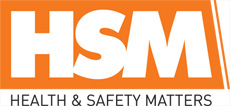
![]() |
Mark Sennett
Managing Editor |
![]() |
Kelly Rose
Editor |
It’s time to get a grip
03 August 2022
Niall Robinson discusses the importance of appropriate and effective hand protection.

HAND INJURIES are the leading cause of all workplace injuries across the UK. In 2021 alone, there were 17,070 non-fatal workplace injuries affecting the hands and wrists, making up 25% of all non-fatal injuries at work.1
The vital role our hands play in almost all forms of work also means they can be exposed to a multitude of hazards. Hand and wrist injuries can end up costing both employers and workers dearly.
Incidents may result in fines, compensation payments, increased insurance premiums and lasting damage to an organisations reputation. Financial impacts aside, for individual employees, the personal impact of their hand injury can be financial, physical, and emotional and may even be life changing. Adequate hand protection and worker education is vital to prevent these worse case scenarios.
Identifying hazards and managing risks
Under the Personal Protective Equipment (PPE) at Work Regulations 1992, employers have a duty of care to ensure the health, safety, and welfare of their employees whilst at work. The first step in doing so is to identify any potential hazards. Whilst this is often a simple process, a thorough risk assessment is usually necessary. It’s important to ask yourself: ‘What is it about the activities, processes or substances used that could harm your employees’ hands?’
Having identified all hazards associated with an activity and the level of risks each creates; employers need to manage them responsibly. It is important to establish what kind of hand protection and safety approach is required. An employer should consider seriousness of the risk, frequency and duration of exposure, and characteristics of the workstation. When it comes to reducing hand injury risks, this includes providing the correct protective gloves. Whilst hand protection can reduce hand injuries by up to 60%, it is important to also educate workers properly on ways to mitigate risk of injury.2 Gloves should be treated as an additional level of protection, not a complete solution.
Mechanical hazards
When it comes to mechanical hazards there are three notable injury risks to the hand, grazing, lacerations, and puncture. Workers are therefore required to wear EN388:2016 certified gloves to appropriately reduce injury risk.
Injuries are more likely to occur if the wrong gloves are worn or if they’re ill fitted, so It’s essential to use the most appropriate hand protection for the right task, However, users should still be encouraged to use caution and care when handling sharp tools and materials. It's important to train workers on prevention techniques, for example:
-
Know how to handle tools and equipment and use the correct one for the job.
-
Comply with controls and use techniques to avoid putting hands in dangerous places.
-
Work at an appropriate pace and stay alert.
-
When working with powered blades or other sharp rotating equipment, machine guarding needs to be in place to prevent contact.
Chemicals
Gloves labelled as ‘chemical’ (certified as EN374:2016.) are often used without checking their level of protection against specific substances being handled. There is huge variation in protection level and exposure tolerance under the same rating, meaning that 70% of Health and Safety professionals risk choosing gloves that don’t promote the level of protection they think they will. As chemical hazards are classed as category III, mortal or irreversible, it is vital users select the correct certified hand protection.
In the first instance, efforts should be made to eliminate the use of chemicals, or swap for less hazardous ones. Where this isn't possible, exposure should be limited. Employers should ask: ‘Can exposure be shortened, or can tools be used to handle contaminated goods?’
Many, even every day, chemicals are hazardous, with accidental contact resulting in adverse reactions ranging from minor skin irritation to third-degree burns and absorption into the bloodstream. The effects can be short term but also long term and life changing.
Users need to always ensure that the wright gloves are selected to protect against the specific chemicals being used and always respect the permeation times as advised by your PPE provider.
Handle, store and dispose of hazardous materials safely and don’t mix them unless you know it won’t cause a dangerous reaction. The workplace must have arrangements in place to deal with chemical exposure incidents.
More information on chemical protection gloves is available at: https://campaigns.arco.co.uk/riskseepingin/#lp-pom-block-129
Harmful micro-organisms
COSHH specifies what containment measures are required for biological agents. Regardless of classification, protective gloves play an important part in protection.
For example, healthcare and laboratory workers may be at risk from blood-borne viruses and require an EN374-5:2016 glove to protect against bacteria fungi and viruses, especially where there’s also the risk of cut or puncture injury. In other industries, such as in construction, the need for care isn't always as obvious, so education and training play a large part in avoiding hazards and minimising exposure. Extra consideration should be made for anyone who is more susceptible to infection, for example, because of pre-existing disease, medication, compromised immunity, or pregnancy.
Hot thermal hazards
Minimising injuries to hands associated with working in environment where there are thermal hazards has to include the use of EN407:2020 gloves to protect against burns caused by contact, convective or radiant heat as well as coming to contact with small and large molten splashes, but other practical measures can be taken too, for example, a work piece can be clamped instead of holding it by hand.
Warning signs, devices to avoid contact, better designed work areas and removing slip and trip hazards can all contribute to preventing hand injuries in the workplace from heat sources.
Fatigue and hand-arm vibration
For both these risks, working practices and patterns should be examined and exposure time restricted.
It is the employer's duty under the Control of Vibration at Work Regulations 2005 to ensure workers are not above the daily exposure limit.
Reduced blood circulation in the fingers increases the risk of hand-arm vibration, so ensure workers have gloves and other warm clothing in cold conditions.
Electrical
When working with electricity, suitable precautions should be taken to reduce the risk of contact with live or earthed components. Appropriately rated EN60903 insulating gloves should be considered a final defence against electrical shock.
Training wearers
As these examples have illustrated, appropriate training to ensure workers understand safety control measures is just as crucial as adequate hand protection.
In addition to supplying hand protection, employers must ensure all staff are properly taught how to use their gloves and how to maintain or replace them.
Workers need to be educated around safe working practices, particularly if pre-existing habits need to be overcome, such as not removing gloves at critical times. Particular care is also needed to ensure new behaviour is adopted when working circumstances change.
References
1 Workplace Injury Statistics UK 2021
2 A case-crossover study of transient risk factors for occupational acute hand injury
Niall Robinson is hand protection expert at Arco. For more information, visit www.arco.co.uk/expert-advice/hand-protection