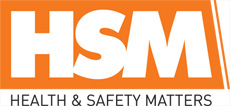
![]() |
Mark Sennett
Managing Editor |
![]() |
Kelly Rose
Editor |
Home> | Premises | >Risk Management | >CO2 safety in the drinks industry |
CO2 safety in the drinks industry
06 April 2016
Carbon dioxide (CO2) is commonly used in the manufacture of popular beverages, and large storage cylinders are used for local dispensing of soft drinks, lager and beer. Louise Early, strategic industry manager at Crowcon Detection Instruments, discusses the use and potential hazards of CO2 in the food and beverage industry, as well as how the use of gas detection can contribute to keeping employees safe that are involved in the supply, delivery and maintenance of equipment.
Carbon dioxide (CO2) occurs naturally in our atmosphere at very low concentrations, and we produce it when we breathe out. It is heavier than air, and if it escapes, it will tend to sink to the floor, where it can form deadly, invisible pockets. Monitoring oxygen (O2) levels will help protect you against asphyxiation, but it is poor precaution against the toxic effects of lower levels of CO2. At almost 80% volume, nitrogen (N2) comprises the majority of normal air. This means that, if a CO2 release occurs, most of the gas that it displaces will be N2. In the event of a leak of CO2, the percentage increase of CO2 is not matched by a similar decrease in the O2 concentration. This means that carbon dioxide can reach exposure limit levels, but O2 levels could still be comparatively unaffected and so considered safe. An additional danger in this case is that, with high concentrations of CO2, some oxygen sensors give a small upscale signal3 i.e. a falsely high reading.
Exposure limits
The UK Health and Safety Executive set legal limits on the amounts of many of the substances that can be present in workplace air. These are known as workplace exposure limits (WELs) and are listed in the HSE’s booklet EH40 Workplace exposure limits. Toxic exposure limits utilise Time Weighted Average (TWA) calculations, meaning that monitoring personal exposure over time has to be considered. TWA is based on a simple average of worker exposure during an eight hour day. It permits periods of exposure above the TWA limit, but only as long as the short term exposure limit (STEL) is not exceeded and there is equivalent under exposure to compensate. Carbon dioxide has a long-term exposure limit (LTEL) of 5000ppm (0.5% by volume) and a STEL of 15000ppm (1.5% by volume).
Worker safety
Carbon dioxide is used and generated in large volumes within the drinks industry. Arguably the most recognised area with which carbon dioxide is associated is as a by-product from fermentation. It is also used however in a myriad of other areas within the food and drinks industry including:
- As a chilling or refrigeration medium
- To inert spaces either in the form of blanketing or vessel evacuation to reduce oxidation or to inhibit yeast or mould growth
- To pump drinks from one vessel to another
- To carbonate beverages
Confined spaces are defined in the UK as “a place which is substantially enclosed (though not always entirely), and where serious injury can occur from hazardous substances or conditions within the space or nearby.” These spaces are abundant within the food and beverage industry, not only during production but also once the beverage is ready for consumption with pub cellars classed in the UK as confined spaces. Employers have a duty of care to their workers, especially those who enter third-party business premises to perform their duties (service, maintenance, delivery or sales). Providing portable monitors, capable of detecting either CO2 or CO2 and O2, can improve the safety of their working environment.
Detection
Carbon dioxide is all around us, ambient levels range from 300ppm to 400ppm. As such, any detection technology employed must be capable of detecting constant levels, while delivering reliable performance. Electrochemical sensors are low-cost and typically offer an accurate method of detection for CO2, this technology does however rely upon consumable materials within the body of the sensor and so over time becomes ‘used’. Electrochemical CO2 sensors are also limited in terms of performance over temperature ranges. Infrared CO2 sensors offer improved accuracy, are not affected by high levels of gas, at the same time as providing comparable life-time cost.
Limit exposure
Carbon dioxide is a deadly toxic gas. Elevated levels can kill, and every year people in the drinks industry die from CO2 inhalation. This can be avoided. Use of today’s CO2 gas detection technologies, and adherence to recognised best practice, should be at the top of your health and safety agenda.
The message is clear. Use gas detection – please don’t put yourself or your employees at risk from CO2.