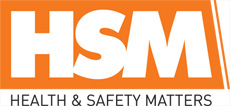
![]() |
Mark Sennett
Managing Editor |
![]() |
Kelly Rose
Editor |
Home> | Managing Health & Safety | >Lone Worker Protection | >High risk in small space |
Home> | Premises | >Risk Management | >High risk in small space |
High risk in small space
07 November 2022
Confined space working carries many challenges. Gillian White highlights the importance of maintaining training programmes for such high-risk environments.

WHILE MANY of the experiences of living and working through the Covid-19 pandemic are beginning to fade from memory, there are some things we learned to do differently that will continue to influence our approach to the ways we work.
Communicating with colleagues through video calls has grown into an accepted way of life and can bring real benefits. Meetings can take place quickly and over long distances, where previously extended travel time away from the office and home would have been necessary. During the pandemic, critical training was able to continue under challenging conditions and some of these experiences continue to play a role today in keeping the nation safe.
For those working in high-risk environments, staying up-to-date with regulations has never been more important and we now know that there are alternative ways of receiving that training that need not involve extended periods away from work and a traditional classroom session. However, a reduction in task-based activity will undoubtedly result in skills fade. The possible consequences in high-risk industries, such as confined space working, are plain. Health and safety training must remain a priority to ensure that a restructured workforce can cope with high-risk environments and the inevitable skill gaps that can occur.
It is vital that any training provides workers with the right balance of knowledge and practical skills to be able to deliver their work safely. It is all too tempting for companies to provide ‘theory only’ training when travel costs are under scrutiny; however, the shortfall in practical skills could have serious consequences, particularly for those working in high-risk environments.
A considerable number of people are killed or seriously injured in confined spaces each year in the UK. This happens in a wide range of industries, such as manufacturing, utilities and agriculture. Those killed include both those working in the confined space and those who try to rescue them without the correct training and equipment. In fact, around 40% of confined space deaths involve people trying to rescue those already trapped or injured. Despite stringent health and safety measures across most workplaces, these statistics highlight that confined space working still poses a considerable threat to employees today.
The existence of confined spaces in some workplace environments is easy to identify and understand. Tanks, vessels, sewers and the like are known to be confined spaces to people in the industry; however, the existence of confined spaces in commercial or non–industrial premises is less well known. Service ducts, loft and void spaces, plant rooms or poorly ventilated rooms are confined spaces often found in commercial buildings, hospitals, universities and residential dwellings. Some confined spaces will also develop during construction, or when work, such as welding or cleaning, is being carried out. These spaces are just as hazardous as those found in industrial environments and demonstrate that systems of safe working must be put in place in every environment.
Given the high-risk involved in working in environments, like confined space, it is vital that businesses and organisations consider several factors.
Regulations
The basis of British health and safety law is the Health and Safety at Work etc. Act 1974 (HSWA). The Act sets out the general duties which employers have towards employees and members of the public, and employees have to themselves and to each other.
In the UK, the Confined Space Regulations 1997 is the legislation that specifically relates to the identification and management of confined space working and the regulations are published with an accompanying Guidance and Approved Code of Practice (ACOP) (HSE L101).
The Management of Health and Safety at Work Regulations 1999 (the Management Regulations) in general make more explicit what employers are required to do to manage under HSWA, and they apply to every work activity.
The PPE Regulation (EU) 2016/425 and the Control of Substances Hazardous to Health state: The risk to health and safety should be assessed on how to prevent or reduce the workers exposure to hazardous conditions and substances.
The Personal Protective Equipment Guidance HSG53 stipulate that Personal Protective Equipment (PPE) and Respiratory Protective Equipment (RPE) is to be supplied and used at work wherever there are risks to health and safety that cannot be adequately controlled in other ways.
The Confined Space Regulations 1997 requires employers to find a reasonably practicable method of completing work in the confined space without entry. This might be remote sampling, inspection or cleaning. However, when the work cannot be achieved by a reasonably practicable remote or outside system, then a safe system of work is required.
Risk assessments
The safe system of work will begin by a competent and experienced person completing a risk assessment. The Approved Code of Practice to the Confined Spaces Regulations 1997 states that, ‘the priority when carrying out a risk assessment is to identify the measures needed so that work in confined spaces can be avoided’. Where confined space working cannot be avoided, ‘then it is necessary to determine what measures need to be taken to secure a safe system for working’. Through assessing the risks associated with entering or working in the confined space, the employer or self-employed worker can then make an informed decision on what specific training, PPE and safety equipment is needed to safeguard employees.
The importance of identifying and understanding the risks, completing risk assessments and implementing regular realistic training cannot be underestimated when it comes to protecting workers. By following the guidance, employers can rest assured that they are safeguarding the health of their employees whilst also significantly reducing the number of confined space accidents in the workplace.
Appropriate controls
Once you have identified that work will be undertaken in a confined space it is important that the right controls are put in place. The Approved Code of Practice (ACoP) L1010 Safe Working in Confined Spaces provides details on the relevant provisions that must be considered. This includes an initial assessment as to whether the work required could be completed without the need to enter the confined space. If that is not possible, then taking the necessary precautions for safe working in a confined space, which will include training, supervision, ensuring safe access and egress, testing and monitoring the atmosphere before and during the procedure, having a reliable communications system in place and suitable equipment for the job.
In the event of an accident, you would need to show you have followed the code or complied with the law in some other way otherwise a court will find you at fault.
Training
Confined space training is essential for those managing or supervising confined space teams as well as those working in confined spaces and for rescue and recovery teams.
Confined space training options range from confined space awareness training, through low, medium and high-risk courses, plus rescue management and training, covering the selection and maintenance of equipment involved in safe confined space working, such as gas monitors, breathing apparatus and personal protective equipment. If the risks are assessed to be too high or the job too complex for in-house teams, you should consider outsourcing jobs to confined space services experts.
Those who are responsible for, or work in, confined spaces should look for appropriate courses. Options available include accredited courses by Awarding Organisations (AOs) such as City and Guilds, or even bespoke training, which can be be tailored to the business needs.
It is important for employers to select the right training courses for their employees. This might include a mix of training methods, such as in a classroom setting or online via an e-learning programme. It may also involve experiential learning, such as practical sessions to provide a more ‘hands-on’ approach, like those available at a purpose-built training facility or through a mobile training unit, allowing participants to practice real-life activities and tasks applicable to their working environment.
Some providers may also offer the opportunity to include the use of virtual reality (VR), allowing learners to experience an immersive environment in a safe and engaging way.
Workers in high-risk industries are often involved in carrying out jobs in industries that are essential for society such as water and utilities, energy generation and distribution or food processing. Their safety is paramount and by working with an expert safety partner, the proper process of risk assessment, safety training and provision of the correct PPE employers and business owners can ensure they follow the correct procedures, meet the requirements of the law and keep their employees safe.
Gillian White is head of marketing communications at Arco. For more information, visit www.arco.co.uk