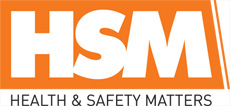
![]() |
Mark Sennett
Managing Editor |
![]() |
Kelly Rose
Editor |
Home> | Managing Health & Safety | >Safety Knives | >Cut knife accidents |
Cut knife accidents
06 December 2021
Identifying the hazards up front involving knife use is of paramount importance, says BSIF.
PLAN AND assess the risk for any work or project that involves cutting by eliminating dangerous fixed blades with safety knives, scissors or deburring tools. Correct planning/assessment could save you from life changing cut injuries or worse still!
- Being struck by a falling object or a cut from a hand knife accounts for over 10% of major injuries reported to HSE in the food and drink industries alone.
- Hand knife injuries typically account for between 25-50% of all lost time accidents in the plastics processing industry (HSE/Plastics Processors H&S Liaison Committee)
- 43,000 knife based reportable work place accidents in 2019*
- 58% of all workplace accidents involving manual tools were caused by knives*
Knife cut injuries
The Guidance statistics on the previous page are clearly showing us that knife injuries are a worrying occupational hazard for us all, at work or at home. Many suffer serious injuries that will affect their quality of life ongoing and sadly deaths do occur.
There are also knock-on effects for business in lost revenue due to time off work, possible litigation issues and Corporate Social Responsibilities to uphold.
Time now to take in this realisation of your own safety whilst undertaking jobs that need a knife. Don’t let lack of time or commercial pressures become a factor in your decision making when It comes to the next knife job. Try to think of the impact a knife injury could have on your life now and how it might ruin your quality of life in years to come. Imagine a tendon injury stopping you from playing your favourite sport or leisure pursuit. Imagine if you were not able to cradle your grandchildren. You owe that much to yourself, your family & your possible work colleagues.
So what can we learn from the above? Knife injuries usually happen when a knife slips during cutting or trimming. The knife blade can come into contact with the workers other hand and, causing a laceration to the hand or fingers.
What can we do to prevent such incidents?
Let us look at how to make changes and eliminate the hazards in our places of work, this Hierarchy of control graphic is commonly used but shows a clear pathway to handle risk analysis:
- Where possible eliminate the need for knives to be used
- Substitute knives for other tools such as deburring tools and scissors
- Use an engineering solution to reduce the risk, such as changing tooling or moulds to reduce/ remove the need for cutting activity.
- Administrative – Ensure that there is a set knife policy to ensure that use of cutting tools Is managed.
- PPE – final line of defence. Use of suitable cut-resistant gloves/sleeves/garments to enhance protection from accidental cuts.
After completing the risk assessment, if you still need to use a knife, choose a safety knife.
HSE guidance
‘How to reduce hand knife injuries’ (PPS12 rev1) gives us a great description of types available:
Group 1 – includes bladeless cutters, such as reel snails and disposable concealed blade knives that help to ensure that not only is the blade edge concealed, but also the remotest chance of injury during blade replacement is ruled out.
Group 2 – (concealed blades) are cutters designed to conceal the blade edge from the possibility of personal injury. These are cutters with changeable blades.
Group 3 – (fully automatic blade retraction) knives are designed to not rely on the operator to retract the blade. sometimes called intelligent cutters. Once the blade leaves the material being cut it automatically and immediately retracts into the handle.
Group 4 – (spring-loaded blade retraction) Once cutting has begun, the operator removes their thumb from the slider. The blade will remain engaged with the material being cut, but as soon as the blade leaves the material. The blade will spring back into the safety of the knife handle.
Group 5 – (manually-operated blade retraction) knives have to be manually retracted as well as manually extended. Therefore, if the knife is placed down the blade will remain exposed.
Take a look at the knife itself before buying, assess its safety performance claims. Take a look at any testing or proof that the manufacturer has available that backs the products performance claims. This will allow you to make a better, more informed decision on whether this is right Safety knife for you.
NB: Unfortunately there are NO ISO/CE/UKCA/BSi standards applicable for safety knives at this current time. The best internationally recognised generic product safety standard, including safety knives, is the German GS mark**.
In the UK Safety knives are covered under the Provision and use of work equipment Regulations 1998 (PUWER). PUWER also places responsibilities on businesses and organisations whose employees use work equipment, whether owned by them or not.
What about your Safety knife policy? Consider the following points while making yours:
-
Elimination
-
Specify the right knife
-
Ensure spare knives and blades are available
-
Provide safe storage for knives/blades
-
Specify the right PPE
-
Consider the working environment
-
Develop and deliver training
-
Checking & monitoring
You now have your risk analysis, you know that you have to use a knife and you have selected the correct knife. What about the last line of defence? PPE or Personal Protective Equipment.
Selection here is key: Is the risk of injury and the severity of the hazard low or high?
This table can be used as a quick simple guide, but using a higher rated glove is always preferable assuming good grip, dexterity, comfort, size, touch sensitivity and general performance is acceptable.
Example Highlighted: Risk of cut is 4 and hazard severity is 3, a Cut D Safety Glove would be seen as appropriate. If a glove offering D or higher is acceptable in all other aspects (some listed above) then this would also be considered acceptable.
Featured below are some typical PPE examples. These take cut resistant yarns made from HPPE (High performance Polyethylene) Kevlar, Aramids, Dyneema and knit them into gloves, sleeves and even some forms of body protection. Coatings are sometimes added for grip and resistance to liquids.
Featured below is the current glove standard and pictogram used for gloves in use against mechanical risks. The key shows the various glove ratings and how they are scored upon test. In general, the higher the score the higher the protection.
For Cut, there are 2 methods, the first is a Coupe Test graded up to a maximum of 5. The second is the high cut test provided by TDM ISO 13997 and is graded alphabetically.
The chart below tells us quickly how to navigate these test results.
Coupe test method
High cut test method
Key considerations for hand protection with knife use:
- Secure grip for knife use and handling goods
- Level of dexterity
- Use and suitability with other PPE ie protective sleeves, aprons, shirts, coveralls
- Is there oil or liquids present
- Correct size and fit are crucial
- Hand protection required for other tasks (removing gloves often, ensuring to always put back on)
- Wear and tear, understanding when gloves are past their usable life span and need to be replaced (no longer protect)
Do not compromise your safety and Health whatever the situation. If you are undertaking a cutting job. Stop and think. How can you keep your hands safe every day?
* Statistic referral from German Social Accident Insurance 2020
** Intertek guide to GS mark certification
For more information, visit www.bsif.co.uk
- BSIF announces 2015 Industry Award Winners
- From the CEO's Desk
- BSIF announces new members
- Questions & Answers - Selection of chemical clothing
- CEO's desk
- And the winners are...
- Managing the risk of Hand Arm Vibration Syndrome (HAVS)
- Trading Standards launches national project on leather gloves
- The Oscar's of the health and safety world!
- The Clean Air? Take Care! Campaign