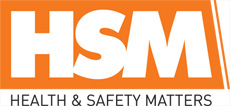
![]() |
Mark Sennett
Managing Editor |
![]() |
Kelly Rose
Editor |
1/48 (1 to 10 of 475)
Understanding the new Personal Fall Protection Equipment Standard: BS 8681 | 30/07/2025 |
---|---|
THE BSIF Height Safety Special Interest Group (BSIF HSG) has unveiled an overview of the new Personal Fall Protection Equipment Standard, BS 8681, which outlines its implications for the industry and those it impacts. Fall protection equipment plays a crucial role in safeguarding workers from the risks associated with working at height, which remains one of the leading causes of workplace fatalities and injuries in the UK. The use of proper fall protection systems, combined with rigorous training and adherence to safety standards, is essential in mitigating these dangers. The introduction of the new British Standard, BS 8681, marks a significant step forward in this area. Officially titled "BS 8681 - Personal fall protection equipment – Anchor systems – Specification for provider competence", this Standard sets out clear guidelines for the industry, emphasising competence and safety across all aspects of fall protection systems. By focusing on the necessary skills, knowledge, and experience required at every stage of fall protection—from design to installation, inspection, and training – BS 8681 aims to enhance safety and reduce the high number of accidents and fatalities associated with working at height. A complement to BS 7883 BS 8681 has been designed to work in tandem with the existing BS 7883 standard, which focuses on the technical aspects of designing, installing, and inspecting personal fall protection anchor systems. While BS 7883 addresses the hardware and structural integrity of these systems, BS 8681 broadens the focus to include the competence of all professionals involved. This new Standard emphasises that every person in the "safety chain"—from system designers to installers, inspectors, and trainers—must have the necessary skills, knowledge, and experience to ensure that fall protection systems are safe and effective. Competence and responsibility One of the key objectives of BS 8681 is to raise the competence levels across the industry. The Standard aims to ensure that those involved in the design, installation, and inspection of fall protection systems are thoroughly qualified. For instance, System Designers, whose role was first introduced in BS 7883, must ensure that the systems they design are not only compliant with safety standards but also fit for purpose throughout their operational life. This includes considering factors such as safe construction, use, rescue, and inspection. BSIF HSG member Elizabeth Rickard of Spring Structural Ltd comments: "BS 8681 is a promising step forward in addressing industry challenges, particularly in the realm of personal fall protection systems. Generally, it takes two years to train a System Designer to simply provide the pertinent information. "Given my experience in training system designers over that two-year period, BS 8681 could significantly streamline onboarding by offering a clearer framework for competence. It also has the potential to improve collaboration with other stakeholders by establishing shared expectations. Furthermore, by ensuring that upstream information is more reliable and standardised, it can help reduce both rework and risk throughout the design and implementation process." BSIF HSG member Harvey Dun of Time Consulting adds: "BS 8681 is a good start to assist in setting the benchmark of competency for people involved in the fall protection industry. Dun explains: "The Standard provides the purchasers of products and services, often referred to as the duty holder, with guidance check lists to confirm the provider they engage is suitably competent. These checklists may be adopted by Safety Schemes in procurement (SSIP) when assessing those providers operating in the fall protection industry." Manufacturing and testing Manufacturers also play a crucial role under BS 8681. The Standard provides clear guidelines on the necessary steps to ensure that anchor devices and other components meet stringent safety requirements. This involves rigorous testing, certification, and documentation to guarantee that these products can withstand the demands of real-world use in high-risk environments. Training and qualifications Training and competency are central themes in BS 8681. The Standard supports the development of qualifications, such as the Level 3 apprenticeship and NVQ Level 3 for permanent fall arrest technicians, which is part of a broader effort to professionalise the industry. This initiative, driven by BSIF HSG, aims to close the skills gap and ensure that all workers in the fall protection industry are equipped with the necessary knowledge and experience to perform their roles effectively. BSIF HSG member, John Hynes of Autumnal Services Ltd, comments: "Formal, sector-specific qualifications, such as the NVQ Level-3 for installers, should raise the quality of installers and inspectors. And the introduction of BS8681 will make it clear to Duty Holders and others that there are minimum acceptable competency levels." Inspection and auditing BS 8681 emphasises the importance of thorough inspection and auditing processes to maintain the integrity of fall protection systems. Inspectors must be highly skilled and knowledgeable, capable of identifying potential hazards that could compromise safety. Regular audits, both internal and external, are recommended to ensure ongoing compliance with the Standard, thereby ensuring that systems remain safe throughout their operational life. A positive impact on the industry The introduction of BS 8681 is expected to have a profoundly positive impact on the fall protection industry. By setting higher standards for competence and safety, it aims to drive a cultural shift towards greater accountability and professionalism. Duty holders can now have greater confidence that they are working with competent professionals who can deliver safe, compliant, and effective fall protection systems. BSIF HSG member Ben Haughton of Ocean Technical Safety Services Ltd comments: "The fall protection industry is entering a new era; with the publication of BS 8681and the support of BSIF, professional competency standards within the industry are going to be raised and in turn, greatly improve worker safety." Hynes adds: "There will be a period where these new expectations and requirements are a challenge to our sector, but in the long term, they are completely reasonable and readily achievable, and they should lead to a significant improvement in the quality of design, installation and record keeping we see for fall protection systems." Dun concludes: "My message to the companies and people who procure installation, inspection and consultancy services is to use BS8681 as part of the tools available in their due diligence process of selecting competent contractors." To view the BSIF's overview of BS 7883, designed to help the understanding of best practice for those designing, installing, maintaining and inspecting anchor devices and systems, visit: www.bsif-heightsafetygroup.org The BSIF (HSG) has produced a webinar that brings together industry experts to discuss the requirements of providers within the industry. The webinar is available via the following link:- BS 8681:2024 Personal fall protection equipment – BSIF HSG Webinar – BSIF Height Safety Group. For more information: https://www.bsif-heightsafetygroup.org/ |
|
|
|
BS8681:2024 - elevating fall protection standards | 01/07/2025 |
THE INTRODUCTION of BS8681:2024 marks a significant advancement in fall protection, establishing rigorous competency requirements for personal fall protection equipment and anchor systems. This standard ensures that professionals designing, installing, and inspecting fall protection systems meet the highest safety standards, thereby reducing risks and improving workplace safety. The importance of BS8681:2024 BS8681:2024 is a comprehensive guide to best practices in fall protection, encompassing areas such as:
By implementing this standard, the industry has started on the journey to raise the level of professionalism, competence and accountability, ensuring that all fall protection systems adhere to stringent safety regulations. Collaboration: Driving progress in fall protection training The introduction of BS8681:2024 has been supported through a strategic partnership lead by BSIF who have ensured that extensive collaboration with organisations such as 8point8 Training, Kee Safety, Hydrajaws, SFS and other key industry personnel. These organisations have combined their expertise to develop industry leading training programs that meet industry requirements, and competency frameworks with the new standard, ensuring a seamless transition for organisations adopting BS8681:2024. Key contributions of collaborating organisations
Their collective efforts are ensuring that work-at-height professionals receive the necessary training, tools, and industry knowledge to meet BS8681:2024 requirements and maintain a safer working environment. SFS, HydraJaws and Kee Safety have had a huge part to play in supporting 8point8 Training with the roll out of the training to the wider industry. Jonathan Seymour of SFS Group Fastening Technology Ltd explained: “Via our membership of the BSiF Height Safety Group, SFS was delighted to have the opportunity to support 8point8 Training Ltd with their delivery of the Level 3 Fall Protection Technician Apprenticeship and the Level 3 NVQ Diploma in Accessing and Rigging. This included training of key 8point8 Training personnel, sample SFS fall protection systems for the newly created Fall Protection Training area in Doncaster and, with the kind permission of their roofing OEM partners, the repurposing and supply of test roofing materials, such as metal decks and cladding sheets, to which apprentices are able to practice installation of roof top mounted fall protection systems”. Graham Willmott, Kee Safety - risk management & standards director explained: “The opportunity to partner with 8Point8 and supply fall protection product, training and resources to facilitate 8Point8 to deliver the Level 3 Fall Protection Technician Apprenticeship and the Level 3 NVQ Diploma in Accessing and Rigging, provides Kee Group and the industry with an opportunity to train fall protection installers & inspectors to the highest standards and achieve a professional qualification.” Key 8point8 staff attended bespoke Kee Safety training sessions run by Simon Oates, Kee Safety fall protection training manager, to ensure the correct installation of our latest product, and this included our inspection App for recording inspection data. This ensures the apprentices can put into practice the required installation techniques to ensure product compliance and safety.” Adrain Morgan of Hydrajaws commented: “Hydrajaws were thrilled to support 8point8 Training Ltd in the delivery of the Level 3 Fall Protection technician apprenticeship and the Level 3 NVQ Diploma in access and Rigging. It has been exciting to see the training facility take shape with the assistance of other supporting companies and this is a credit to David and his team. Training was undertaken with key 8point8 staff to ensure the correct use of our latest equipment, and this included our App for recording test data. This ensures the apprentices can practice and learn present time techniques of testing.” Celebrating milestones in fall protection training In addition to the new standard and collaborative efforts, the industry is celebrating major accomplishments in fall protection training courses that have been developed to ensure site competence. First completers in Level 3 NVQ in Access and Rigging - Fall Protection The first two individuals employed by a major Group employer have successfully completed the Level 3 NVQ in Access and Rigging - Fall Protection, accredited by Smart Awards. This regulated qualification is critical for ensuring that professionals have the necessary skills to safely perform access and rigging tasks, further strengthening the industry’s workforce. Level 3 Fall Protection Technician Apprenticeship: A new era The first learners are now reaching completion of the Level 3 Fall Protection Technician apprenticeship, signalling a new era of specialiaed fall protection expertise. This apprenticeship equips individuals with:
Kee Safety one of the largest employers in the fall protection Industry have started to see the benefits of the apprenticeship programme with individuals now starting to complete their apprenticeships and enter their final assessments. Graham Willmott, Kee Safety - risk management and standards director explained: “Our Group recognises the importance of training and development of our fall protection technicians and inspectors. As soon as the apprenticeship program was available, we committed to the program and enrolled our delegates.” David Ravensdale, head of training at 8point8 Training said: “These qualifications are raising the industry’s standards, ensuring that current and future professionals are fully equipped to handle the complexities of installing and maintaining fall protection systems.” The road ahead: Advancing fall protection With BS8681:2024 now implemented, alongside industry collaboration and major training milestones, the fall protection sector is undergoing a transformative shift. These advancements emphasise worker safety, competency development, and adherence to best practices—critical factors in ensuring long-term success. Alan Murray of BSIF explained: “As more professionals achieve advanced qualifications, the industry will continue to evolve, innovate, and strengthen safety standards, creating a highly skilled workforce capable of delivering excellence in fall protection.” |
|
|
|
PPE Saves Lives! | 04/08/2025 |
The British Safety Industry Federation (BSIF) has recently launched PPE Saves, a new campaign spotlighting the vital role performed by personal protective equipment in protecting workers and ensuring people and businesses thrive. You can hear more about this at HSM Live Coventry. PERSONAL PROTECTIVE Equipment (PPE) is sometimes undervalued, yet it can mean the difference between life and death, safety and injury, long-term health and preventable harm. While other safety controls are essential, PPE remains a vital line of defence when risks cannot be eliminated. Every day, millions of workers rely on PPE not just for protection but for peace of mind. When it’s well-designed, fit for purpose, correctly certified, and correctly fitted, PPE supports comfort, confidence, and a stronger safety culture. The PPE Saves campaign urges organisations to take great care and involve their employees when selecting these safety critical products. PPE Saves Lives! PPE is far more than just a precaution—in some cases lives depend on it. While it's often difficult to prove when PPE has directly saved a life, there are consistently high levels of serious workplace accidents where the right protective equipment could have made a critical difference. For example, incidents involving moving vehicles remain one of the leading causes of workplace deaths. Wearing high-visibility clothing can help workers stay seen and safe and reduce such incidents. Another serious hazard is asbestos exposure, which the WHO identifies as the top cause of work-related deaths globally. Respiratory Protective Equipment (RPE) is crucial in protecting workers from inhaling these deadly fibres. Every part of the body matters PPE not only saves lives but also saves heads, eyes, faces, hearing, lungs, hands, bodies, and feet. From head to toe, it prevents injuries, reduces severity, and improves recovery outcomes. In a study of occupational use, the correct non-slip footwear reduced falls by 49% (BMJ).
When PPE performs, people thrive Properly specified, well-fitting, and high-quality PPE not only enhances safety but also allows workers to carry out their jobs effectively and remain in the industries they enjoy for longer. Work can be demanding but the right PPE does more than just protect—it enables people to work safely and comfortably. Beyond protection, great PPE improves comfort, confidence, and morale and even staff retention. When sourced responsibly, well-designed, fit for purpose, correctly certified, and correctly fitted, PPE contributes to a safer, more productive workforce. PPE isn’t just about compliance, it’s about keeping people well, engaged, and performing at their best. Commenting on the launch of PPE Saves, BSIF CEO Alan Murray says: “PPE is vital for protecting lives across Britain every single day. But not all PPE performs well, and that’s a serious problem. “PPE Saves is a campaign dedicated to making sure workers have access to suitable and reliable PPE because investing in quality products isn’t just about safety, it shows you value your people. “There’s a wide range of innovative, comfortable, and sustainable PPE on the UK market. Yet poor-quality products are still in widespread use, compromising worker comfort and putting lives at risk. That’s why we’re raising awareness of what good PPE looks like, where to find it, and how to make sure it performs.” For PPE that protects people and helps workers and businesses to thrive, visit: www.registeredsafetysupplierscheme.co.uk For support in specifying PPE, find out more about the BSIF’s Sourcing Safety course as well as the Duty Holder Membership Scheme, which includes access to a PPE Helpline, visit: bsif.co.uk/join-bsif/ Share your PPE story The PPE Saves campaign highlights real-life impact. We invite workers, employers, and safety professionals to share their experiences. Has PPE saved your life, prevented an injury, or improved your working conditions? Join the conversation and help raise awareness by sharing your story using #PPESaves. Find out more about the campaign at BSIF's seminar at HSM Live Coventry, or visit www.bsif.com |
|
|
|
CEO's desk - May 25 | 12/05/2025 |
As the British Safety Industry Federation launches its BSIF Saves Campaign, Alan Murray underlines the case for better PPE in the workplace. ON THE 8 April 2025 BSIF launched the PPE Saves Campaign during the Health and Safety Event at the NEC, urging organisations to take greater care when selecting these safety-critical products and to involve the people who use them in every step of the process. Why did we take this step? The answer is simple! Personal Protective Equipment (PPE) is such a common sight that its’ importance can sometimes underestimated or undervalued, but when you think about it, it can mean the difference between life and death, safety and serious injury, long-term health and irreversible harm. While other safety controls are essential, PPE remains a vital line of defence when risks cannot be eliminated. We felt that it was time for a strong reminder of the vital role that PPE plays ensuring safety, health and the contribution that it can make to wearer’s feelings of wellbeing. I have had the privilege to serve the BSIF membership for over 11 years and in that time we and the membership have made best endeavours to ensure that non-compliant and dangerous PPE is removed from the market and that workforces are provided with PPE that performs as it should so that it can save when called upon to do so. Let’s remember that every day, millions of workers rely on PPE not just for protection but for peace of mind. When it's well-designed, fit for purpose, appropriately certified, and correctly specified against the hazard and properly fitted, PPE supports comfort, confidence, a stronger safety culture and better outcomes for both the wearer and the business.. PPE Saves Lives! PPE is far more than just a precaution, in some cases lives depend on it. While it's often difficult to prove when PPE has directly saved a life, there are consistently high levels of serious workplace accidents where the right protective equipment could have made a critical difference. For instance, incidents involving moving vehicles remain one of the leading causes of workplace deaths. Wearing the correct high-visibility clothing and other protective equipment can help workers stay seen and safe and reduce such incidents. Another serious hazard is asbestos exposure, which the WHO identifies as the top cause of work-related deaths globally. Respiratory Protective Equipment (RPE) is crucial in protecting workers from inhaling these deadly fibres. In addition to asbestos and other breathable toxins the threat from Silica is becoming ever more recognised. . /, Every part of the body matters PPE not only saves lives but also saves heads, eyes, faces, hearing, lungs, hands, bodies, and feet. From head to toe, it prevents injuries, reduces severity, and improves recovery outcomes:
All of the above statistics refer to protection from direct harm but we should also reflect on the fact that PPE is worn over long shifts and must be comfortable for the wearer during that time The long-term impact of preventable injuries We rarely consider how life-changing an injury can be until it happens. Beyond the pain of the injury itself, treatment and time off work, even minor injuries can have lasting consequences, while severe ones can alter everything. Let's consider some of the consequences of injuries that could have been prevented with proper PPE: Head Protection: Head and brain injuries can result in memory loss, cognitive difficulties, or permanent disabilities. Properly rated correctly worn helmets can mean the difference between walking away from an accident or facing lifelong consequences. Hearing Protection: Noise-induced hearing loss is permanent and progressive, often leading to social isolation and cognitive decline. Well performing correctly used hearing protection prevents irreversible damage. Eye Protection: A single eye injury can result in partial or total blindness. Protective eyewear protects against chemical splashes, flying debris. Correctly fitted eyewear prevents ingress damage and properly thought out selection of lenses will prevent damage from hazardous light exposure. Foot Protection: Injuries such as fractures, burns, or punctures can lead to chronic pain and mobility issues. Non-slip, impact-resistant footwear reduces workplace falls and injuries. Comfort is vital across all PPE but perhaps most obvious in footwear (and protective clothing) as these items are often worn continuously through long work-shifts. Comfort and fit is vital for the wearer. Respiratory Protection: Inhaling hazardous substances can lead to chronic lung diseases, impacting long-term health. Good fit for purpose respiratory protection, correctly fitted, minimises these risks. Hand and Skin Protection: Severe burns, chemical exposure, and deep lacerations can cause permanent damage, affecting daily activities and work performance. The right gloves and protective clothing safeguard against these hazards but again these must be well fitted, comfortable and must not impair the wearer in their duties. Proper fall protection builds trust and reduces risk. Whether we are talking about permanent fall protection systems or PPE worn while working at height, The correct equipment properly specified and installed protects and reduces physical and mental strain, letting workers move confidently and work productively at height. When PPE performs, people can thrive Properly specified, well-fitting, quality PPE not only enhances safety but also allows workers to carry out their jobs effectively and remain in the industries they enjoy for longer. Work can be demanding but the right PPE does more than just protect, it enables people to work safely and comfortably. Beyond protection, great PPE improves comfort, confidence, and morale and even staff retention. To achieve this, it's vital to involve the workforce in PPE selection, because those who wear it know best what works and what doesn’t. So, through the PPE Saves Campaign BSIF are urging duty holders to look beyond the basics and specify PPE that can make a difference to wearer protection through specifying in conjunction with wearers PPE that is right for the hazard and suitable for their workforces. Alan Murray is CEO of BSIF. For more information on PPE Saves please go to PPE Saves Campaign – BSIF . |
|
|
|
BSIF Safety Award Winners 2025 | 13/05/2025 |
BSIF IS delighted to announce the winners of the BSIF Safety Awards 2025! The Awards were held on Wednesday 9 April as part of the SHE Awards at The Vox, NEC, Birmingham. The evening was hosted by Jason Manford and was a huge success. We would like to congratulate all of the Commended, Highly Commended and Winners across our four categories: Product Innovation Award PPE Winner: Hunter Apparel Solutions – Flexguard Highly Commended – Elten Safety Shoes – Lakers XXT BTG Boot Highly Commended – Ansell UK Ltd – AlphaTec® 53-003 Commended – Univet SRL – 5X2 OTG eyewear Commended – 3M – Peltor PIC-100 Product Innovation Award Safety Products (Non PPE) Winner: Chemstore – ionGuard Commended: Seton – EasyExtend Max Retractable Barrier Commended: Eave – Eaveolution Customer Service Award Winners Guardsman Safety Solutions – Winner The Caley Group – Winner Lee Brothers – Highly Commended Eave – Highly Commended Zero Gravity Safety – Commended Leo Workwear – Commended Safety Solution Award Winner – Hunter Apparel Solutions – Deconology Highly Commended – EAVE – EAVEOLUTION Highly Commended – Sundstrom SR – Sundstrom Safety Academy RPE Training Commended – Staysafe PPE – PPE Laundry and Recycling Commended – Total Safety UK – Two Tiered Monitoring |
|
|
|
CEO's desk - March 25 | 13/03/2025 |
Alan Murray introduces the British Safety Industry Federation's brand-new campaign, which will be launched at the Health & Safety Event 2025. I’M EXCITED to share that the British Safety Industry Federation (BSIF) will be introducing ‘PPE Saves’ at the Health & Safety Event 2025, a brand-new campaign highlighting the critical role of high-quality PPE in protecting people at work. BSIF membership, as a lot of people now know, comprises companies dedicated to excellence in PPE production and supply, consistently exceeding minimum standards - many of whom feature regularly within this publication. The PPE Saves campaign aims to emphasise the critical role it plays in saving lives and ensuring safety while emphasising the value of investing in high-performing quality PPE – as is available from many of our members. Why PPE Saves matters Personal Protective Equipment (PPE) can sometimes be undervalued, yet it can mean the difference between life and death, safety and injury, long-term health and preventable harm. While other safety controls are essential, PPE remains a vital line of defence when risks cannot be eliminated. Millions rely on PPE daily for protection, comfort, and well-being. Properly designed and fitted PPE enhances morale, promotes a culture of safety, and helps businesses maintain a healthy, engaged workforce. The PPE Saves campaign stresses the importance of investing in certified, fit for purpose quality PPE that meets safety standards and delivers real performance. The statistics speak for themselves: PPE Saves Lives PPE is not just a precaution—lives depend on it. Workplace safety statistics show its impact: • Falls from height caused 36% of workplace fatalities in 2023/24 (HSE). Proper fall protection can help prevent these tragedies. • Moving vehicle incidents remain a leading cause of workplace deaths (HSE). High-visibility clothing mitigates these risks. • Asbestos exposure is the leading cause of work-related deaths worldwide (WHO). Respiratory Protective Equipment (RPE) is essential protection. Despite these figures, PPE quality varies significantly. PPE Saves aims to change this by advocating for high-performance protective equipment. Every part of the body matters PPE not only saves lives but also saves heads, eyes, faces, hearing, lungs, hands, bodies, and feet. From head to toe, it prevents injuries, reduces severity, and improves recovery outcomes. We rarely consider how life-changing an injury can be—until it happens. Even minor injuries can have lasting consequences, while severe ones can alter everything. When PPE performs, people thrive Properly specified, well-fitting, and high-quality PPE not only enhances safety but also allows workers to carry out their jobs effectively and remain in the industries they enjoy for longer. Work can be demanding but the right PPE does more than just protect—it enables people to work safely and comfortably. Beyond protection, great PPE improves comfort, confidence, and morale and even staff retention. When sourced responsibly, specified, fitted, and suitable PPE contributes to a safer, more productive workforce. PPE isn’t just about compliance—it’s about keeping people well, engaged, and performing at their best. Find out more at the Health & Safety Event 2025 Come and visit us on Stand: 3/P30 at the Health & Safety Event 2025 being held from the 8-10 April at NEC, Birmingham, to find out more about how to source PPE that not only saves lives but helps workers and businesses to thrive. The BSIF team will be on hand throughout the event and would be delighted to discuss this important new campaign. The BSIF represents trusted suppliers dedicated to delivering protective equipment that meets the highest safety standards. These suppliers provide certified PPE designed for protection, comfort, and performance. Many of them will be present at the Health & Safety Event 2025, giving you the perfect opportunity to explore their offerings firsthand. Share Your PPE Story The PPE Saves campaign highlights real-life impact. We invite workers, employers, and safety professionals to share their experiences. Has PPE saved your life or that of a colleague, prevented an injury, or improved your working conditions? Join the conversation and help raise awareness by sharing your story on social media using #PPESaves. For PPE that protects lives and helps workers and businesses to thrive, visit: www.registeredsafetysupplierscheme.co.uk Alan Murray is chief executive of BSIF. For more information, visit www.bsif.co.uk |
|
|
|
BSIF membership for professionals | 18/02/2025 |
FOR THE first time BSIF are now asking Health & Safety Professionals /duty holders/ category managers/ buyers, employers and or employees to become members of BSIF in their own right. To facilitate this, BSIF have launched a free membership pilot. The Pilot seeks to deliver a structure by which BSIF can engage, embrace and support duty holders and safety professionals/ compliance managers in all things in PPE/Safety products. There is no cost for Pilot membership, during the Pilot we will forge a form of membership that works for you, the BSIF and the wider safety industry within the UK. The British Safety Industry Federation (BSIF) is the Trade Association for the safety industry and acts as a leading voice for the sector. Set up in 1994 the Federation has some 400 members representing the complete supply chain including manufacturers, importers and distributors of personal protective equipment (PPE) and safety products, through to test houses, certification bodies and specialist safety service providers. The following give a brief overview of the Pilot membership benefits. PPE Helpline The BSIF Members PPE Helpline has been set up to reduce the complexities of PPE & Safety Products and to become the ’Go To’ for information not always easily obtainable in the market place. The BSIF PPE Helpline is administered by PPE & Safety experts ready to assist with any questions relating to a variety of areas including product queries, standards information and help in understanding compliance of different products. The pandemic shone a light on the need for people to be able to access free non commercially biased information. BSIF’s new helpline will cover areas such as:
ACCESS TO BSIF MAILINGS BSIF communicate information that keeps you ahead of the curve. Our mailers arrive into your inbox and cover: • Government updates • European PPE/Safety Information • Standard changes • BSIF member events • Industry opportunities BSIF INDUSTRY CAMPAIGNS BSIF have produced campaigns to raise awareness of H&S issues. They highlight what can happen when personal safety is not taken into account. BSIF want to engage with Pilot members to develop new campaigns and posters to help people avoid hazards that can affect their life now and in the future. BSIF SPECIAL INTEREST GROUPS (SIG’s) BSIF have a structure of PPE/ Safety product SIGs focusing on all relevant issues within the sector. Working directly with Pilot members we will be introducing a new user group to collaborate and support the existing. The user group will receive pertinent information from the SIG’s and feedback valuable opinion and industry experience. BSIF QUALIFICATIONS BSIF Pilot membership gives access to industry courses & qualifications at discounted rates. For example a new publicly recognised qualification for specifiers/buyers of PPE/Safety products. This qualification will help provide the tools needed to procure compliant & safe product. It includes: • Legal requirements • Standardization processes (EN/ISO standards) for PPE/Safety Products • Market Surveillance • Safety In the Workplace • PPE EN standards information BSIF EVENTS BSIF will run Pilot member events designed to inform, educate and network. Giving the opportunity to meet with BSIF Economic Operator members from within the supply chain and other HSEQ members & Duty Holder (Pilot) members. BSi COMMITTEES: BSIF are a nominating body for BSI. We can refer our members directly into BSI PH/Horizontal committees. These committees plug into CEN/ CENELEC/ISO working groups. If you want to get more involved in technical standards in PPE you can do so through a BSIF – Bsi referral. If the BSIF Pilot Scheme sounds of interest to you please contact us by email to [email protected] |
|
|
|
Shocking 90% of PPE from non-registered providers fails tests | 24/02/2025 |
THE BRITISH Safety Industry Federation (BSIF) has issued an urgent warning to those responsible for procuring personal protective equipment (PPE) and safety products following the results of its latest independent tests. These findings once again reveal the alarming prevalence of substandard—and potentially hazardous—products circulating in the market. Between December 2023 and December 2024, the BSIF tested 161 products from non-member suppliers, assessing their advertised performance, labelling accuracy, and compliance with relevant standards. Alarmingly, only 10% (16 products) met full compliance requirements, while an overwhelming 90% (138 products) failed to meet the necessary criteria with seven test results still pending. Particularly troubling was the finding that in some categories, including head protection, eye & face protection and fall protection, every non-member product tested (100%) failed the assessments. Even more concerning is the fact that many of these substandard products are still available for purchase, placing unsuspecting users at significant risk. Key problem areas Failures were identified across all product categories, with some showing particularly alarming issues:
The tests and assessments were conducted in accordance with the requirements of the PPE Regulation and are vital for ensuring that only safe and effective products are placed on the market. BSIF member test results The non-member test results are vastly different from the results of tests conducted on products supplied by BSIF Registered Safety Suppliers, who are committed to selling only certified PPE and trading honestly and ethically. Of the 399 tests completed on products from Registered Safety Suppliers between December 2023 and December 2024, 86% – 322 products – passed. Even for the 14% – 51 products – initially falling short, all issues were promptly addressed and rectified, while 24 results are still pending. Check for the BSIF Shield For buyers and end users seeking assurance, the BSIF Shield is a respected mark of credibility. Companies displaying this shield have pledged a binding declaration that their PPE and safety equipment meets the correct performance standards, fully complies with regulations, and bears the necessary UKCA and/or CE markings. Choosing a Registered Safety Supplier helps to ensure not only genuine products fit for purpose but also authentic information and guidance. Commenting on the latest statistics, BSIF CEO Alan Murray says: "People are continually surprised by the sheer volume of PPE and safety products that fail to meet basic safety standards. What's even more shocking is that, despite vendors being informed of these deficiencies, such products often remain on the market, continuing to expose unsuspecting buyers and users to significant risks. "Our latest test results have once again brought to light a deluge of problem PPE, from substandard safety helmets to safety shoes that fall a long way short of the required standards for keeping wearers safe. "Buyers and specifiers must urgently review their procurement processes and consider what assurances they have that the PPE and safety equipment they are being supplied with is fit for purpose.” BSIF Registered Safety Supplier Scheme manager Roy Wilders adds: "The findings are deeply concerning. When protective—and sometimes life-saving—equipment fails to meet standards, it's not just a statistic; it's a potential tragedy waiting to happen." “The dedicated RSSS team works tirelessly year-round, assessing members of the scheme to ensure compliance with stringent requirements and actively monitoring the market to identify and address substandard products. However, buyers also have a critical role to play. By verifying the credentials of their PPE and safety equipment suppliers, they can help eliminate the market for substandard goods and prioritise safety above all. “Checking for the BSIF Registered Safety Supplier shield is the easiest way to ensure you only deal with compliant, competent and trustworthy suppliers. Remember, anyone can sell safety, but you shouldn't buy safety from just anyone; always check for the BSIF shield." Resources for buyers • Download the BSIF's PPE purchasing checklist: Check Your PPE • Find a full list of Registered Safety Suppliers: Registered Safety Supplier Scheme |
|
|
|
From the CEO's desk | 25/02/2025 |
WITH A concerning presence of substandard PPE on the market, Alan Murray looks at the results from the BSIF’s product tests and explains how you can ensure you are buying compliant products. Each year, the British Safety Industry Federation (BSIF) tests and assesses a wide variety of personal protective equipment (PPE) and safety products available in the UK to check products perform as advertised. These evaluations cover products from both BSIF members and non-member suppliers, checking for compliance with the requirements of the PPE Regulation which is critical for guaranteeing that only safe and effective products reach consumers. Consistently, these tests reveal a worrying number of non-member products failing to meet the necessary safety standards. However, this year’s results are particularly alarming. Between December 2023 and December 2024, the BSIF tested 161 products from non-member suppliers, with a shocking 90% failing to comply with safety requirements. Only 10% of the products met the required standards, highlighting a deeply concerning trend and underscoring the urgent need for increased scrutiny and enforcement within the industry. This is not an isolated occurrence. The failures were evident across multiple categories of PPE, including head protection, eye and face protection, and fall protection, where every product tested failed to meet the necessary requirements. It is sobering to consider the potential consequences of these failures. Let’s not forget that faulty helmets, ineffective fall arrest systems, and inadequate protective eyewear are not just regulatory issues; they represent real risks to the safety and wellbeing of workers. In categories such as safety footwear and hearing protection, failure rates stood at 86% and 90% respectively. Alarmingly, many of these products are aggressively marketed on popular platforms, appealing to buyers with promises of comfort and protection without the necessary backing of rigorous safety testing. In contrast, the results from tests conducted on products supplied by BSIF Registered Safety Suppliers present a markedly different picture. Of 399 products tested from these suppliers, 86% passed the assessments. For the 14% that initially fell short, corrective actions were promptly implemented. This reflects not only the commitment of these suppliers to safety and compliance but also the effectiveness of robust quality assurance processes. The BSIF Registered Safety Supplier Shield serves as a clear indicator of credibility. Companies displaying this mark have made a binding commitment to provide products that meet stringent safety standards and comply with all relevant regulations. The BSIF shield represents a supplier's dedication to safety, quality, and responsible trading practices. The presence of substandard PPE on the market pose tangible risks to health and safety. Ineffective respiratory protective equipment can lead to serious occupational illnesses, while inadequate high-visibility clothing can result in preventable accidents. Substandard gloves, footwear, and hearing protection expose workers to unnecessary hazards. With substandard products so prevalent, procurement professionals, safety managers, and end-users adopt a more cautious and informed approach to sourcing PPE. This includes scrutinising the credentials of suppliers. Are they registered with reputable industry bodies like the BSIF? Do they have a proven track record of compliance? What quality assurance measures do they have in place? Education and awareness play a crucial role in addressing this issue. Procurement teams must be trained to identify potential red flags, such as vague certification claims or suspiciously low prices. While the BSIF continues to monitor the market and advocate for higher standards, the responsibility for ensuring safety does not rest solely with regulatory bodies. Buyers and specifiers have a pivotal role to play. By choosing Registered Safety Suppliers, you can drive positive change and help eliminate substandard products from the market. Don’t forget the BSIF offers valuable resources to support buyers, including the "Check Your PPE" purchasing checklist and a comprehensive directory of Registered Safety Suppliers. These tools are designed to help organisations make informed decisions and maintain high safety standards. The BSIF is dedicated to challenging the supply of substandard PPE and safety products in the UK. As part of this commitment, the Federation will be launching the "PPE Saves Lives" campaign in April. This initiative aims to raise awareness about the critical importance of sourcing and using suitable PPE, reinforcing the message that safety should never be compromised. Alan Murray is chief executive of BSIF. For more information, visit www.bsif.co.uk |
|
|
|
Diversity in PPE | 10/12/2024 |
THE ARGUMENT that there’s a requirement for PPE that meets the needs of a diverse workforce is not a hard one to make; people are safer when they have the right PPE that’s correct for their body type, in the specific environment in which they are working. Where historically, innovation in the PPE world has been predominantly focused on functionality, in the last 5-10 years there has been a general shift where brands have acknowledged the need to stock a wider range of products, addressing the needs of more people. Today, there are more products available that take into consideration a person's size, body shape, gender, or religious beliefs. There are even products that address the needs of pregnant women as they move through maternity, brands have realised that pregnant people do need to work and yes, they still need protecting (perhaps more so!). But we’re not there yet. In HSM PPE Insights Survey results, many replies cited that sizing was an issue, with “a lack of options for women” across the whole PPE spectrum being a continual issue, with comments such as “Sizing for women – pink it and shrink it doesn’t work”. With movements such as Bold as Brass and the work of organisations such as the National Association of Women in Construction (and many more) resonating so well recently, the frustrations are clearly there and have been building for the people who wear PPE day-to-day for their whole careers. And it’s not just damaging for those who have suffered over the years, a lack of appropriate safety equipment can only affect recruitment in a negative way, whether that be through people not seeing that they are already represented in these industries or whether they quickly realise that they are not provided for once in the role. So, with the ongoing progression of manufacturing brands and with more products coming to market all the time, we must now address why these survey responses persist and address the additional barriers. Firstly, just because these new products exist, it doesn’t mean that they immediately meet the needs of the wearer. As products become less generic, it becomes more difficult for manufacturers to meet their requirements, manufacturers that create poor products with a “diverse message” will soon be found out; those who have been frustrated for decades will not stand for it. Extended research and development time and an understanding that products may not be perfect the first time, coupled with an attitude of continual improvement from wearer feedback is essential. Feeding information up and down the chain is the key to ensuring the progression of PPE for those currently marginalised. Only by receiving constructive feedback from wearers can the manufacturer know that improvements need to be made, only by having a culture of listening and action, can a manufacturer make these changes a reality. Manufacturers must work tirelessly to make sure their distributors know that these products exist, but also effectively convey their benefits to users as well, alongside engaging with end users where possible. Distributors must ensure they are aware of these products and actively make them available to their customers, championing them over the generic and encouraging purchasers that the personal approach to PPE is the best one. Again, this argument isn’t a hard one to make. Someone who is given a product that meets their needs knows that their employer cares, and knows they are valued and respected. This makes it a sustainable approach too. As businesses continue to scrutinise their impact on the environment, they need to not only look at the way in which the products are made but also ensure that wearers are actually getting products that fit them and meet their needs. The proverb ‘respect begets respect’ comes in here; people who are given products that show they are safer, respected, cared for and valued are more likely to respect the products they are given. They are more inclined to care for that product in line with a user information sheet and less likely to request a replacement before it's necessary. This way products will last longer and be replaced less frequently. Availability is another barrier. Unless manufacturers invest in products that meet the needs of a smaller cohort, they cannot expect that cohort to grow, the onus is on them to push progression and for the rest of the chain to follow suit. Manufacturers and distributors must do everything they can to strive for price equity. Ordering more products in smaller quantities will inevitably cost them more but they must not use niche as an excuse for profiteering. Employers must see the value in tailoring their PPE to their employees or the whole system falls down. Great things are happening, which must be celebrated, but not without a huge dose of humility from all members of the supply chain that they all haven’t yet done enough. So, whilst many barriers still exist to getting the right products worn by the right people for the right environment, many great advances are happening throughout the supply chain. The vital key to ongoing progression is an attitude of feedback that leads to action at all touchpoints within the chain. If we all stay committed, our industries will have happier workers, a more diverse future and we can consign these remaining barriers to the bin. |
|
|