful gas is detected, respiratory protection for quick and safe escape becomesvital. Technology is supporting this through the use of Man Down and worker tracking - particularly beneficial for safeguarding workers in remote and confined spaces.
"The precise location of workers and what they are exposed to are vital elements in rescue procedures," asserted Schwarz. "Tracking technology provides this information to control centres, letting them know whether workers are conscious or unconscious, providing a much clearer picture of the situation and precise rescue and evacuation requirements.”
Respiratory protection
The provision of respiratory protection needs to be included as part of any gas monitoring and detection programme. But what respiratory devices should you opt for?
Where oxygen levels are acceptable, the contaminant is known and filterable, and the area being worked in not an immediately dangerous to life or health (IDLH) atmosphere, consider filtering apparatus including a mask and filtration device for ambient air purification. Where oxygen levels are unacceptable or unknown and the risk uncertain, opt either for a compressed airisolating device with full mask, a hood or a chemical oxygen re-breather solution.
"In more than 70% of gas exposure cases, the risk to the worker is in the form of both gases and particulates, requiring the use of a combination filter with both activated charcoal and mechanical elements,” explained Christian Vieille, product manager respiratory, Honeywell Safety Products EMEA. Other respiratory considerations will include the type of face piece according to the level of protection required and the length of time needed to escape.
"For workers who have to carry their own protective respiratory equipment, consider the environment in which they will be working – confined spaces for example - and ensure equipment is light, compact, easy to use and quick to put on,” added Vieille.
Worker safety is paramount and failures in gas detection programmes and protection can have fatal consequences. Embracing the latest technological advancements provides safety managers with the environmental awareness, knowledge and understanding they need to enable them to protect workers at risk of gas exposure.