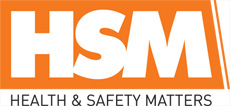
![]() |
Mark Sennett
Managing Editor |
![]() |
Kelly Rose
Editor |
Home> | Breathing Safely | >Respirators | >Why RPE matters |
Why RPE matters
13 April 2017
Luca Favarin, product manager EMEA, respiratory protection, Honeywell Industrial Safety, says RPE matters when it comes to tackling work related respiratory illnesses.
Occupational respiratory illness is a serious concern across industries. And there are signs that many companies are still neglecting their duties to workers in this area.
According the recent British Safety Industry Federation’s (BSIF) report, Tackling Work-Related Respiratory Illnesses, every year 30,000 UK workers suffer from breathing or lung problems and 12,000 die from respiratory illness. Strikingly, as the report concludes, the correct respiratory protective equipment (RPE) “correctly used and correctly fitted can prevent the vast majority of these deaths.”
There is still a tendency among workers to either not wear RPE or not wear it correctly. This is a problem that could easily be solved by providing workers with a more comprehensive choice of RPE and appropriate training on how to use it. However, some employers may see investing in new RPE and training programmes as a cost, failing to understand the long-term benefits that this can bring to the business.
Take fit testing. Some employers may see this crucial assessment of RPE’s performance, which is now compulsory in the UK, as being detrimental to business productivity. If performed correctly, the test, which has to be run on each worker individually, should take approximately 30 minutes and has to be repeated if it fails, which can result in downtime for the company. Additionally, the employer has to pay for the service offered by a competent trainer and a sensing device to assess the RPE’s performance.
However, there is now evidence that failing to invest at the very start can result in respiratory disease in the long run, which can turn out to be more costly for the business. For example, last year 25.9 million working days were lost due to work-related illness, which cost the UK’s economy £9.3 billion. The Health & Safety Executive estimates that a worker who is absent from work for more than seven days due to ill health will cost the employer £ 8,000 on average.
With these figures in mind, a risk assessment should always be the first step of any safety strategy aimed at tackling respiratory illness. This should include knowing the type of pollutants that workers are exposed to and their concentration levels, which is essential to selecting the right RPE.
Legislation will play a key role in giving employers, safety managers – and ultimately workers – more assurance that the RPE they select meet the latest quality standards. The new PPE Regulation (EU) 2016/425, set to come into application in April 2018, will introduce a five-year validity period on EU Type Examination Certificates, meaning more regular and strict assessments of the quality of PPE.
However, the quality standards and performance levels that a piece of RPE will claim don’t necessarily translate into total protection, with recent research showing that up to 50 percent of all RPE used does not offer the wearer the level of protection it declares because it simply does not fit their face. For example, having a beard can prevent the RPE to seal the user’s face completely unless alternative forms of RPE that do not rely on a tight fit to the face are available.
With this in mind, fit testing is key to ensuring that the equipment selected is suitable for the wearer. The test is performed by releasing a mixture of salt and water in the environment. If the RPE is not fitted correctly or doesn’t fit the user’s facial morphology, the test will show, through the use of air sensors, the quantity of particles that the RPE is failing to keep out. In the UK, it is a legal requirement that the test is performed by a competent person and the BSIF has also developed a competency scheme for Fit Test Providers - the Fit2Fit Accreditation Scheme – which is designed to confirm the competency of any person performing face piece fit testing.
Whereas fit testing should always be performed at the RPE selection stage, it is also vital to make sure that workers continue fitting their RPE correctly over time, reinforcing their awareness through regular training. It is extremely important that workers wear their RPE correctly and check for a good fit every time and this is where technology comes in.
The growth in IoT (Internet of Things) means ‘connected’ RPE will enable safety managers to access vast streams of data that can be used to ensure workers receive the right training in the use of their protective equipment and that this is up to date, well-maintained and fit for purpose. More importantly, the latest technology enables businesses to develop an overall safety ecosystem to monitor, track and control exposures.
This approach can be used to not only help prevent occupational illnesses, but also enables businesses to make informed decisions quickly and so reduce costs and downtime whilst increasing worker productivity. Workers can concentrate on the job at hand rather than worry about whether their equipment is working properly.
The Tackling Work-Related Respiratory Illnesses report along with recent campaigns like the Health and Safety Executive’s Helping Great Britain Work Well are welcome and demonstrate that the safety industry’s awareness and knowledge of previously neglected long-term ill health is growing. A strong health and safety culture that values the importance of investing in the latest RPE technology and training should be at the very centre of this approach and inform the safety strategy of UK employers moving forward.
- Disposable respirator offers durability
- Respiratory protection urged
- Welding talk
- Combo passes fit test
- Double protection at half the price
- 3M advanced three-panel design optimises comfort
- Flexible fit disposable respirator
- 3M Pioneers advanced disposable respiratory protection technology
- Respiratory & personal protection
- Latest respirators