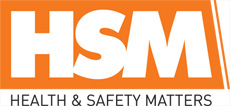
![]() |
Mark Sennett
Managing Editor |
![]() |
Kelly Rose
Editor |
Home> | Managing Health & Safety | >Standards | >Safety culture consequences |
Safety culture consequences
18 February 2015
Research findings from a YouGov survey conducted on behalf of Seton have shown that health and safety is not always prioritised in small and medium enterprises (SMEs), and that a high proportion of accidents at work could have been avoided.

In order to make health and safety a top priority for businesses, a fundamental shift in attitude towards safety is necessary. Stephen Thomas, health and safety technical consultant at Croner Solutions (a business consultancy in the health and safety industry), shares his thoughts on some of the research outcomes and provides expert advice on how to improve safety standards in the future.
The research
YouGov survey findings reveal that 62% of senior decision makers at SMEs admit to a number of barriers preventing them from investing more in health and safety. On top of the usual cost and time constraints, the lack of a healthy safety culture seems to be a key obstacle. 20% of employers surveyed believe that there is too much bureaucracy involved, an attitude particularly prevalent in construction, and 13% of employers stated that employees are often resistant to following health and safety procedures. 21% of senior decision makers held the attitude that health and safety is not that important in their industry. 10% of construction employers held this belief despite the fact that the construction industry accounted for nearly half of all workplace fatalities last year according to the latest Health and Safety Executive report.
Core business issue
Stephen Thomas believes that health and safety "should really be a core business issue...so if you build it in right from the ground floor then the business will reap the rewards". Health and safety needn’t be a bureaucratic nightmare or about spending lots of money. Stephen advises that "businesses shouldn’t focus on filling out forms but on identifying the things that are actually likely to cause people harm and pro-actively taking measures to prevent that. Companies don’t necessarily need to spend money on a health and safety expert, they just need someone with enough competence to manage health and safety issues". He also makes the point that improving practice can not only increase safety but may also improve processes making the business more efficient.
The benefits of a more positive safety culture are clear, and the consequences of a negative safety culture can be fatal. Paul Bizzell from SHP recognises the impact of safety culture at work and recommends that organisations evaluate their own culture in order to understand whether it is having a positive impact on the business and how it can be improved.
In line with this, Seton urges health and safety decision makers to keep a couple of questions top of mind when planning for the year ahead: How can I ensure our safety culture is a positive one that benefits the business? And, ultimately, what is more important than the lives of people in the workplace?
This research forms part of Seton’s Season of Safety campaign to put health and safety at the top of the business agenda.
- Ensuring CDM Regs compliance
- HSE Chair calls for consultants to sign up to new benchmark register for health and safety
- Changes to construction site scaffolding regulations:Are you safe?
- Lessons in safety
- The Corporate Manslaughter Act: Why only 2 prosecutions after 4 years?
- Nationwide gets OHSAS 18001 accreditation
- New procedural guidelines at VdS
- Prevention is better than cure
- NQA prize winners
- Latest register of legislation