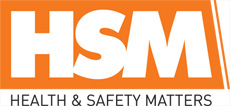
![]() |
Mark Sennett
Managing Editor |
![]() |
Kelly Rose
Editor |
An eye for detail
16 November 2022
Selecting the appropriate safety eyewear lens coatings for the job can be a seemingly complex and confusing issue, requiring a PPE manufacturer with specialist knowledge and a safety manager or eyewear buyer who knows what to look for. Clair Weston says that by following some simple rules, this process can be made straightforward.

Different jobs in different environments carry contrasting risks and therefore require different lens coatings for maximum effectiveness. Safety eyewear buyers look for an array of product merits including quality, innovation, durability, comfort, value for money, whole-life cost effectiveness and good design, but they also need to consider the large variety of available lens coatings before making their final choice. This will depend on the particular situation in which the wearer works.
Correct lens coatings that work intelligently with the wearer provide the best possible optical clarity, efficacy, safety and wearer comfort, and so choosing the right coating for the right activity to ensure the specs are worn by those who need them, is vital. Lens coatings encourage and improve compliance because workers are more likely to keep their eye protection on when they are able to see their work clearly – there is little point in employers providing protective eyewear if workers won’t wear it.
Advantages of lens coatings
Using improved technology and manufacturing methods, safety eyewear lens coatings are now produced for almost any application. High-tech, permanent, lens coatings bring a host of benefits to the wearer. They not only improve vision indoors or outdoors, but they also protect against fogging, UVB/UVA and infrared radiation, scratching, chemicals, glare, dust, sparks and static electricity. In addition, the coatings keep the lenses of the eyewear freer from contamination and cleaner for longer, making dust, aqueous and oily marks easy to remove and increasing the lifespan of the eyewear.
However, coatings must be appropriate to the task in hand. If unsuitable lens coatings are used, unwanted consequences such as eye irritation, lack of compliance and confidence in PPE, low worker morale, and subsequently reduced efficiency. Obviously, a happy workforce makes for good productivity.
Types of safety eyewear
The suitability of safety eyewear varies with the job and the industry. Wrap-around safety glasses are very effective for protecting eyes from mechanical risks such as flying wood or metal particles in a workshop, for example. Safety prescription eyewear which is made to the wearers’ individual prescription eliminates the need for overspecs thus enhancing comfort.
Safety goggles also provide impact protection but fit more tightly around the eyes so they provide a greater degree of protection from all angles. They are ideal for protection from chemical splash, for example, and are most effective if they have anti-fog coatings, to compensate for the lack of air flow within them. Many designs also fit over prescription eyewear giving the required protection level or special prescription inserts further enhance comfort for frequent users.
Types of lens coating
Certain lens coatings are appropriate and effective for some jobs, but not for others. For example, coated lenses that are permanent anti-fog on both sides, scratch resistant and antistatic are particularly suitable for work in high humidity or polluted circumstances, while extreme coatings which separate anti-fog and scratch resistant lens coatings allowing them to perform at a much higher level and on the side of the lens where the coating is needed most, are ideal for work in tough and dirty environments.
In welding, a grey-tint welding filter lens, as well as providing 100% ultraviolet and infrared protection and glare reduction, also gives perfect natural colour recognition, unlike traditional green-tinted welding lenses, which can alter colours. Correct colour vision is vital in welding tasks where safety can depend on the accurate recognition of colours in safety signs and signals in environments such as foundries, steelworks, aerospace or engineering. Coatings can also minimise the impact of sparks on the lens during welding.
In workplace settings with a high risk of small particles, dirt and dust flying around, such as in steel making, mining or construction, highly scratch-resistant coatings are a must, preferably on both sides of the spectacle or goggle.
In working situations such as in paper, food, textiles and refrigerated warehouses with high humidity levels and persistent condensation, permanent, hydrophilic fog-resistant coatings are essential for safe and non-interrupted effective working.
In the past, anti-fog coatings used to wear or wash off quickly, so their permanence is a big step forward in increasing performance and life span of a product even after repeated cleaning. The modern hydrophilic coating becomes sponge-like, absorbing moisture without becoming saturated, so that the wearer does not have to take off their spectacles or goggles to clear any fog, enhancing both safety and wearer compliance.
Chemical - and biological - resistant coatings are needed for whenever chemicals are worked with, especially in medicine, food and waste management. They are also needed to protect against hazardous liquids, toxic dust, gas and vapours.
In jobs that require frequent change from indoor to outdoor environments, a 20% silver mirror sun tint lens could be used to allow workers to see in both light environments.
Different lens coatings can also be used for highly specialised laser applications, such as in medical, dental and industrial situations.
Selecting the right lens coating
So how can eyewear procurers decide on the perfect lens coating for the job in hand and the relevant working conditions? Good manufacturers can assist companies in selecting the proper eyewear and lens coatings for specific work environments. However, it should not be a difficult or daunting task and it is, in fact, very easy to make the right choice using a foolproof coatings selection system, which caters for most working conditions and industries.
The most efficient way to do this is to use a ‘spider graph’ selection chart. With this method, it is easy to plot and opt for the right coating for the right job, so eliminating wasteful trial and error, saving time and costs, and increasing efficiency.
The method is straightforward. The workplace conditions in terms of temperature (hot, cold) are entered on the horizontal axis of the chart, the air humidity (dry, wet) is described on the diagonal axis, and the degree of dirt (dirty, clean) specified on the vertical axis. When these three points are joined to form a triangle, the largest area will indicate the appropriate lens coating for the defined area of use.
A set amount of choices is available to cover most working conditions, so making the selection of the right lens coating for a particularly function very simple.
Conclusion
Selecting the right eyewear and appropriate lens coatings is not difficult, and gives the best chance of user compliance, leading to a safer workplace, fewer eye injuries and increased productivity.
Clair Weston is marketing manager at uvex. For more information, visit www.uvex-safety.co.uk