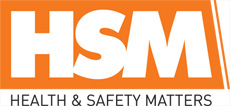
![]() |
Mark Sennett
Managing Editor |
![]() |
Kelly Rose
Editor |
Home> | Plant & Machinery | >Electrical Safety | >Defusing danger |
Defusing danger
02 December 2024
Ian Thorp provides an insight into how you can achieve electrical safety in the workplace.

Electricity both AC and DC, while essential to modern life, can pose significant dangers if not managed correctly. Each year, numerous workplace accidents involving electrical shocks or burns are reported to the Health and Safety Executive (HSE). While not all electric shocks result in lasting harm, under certain conditions, they can lead to fatal outcomes, a phenomenon known as electrocution.
By taking appropriate precautions when working with or near electrical systems, you can substantially reduce the risk of injury to yourself and others by selection of PPE tested for AC or DC use.
Understanding electrical hazards
The human body can conduct electricity making it vulnerable to shock. This occurs when direct contact is made with an electrified part while simultaneously touching another conductive surface at a different electrical potential. The current flows through the body, potentially causing effects ranging from mild tingling to severe injury or death.
Electricity is a serious workplace hazard when working on or near live electrical components or systems. National data documents fatalities and injuries triggered by electrical faults or accidental contact.
Key electrical hazards include:
1. Electric shock and burns
Factors influencing the severity include voltage, current strength, exposure duration, and the current’s path through the body. Injuries can include burns, muscle contractions, cardiac disturbances, and other health complications.
Electric shocks can also lead to secondary injuries, such as falls from ladders or scaffolds.
2. Electrical arc flash
An arc flash, often caused by unsafe practices or equipment failure, produces intense heat—up to 19,000°C—capable of vaporising metal and igniting clothing. Direct exposure can cause severe burns, while ultraviolet radiation from the arc can damage eyes.
3. Arc-blast impacts
The extreme pressure wave from an arc blast. This phenomenon poses risks to anyone in proximity and can result in hearing damage, memory loss from concussions, and injuries from flying debris.
4. Fire hazards
Faulty electrical equipment or installations are common causes of workplace fires.
Common causes of electrical accidents
Most electrical accidents arise from working on or near equipment that is:
- Believed to be de-energised but is actually live.
- Known to be live, but workers lack proper training, tools, or precautions to mitigate the risks.
Mitigating electrical risks
Risk assessment
Before working with or near electrical systems, conduct a thorough risk assessment. Ensure all equipment is designed, installed, and maintained to prevent risks of shock, burns, fires, or explosions when used correctly. The use of equipment specific safety standards supports effective risk management.
Safety measures to protect against electric shock
- Personal Protective Equipment (PPE) and insulated tools
The PPE regulation states PPE to be appropriate for the risk or risks involved.
It is documented that there is not an equivalence between AC and DC testing for products i.e. a product that is AC tested and therefore has an AC use voltage does not have a corresponding DC use voltage. Products should be DC tested to give a DC use voltage.
It is under debate that insulated tools (and ladders) are required to be compliant to the PPE regulation (Article 3 states compliance is required for PPE held). The consideration is supported by the fact that specific insulated tools and insulated equipment EN product standards specify within their requirements: Insulated, insulating and hybrid hand tools shall be manufactured and dimensioned in such a way that they protect the user from electric shock. Insulating hand tools minimise the risk of short-circuits between two parts at different potentials.
- Inspect PPE regularly and replace damaged items promptly. PPE maintenance requirements are outlined in the Personal Protective Equipment at Work (Amendment) Regulations 2022.
- Use PPE equipment relevant to the risk. AC tested for AC use and DC tested for DC use. This applies to all PPE including clothing for protection against DC arc flash.
- Use properly rated insulating gloves, matting and other protective gear (e.g. BS EN 60903 and BS EN 61111 standards).
- For arc flash risks, such as burns from arcing or flashover that cannot be avoided, use adequately rated, thermally insulating, flame-resistant PPE (including face/eye protection) arc flash protective clothing.
- Utilise insulating tools compliant with BS EN 60900.
- Ensure that Instructions For Use (IFU) have been supplied with each item and are:
- Read and understood. If they are incomplete or require further clarity, contact the manufacturer or authorised representative before use.
- Compliant with PPE Regulation
- Proper training and procedures Ensure workers are adequately trained in safe practices, correct equipment usage, and emergency response.
Environments with elevated electrical risks
Certain industries and situations carry higher risks of electrical hazards, including:
- Live line working, power generation and distribution: Tasks involving high-voltage equipment.
- Construction: Electrical installations and repairs.
- Manufacturing: Handling components e.g. transformers and control panels.
- Data centres and telecommunications: Installing or maintaining communication infrastructure.
- Renewable energy: Operations in wind and solar power facilities.
- Electric vehicles: Working with batteries and electrical components.
- Railways: Maintaining electrified tracks or overhead lines.
- Oil and gas: Managing electrical systems in hazardous environments.
- Emergency services: Firefighters and responders handling live electrical hazards.
- Laboratories: Using specialised electrical equipment.
Working at low voltage (e.g. 240 AC) is hazardous and has led to unnecessary energised work without proper justification or protection.
Guidance and best practices
The HSE’s HSG85 document, "Electricity at Work: Safe Working Practices" (Third Edition), is a comprehensive resource for ensuring workplace electrical safety. It covers legal responsibilities, risk assessments, training, equipment maintenance, and emergency protocols. Employers and safety professionals are encouraged to consult this guide for detailed, context-specific advice.
By adopting these practices, workplaces can effectively minimise the risks associated with electrical systems and create a safer environment for everyone.
Summary of live working standards
The table below gives the status of Live Working standards under revision in IEC committees and their current proposed publication date.
The list does not include published live working standards currently in use or in the revision process in CENELEC (EN Standards) e.g.helmets, boots, arc flash clothing.
Ian Thorp is dynamic specialist rubber technologist at Rubber By Design. For more information, visit www.rubberdesign.nl
- Kitchen fitter carried out illegal gas work
- Fire chiefs call for clear answers on cladding
- Protect workers in cold weather, urges HSE
- Extra mental health support for firefighters
- Metal processing firm in the dock after employee injured
- Health and Safety Matters Podcast - Episode 39
- Construction company fined £64k for height breach
- Patient fatally injured on minibus journey
- Pork pie maker prosecuted after workers lose fingers
- Graham Mackrell sentenced for Hillsborough role