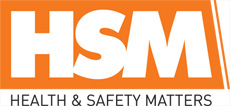
![]() |
Mark Sennett
Managing Editor |
![]() |
Kelly Rose
Editor |
Home> | Slips, Trips & Falls | >Fall Prevention | >Break the fall |
Home> | Slips, Trips & Falls | >Fall Protection | >Break the fall |
Home> | Training & Development | >Guidance | >Break the fall |
Break the fall
25 March 2024
Falls from height continue to be the most common cause of workplace fatalities in the UK. The latest figures show 40 workers were killed as a result of falling from height in 2022/23, a stark 51% of total construction fatalities*. Ben Haughton explains how fall protection solutions play a key role in safety.

WORKING AT height is simply defined as any instance of work where, if precautions were not taken, an individual could fall a distance that may cause injury or death. A person is working at height if they are working above ground level, if they could fall off an edge, or even if there is a chance that they could fall through an opening in the floor when at ground level. Working from a ladder is also considered working at height, so it is important for those responsible to understand their duties in ensuring safety1.
Safety
Like most workplace activities, the safety considerations for working at height follow the hierarchy of control, the process of which is governed fundamentally by the Working at Height Regulations 2005. These regulations put the responsibility of working at height safety on employers concerned with undertaking the work, as well as those who control working at height activity, such as building/facility managers that outsource the work to contractors.
To be compliant with the regulations, those responsible must ensure all work at height is properly planned and organised, including evaluating that everyone involved is competent. A proper risk assessment must be carried out, which should identify the necessary fall protection systems and detail how they will be used during the work. This equipment must be properly inspected and maintained prior to the work commencing.
In some cases, it is necessary to utilise personal fall protection equipment to ensure the safety of employees whilst they are working in potentially perilous conditions. There are two categories of personal fall protection equipment, the definitions of which must be understood to prevent choosing the incorrect safety equipment for the task. Fall restraint prevents workers from reaching a fall hazard, and fall arrest limits the distance and consequences of a fall. It should be noted that to operate under fall arrest conditions, a suitable and sufficient rescue plan must be in place to recover a worker should a fall occur.
High-level access solutions and anchor systems are designed to facilitate the safe and efficient working environment for all tasks that are performed at high level or where there is exposure to a fall. Personal fall protection systems incorporate several key elements, principally the anchorage, whose design and application is influenced by a number of variables. It is important to note that personal fall protection systems should only be considered once all other methods of safe working, including collective protection (guard rails), have been ruled out. In an ideal world, the need to work at height will be completely removed.
Personal fall protection systems
BS 7883 has been in existence since 1997 and was revised in 2005, amended in 2007 and recently revised again in 2019. This standard initially created comprehensive guidelines for the design, installation, and especially maintenance of anchor devices, such as eyebolts. Now, following its latest revision in 2019, it accounts for the advancements in fall protection technology and covers five types of anchorage system and provides a more prescriptive approach than the original versions, putting a greater emphasis on what must be done, as opposed to what should be done.
System design
For the designer, specifier or installer of fall protection systems, there has always been a requirement to provide evidence of the design process. In the revised standard, there is additional guidance on best practice to ensure all elements of a safe system have been considered and are documented.
For systems designed after November 2019, the System Designer must provide a system Technical File that contains a minimum amount of information, and this file should be made available for reference at every inspection. This is particularly important as inspections are often carried out by third parties, who may have no prior knowledge of the original system design. The file could include photographs taken at the time of installation and other details that may not be immediately obvious on initial inspection, this is of particular importance where hidden elements comprise parts of the anchor system.
BS 7883 is a code of practice and not a specification or regulation, meaning there is no legal duty to comply with it. It is however deemed best practice so if an accident were to occur due to the failure of a system whose design falls short of the requirements of BS 7883 and there was no evidence of a suitable alternative design, the individual, or individuals, responsible for its design and installation could be found negligent and prosecuted under the Health and Safety at Work etc Act 1974.
System inspection
Duty holders are responsible for ensuring that personal fall protection systems under their control are deemed either “In-Service” or “Out of Service”. Where equipment is deemed “In Service”, it must be inspected at least annually, in some cases more frequently i.e. those that come under the Lifting Operations and Lifting Equipment Regulations 1998 (LOLER), by a competent and qualified person. If the equipment is “Out of Service”, arrangements must be made to ensure that it cannot be used, ideally it will be completely removed.
Where the system inspector finds that a system is in safe condition and meets all the requirements of BS 7883: 2019, the system will receive a Pass. If a system does not fully meet the requirements of BS 7883: 2019 i.e. certain low-priority items of the Technical File are missing but is deemed safe to use, it will receive a Conditional Pass. However, if the system is found not to be safe, the system inspector can either call for an installation review (as set out in BS 7883: 2019 clause 12.2.5) and award a Conditional Fail or completely condemn the system and Fail the system completely. Importantly, for the system inspector to award a Pass or Conditional Pass, they must be completely satisfied that the system is safe to use and have the necessary evidence to support this.
In light of some industry concerns, a review committee, made up of expert representatives from across the industry, recently reviewed the existing standard. The committee has drawn up a Technical Bulletin Update, which aims to provide clarity on how Conditional Pass and Conditional Fail inspection outcomes should be treated when information in the Technical File for “legacy installations” is not available. The bulletin was reviewed by PH5, the committee that provides the UK input to European Standardisation in relation to protection of people from falls from height, and has now been published by the British Standards Institution (BSI) and is available on the BSI website.
Conculsion
The design, installation and inspection of anchor systems is a complex matter and providing the right access solution is often far from straightforward. The consequence of an anchor system failure could lead to serious injury or even death, so it is essential that developers, architects, constructors and duty holders seek the advice of service providers that are suitably qualified and have necessary experience of the design or installation they are undertaking.
Selecting the correct equipment, ensuring workers are up to date with training and taking the necessary precautions when responsible for a working at height task, will save lives.
Whilst not a legal requirement, commissioning of systems by a suitably qualified third-party provider can provide independent assurance that the anchor system has been designed and installed correctly.
Arco Professional Safety Services can provide expert assistance from initial concept design to installation, commissioning and periodic inspection.
References
* www.hse.gov.uk/statistics/fatals.htm
2 https://tinyurl.com/ypcv8b3a
Ben Haughton is technical director at Arco Professional Safety Services. For more information, visit www.arcoservices.co.uk/services/fall-protection
- Arco scholarship supports the enterprise of over a thousand Xiamen students
- Sound solution
- Confined space guide
- Gloves are off
- Preventing MSDs through technology
- Arco raises thousands for charity
- 'All in one' devices
- Flexible solutions for respiratory protection from ARCO
- Ethical status retained
- Makes sense